INTRODUCTION
Compared to the typical forces usually included in building design, such as wind and seismic, there are many unique considerations involved in blast design. Except for high-threat scenarios associated with military and diplomatic facilities, a blast event is typically considered to be very unlikely but potentially catastrophic. The priority of blast design is to ensure the life safety of occupants and protection of critical assets, and therefore high levels of structural damage may be acceptable. To design a building to withstand any possible blast load event without significant damage tends to be prohibitively expensive, and achieving the balance between the additional costs of blast protection and the costs associated with significant but acceptable damage is often challenging.
For introductory purposes, the source of blast loading can be broadly categorized as either “intentional” or “accidental.” In today’s global political environment, “intentional” primarily refers to an act of terrorism that involves explosives. “Accidental” refers to the many other potential sources of blast loading such as explosions at industrial facilities, crashes of tractor trailers or trains that are transporting energetic materials, deflagration resulting from gas line leaks, etc. However, from a structural engineering standpoint, the design methodology is the same regardless of the source, although the source defines the design load.
Blast design associated with intentional load sources is one aspect of the broader subject of “security engineering.” In commonly used broad terms, security engineering involves detecting the possibility of intrusive behavior, deterring, delaying or denying a potential perpetrator from attacking, and defending people and assets against harm. Any scenario that involves design for an explosion attack will begin with identifying nonstructural approaches for protecting the subject building. For example, simply placing bollards around the building perimeter and restricting access to adjacent garages and parking areas can greatly reduce the blast design load by increasing the distance between the asset and a potential vehicle-borne explosive device, and thereby minimize construction costs. At the same time however, buildings such as embassies that must be constructed in urban settings, do not allow for a large standoff distance, and the only recourse is to design for the potentially intense blast loading. There are many consulting companies that specialize in site, architectural, and operational design and planning for security.
This TEK provides an introduction to the major concerns and challenges associated with design of concrete masonry walls for blast loading and directs the reader to sources for additional information and assistance.
TECHNICAL GUIDANCE, DOCTRINE & CRITERIA
Although blast design is not typically taught as part of college engineering curriculums, there are ample resources available for engineers to learn the basics of security engineering, explosion loading phenomena and blast design. This includes seminars and training courses taught by agencies such as the Federal Emergency Management Agency (FEMA) and the Interagency Security Committee (ISC), as well as through academic centers, companies and organizations around the United States. Standing technical committees such as the ASCE /SEI Committee on Blast, Shock and Impact and the ACI Committee 370 on Blast and Impact Load Effects, play prominent roles in disseminating state-of-the-art practice. There are also several international organizations, conferences, and technical publications focused on protection against blast and ballistic events, such as the International Association of Protective Structures (IAPS, protectivestructures.org), the International Journal of Protective Structures (multi-science.co.uk/ijps.htm), the International Conference on Protective Structures (ICPS), and the International Conference on Shock & Impact Loads on Structures (SILOS).
Several comprehensive reference books related to design for blast protection have emerged over the past several years. Most prominent are: Blast and Ballistic Loading of Structures (ref. 1), Modern Protective Structures (ref. 2) and Handbook for Blast Resistant Design of Buildings (ref. 3).
Some of the most frequently used design guides and criteria include:
- Design of Blast-Resistant Buildings in Petrochemical Facilities (ref. 4)
- Blast Protection of Buildings, ASCE/SEI 59-11 (ref. 5)
- Structural Design for Physical Security: State of the Practice (ref. 6)
- Blast Resistant Design Guide for Reinforced Concrete Structures (ref. 7)
- FEMA-427: Primer for Design of Commercial Buildings to Mitigate Terrorist Attacks (2003)
- FEMA-452: Risk Assessment: A How-To Guide to Mitigate Potential Terrorist Attacks (2005)
- FEMA-426/BIPS-06: Reference Manual to Mitigate Potential Terrorist Attacks Against Buildings (2011)
Historically, many government departments and agencies, such as the Government Services Agency (GSA), Department of Defense (DoD), Department of State (DoS), and Department of Energy (DoE), developed and implemented their own independent criteria and standards. These independent standards compounded the complexity of designing and constructing government facilities. In fact, the Departments of the Army, Air Force, and Navy each had separate standards until the late 1990s. Fortunately however, much of this has been consolidated in recent years with the advent of Unified Facilities Criteria (UFC), Unified Facilities Guide Specifications (UFGS) and products of the Interagency Security Committee (ISC).
The UFC and UFGS documents are applicable to the design, construction, operation, maintenance, and modernization of all DoD facilities. The ISC Security Design Criteria was developed to ensure that security issues are addressed during the planning, design, and construction of all new federal courthouses, new federal office buildings, and major renovations, including leased facilities. Most of these criteria and guidelines are now disseminated in an easy-to-locate format provided by the National Institute of Building Sciences under the Whole Building Design Guide (wbdg.org). In addition, the U.S. Army Corps of Engineers Protective Design Center (PDC) provides information, criteria, and software for protective structures design and security engineering (pdc.usace.army.mil). Most DoD-sponsored research reports are available through the Defense Technical Information Center website (DTIC.mil). The distribution of some of these resources is restricted, but generally any U.S. company with the appropriate credentials can acquire the documents needed to conduct business for the U.S. Government by following instructions provided on the respective websites. Following are some of the most prevalent documents and tools relevant to blast design of masonry and other exterior wall components in government buildings and facilities.
Unified Facilities Criteria
- UFC 3-340-01, Design and Analysis of Hardened Structures to Conventional Weapons Effects (For Official Use Only, FOUO)
- UFC 3-340-02: Structures to Resist the Effects of Accidental Explosions
- UFC 4-010-01: DoD Minimum Antiterrorism Standards for Buildings
- UFC 4-010-02: DoD Minimum Antiterrorism Standoff Distances for Buildings (FOUO)
- UFC 4-020-01: Security Engineering: Facilities Planning Manual
- UFC 4-020-02FA/T 5-853-2: Security Engineering: Concept Design
- UFC 4-020-03FA/TM 5-853-3: Security Engineering: Final Design
- UFC 4-023-03: Security Engineering: Design of Buildings to Resist Progressive Collapse
ISC, GSA, DoS
- The Risk Management Process for Federal Facilities: An Interagency Security Committee Standard (ISC 2013)
- Physical Security Criteria for Federal Facilities (ISC 2010)
- Facilities Standards for the Public Buildings Service (GSA 2010) (superseded by ISC standards)
- The Site Security Design Guide (GSA 2008) (superseded by ISC standards)
- A&E Design Guidelines for U.S. Diplomatic Mission Buildings (DoS 2002)
PDC Software (includes user documentation)
- BlastX: Internal and External Blast Effects Prediction —performs calculations of the shock wave and confined detonation products pressure and venting for explosions, either internal or external, to a structure.
- CEDAW: Component Explosive Damage Assessment Workbook—a Microsoft Excel-based tool for generating pressure-impulse (P-i) and charge weight-standoff (CW-S) damage level curves for structural components.
- ConWep: Conventional Weapons Effects—a collection of conventional weapons effects analysis tools that perform a variety of conventional weapons effects calculations including airblast loads, fragment and projectile penetrations, breach, cratering, and ground shock.
- PSADS: Protective Structures Automated Design System —automates the procedures in UFC 3-340-01 into digitally read graphical tools.
- SBEDS: Single-Degree-of-Freedom Blast Effects Design Spreadsheets—Excel-based tool for designing structural components subjected to dynamic loads using single degree of freedom (SDOF) methodology.
RECENT RESEARCH & DEVELOPMENT ON MASONRY PERFORMANCE UNDER BLAST LOADS
From a blast-response standpoint, unreinforced masonry behaves much differently from reinforced masonry. Unreinforced masonry tends to be very brittle under blast loads, and has been demonstrated to fail catastrophically at relatively low load intensity. Fragmentation of brittle exterior wall components, namely unreinforced masonry and windows (glass), is the primary cause of injury and death when an occupied building is subjected to an external explosion. For this reason, the U.S. Department of Defense (UFC 4-010-01) and the ASCE blast standard (ref. 5) prohibit the use of unreinforced masonry in the construction of new buildings that must be designed to withstand significant blast demands.
Due to the fragmentation susceptibility combined with the widespread use of unreinforced masonry throughout the world, there has been extensive research supported by many agencies in the U.S. and abroad on the use of a variety of materials such as fiber composite laminates, geotextiles, shotcrete with wire meshing and spray-on polymers for retrofitting existing unreinforced masonry for blast protection. Design guidelines and commercially available products have evolved, some of which are included in the documents referenced above, and research on the subject of retrofitting existing unreinforced masonry has recently subsided.
In contrast, because of the ductility provided by the reinforcement and the mass provided by the grout, even minimally reinforced fully grouted masonry provides a high level of blast resistance. The distinction between unreinforced masonry and reinforced masonry is very important because properly designed and detailed reinforced masonry can provide a high level of protection at relatively low cost. Potentially misleading broad statements such as “masonry is considered a very brittle material that may generate highly hazardous flying debris in the event of an explosion and is generally discouraged for new construction” (FEMA-426/ BIPS-06 2011) are intended to reference unreinforced masonry.
Recent full-scale blast testing conducted by the Air Force Research Laboratory (AFRL) (refs. 8, 9) on fully grouted 8-in. (203-mm) concrete masonry walls with No. 5 vertical reinforcement at 40 in. (M #16 at 1,016 mm) on center (one bar at the cell center) and W1.7 (9 gage, MW11) horizontal joint reinforcement 16 in. (406 mm) on center demonstrated excellent ductility under blast loading (Figure 1). That testing involved panels with and without clay brick veneer and polystyrene foam insulation (typical cavity wall construction). The veneer enhances resistance due to the added mass, but does not significantly increase the section moment of inertia through composite action. Furthermore, it was noted that the veneer ties provide sufficient strength and stiffness to transfer the forces from the reflected pressure from the veneer exterior to the structural wythe without significantly loading the insulation.
The second phase of the AFRL masonry test program demonstrated that the ungrouted cells of partially grouted exterior walls tend to breach and turn into hazardous fragments similar to unreinforced masonry, and therefore partially grouted walls should not be used when designing against a significant blast demand (refs. 10, 11) (see Figure 2).
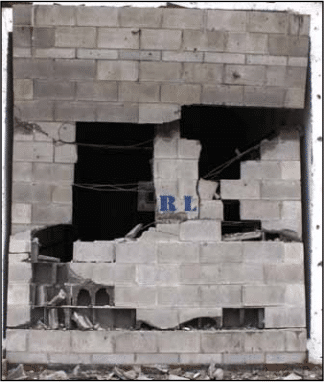
BLAST PHENOMENA AND DESIGN LOAD
The intensity of blast loading on a given structure depends upon several key factors, such as the type of energetic material, distance between load origin and the structure, position of the load origin relative to the ground, the relative orientation of the structure, etc. Explosions external to a building tend to result in a single predominate reflected pressure pulse that is relatively easy to predict. The duration of loading on a building façade from external explosions is typically characterized in milliseconds (seconds/1,000). Forces resulting from internal explosion are significantly more complex to predict due to reflections and gas pressure venting. The duration of the reflection peaks resulting from internal detonations may be only a few microseconds, followed by a longer build-up and release of gas pressure through venting mechanisms.
The most intense loading occurs on forward-facing components closest to the blast origin (reflected pressure), but an explosion that is external to a building can also cause significant side, rear, and roof loadings. Figures 3 and 4 illustrate some of the basic factors involved in explosion loading on structures and the idealized shape of pressure over time. For purposes of exterior wall system structural design, the negative phase is typically (and conservatively) ignored, and the positive impulse is simplified to a right triangle form (Figure 5). Load is defined in terms of anticipated size (i.e., industrial container size, truck-, car- or person-carried explosive device, etc.) and distance between the building component being designed and blast origin (commonly referred to as the “standoff distance”). A close-in blast tends to cause local breaching; far-away blasts tend to result in a flexural response of exterior wall components. The intensity degrades exponentially with distance between subject component and blast origin; therefore one of the primary protection methods is always to maximize the standoff distance. It should be understood that the size of explosive device is not a singular descriptor of the potential level of damage/harm that could be caused—a well-placed satchel device can be more destructive than a truck full of explosives detonated on the street.
Many of the resources listed above describe the blast load phenomena in great detail. Approximate methods for transforming explosive type, size and distance into the peak pressure and impulse required for engineering analysis and design are thoroughly defined in UFC 3-340-02 (ref. 12). Airblast calculators such as CONWEP are also available, and some engineering analysis software such as SBEDS, WAC, and LS-DYNA include embedded blast load calculators. Accurate analysis of internal detonations or explosions that may involve multiple reflections requires advanced shock analysis and computational physics codes.
Some government provided documentation and software used for blast load prediction is restricted as “for official use only” (FOUO), but general airblast load methodology and calculators are not sensitive and can be openly distributed. Restriction occurs when the documentation or software contains specific military-use or mission-specific information or capabilities. Therefore, some documentation such as UFC 3-340-01 and calculators such as CONWEP are restricted since they contain weapons effects information. However, any contractor or organization with the proper need and contract credentials can gain access to the necessary information and tools.
DESIGN FOR FAR-FIELD BLAST LOADS
Once the design load has been defined, the structural engineer can proceed with the dynamic response calculations required to analyze the masonry component. In general, blast analyses for designing exterior wall systems are done in the latter phases of design. The components are typically first designed for gravity, wind and seismic loads, and then the design is checked for blast adequacy and altered for blast resistance if needed.
Single-degree-of-freedom (SDOF) response calculations are most common, but some blast design engineers prefer more robust, but more complicated and expensive, finite element analyses. Finite element modeling can provide a more accurate and detailed response simulation, but must only be used by persons with a high degree of knowledge in finite element theory and application.
Response Limits
Component deflection is the first focus of the dynamic analyses for systems that will respond in a flexural mode. The required level of protection (LOP) for individual structural components must be defined during the planning process. Table 1 introduces the damage categorization language typically used. Components are generally categorized as primary, secondary or non-structural, as described in Table 2. Table 3 illustrates the typical terminology used to describe component damage. And, Table 4 is used to relate LOP to component damage. The process and information presented in Tables 1 through 4 may differ slightly between the various standards and criteria, but the overall approach and concepts involved will be essentially the same.
Blast criteria for flexural components are typically written in terms of the allowed ductility (μ) and rotation (θ). As part of the process, the building is categorized according to the level of damage that is acceptable, and then the rotation limit is set according to that level of acceptable damage. “Ductility” is the ratio of the maximum deflection of the component to the yield deflection of the component; “rotation” is defined in Figure 6. The limits for masonry are defined in Table 5.
Analysis Methodology
As mentioned above, single degree of freedom analysis is generally considered to be the standard approach for blast design of flexural components such as masonry walls used for exterior wall systems. Pressure-impulse (P-I) diagrams, also called iso-damage curves, such as those provided through the CEDAW software, can be used for preliminary design or rapid assessment of structural components (ref. 14). The fundamentals of SDOF analysis are defined in commonly-used structural dynamics textbooks such as Biggs, Chopra, and Tedesco et al. (refs. 15, 16, 17), as well as in many of the references discussed above, and the reader must review those sources to fully understand the methodology.
SDOF analysis is not unique to blast analysis of structures; it is a common technique for dynamic analysis of a wide range of structural and mechanical systems. However, some aspects of the resistance definition approach are specific to blast load analyses. The following provides a brief overview of the methodology.
In SDOF blast design, the component, such as a masonry wall, is idealized as a beam subjected to the transient blast load, which is then reduced to the transverse motion of a single point (degree-of-freedom) (Figure 7). Equation 1 is solved numerically for transient displacements up to the peak displacement. The system is therefore comprised of a nonlinear resistance function (translated through time increments into stiffness), a transient pressure loading, and an effective mass. Once the displacement is solved, the peak rotation and other design parameters can then be related to the maximum displacement. The approach can include damping, but damping is typically not important for calculating the first peak displacement of flexural systems subjected to impulse loading.
The resistance function used for reinforced masonry is essentially the same as used for reinforced concrete. The resistance is idealized as an elasto-plastic form for simple (determinate) support conditions, or multi-linear for other support conditions, as illustrated in Figure 8. The ultimate resistance (ru) is defined using resistance definitions provided in standards and engineering guidelines such as Section 6-8: Design Criteria for Reinforced Masonry Walls of UFC 3-340-02 (ref. 12) and Chapter 7—Masonry Components of the SBEDS methodology manual (ref. 18). In addition to the usual material properties, dimensions, etc., that play into concrete static design resistance, the approach used to define the blast resistance also includes factors that compensate for effects of strain rate on material properties. Although strain rate effects are localized and vary spatially and temporally, the approach used in typical SDOF-based blast design is to smear the effect using single dynamic increase factors (DIF) that are applied to the material strengths (i.e., concrete and steel) used in the resistance definition. The dynamic increase factors for masonry are 1.19 for flexure, 1.12 for compression, and 1.10 for direct shear, which are the same as used for concrete (ref. 5). A DIF on yield of approximately 1.17 is also typically applied to Grades 40 and 60 reinforcing steel.
Unreinforced masonry does not exhibit any significant resistance at deflections larger than the yield deflection. Therefore, a brittle flexural response is assumed based on the moment capacity controlled by the flexural tensile strength between masonry units. Increase in resistance due to compression arching, which may be significant, can be considered if the supports are sufficiently rigid and there are no gaps between the wall boundaries and supports. There is no available test data on the dynamic flexural tensile strength of masonry walls, therefore a value of 1.38 MPa (200 psi) is recommended, based on use of this assumed value in SDOF analyses that approximately matched measured unreinforced masonry wall response from a number of explosive and shock tube tests (refs. 13, 14).
The SDOF methodology for nonloadbearing wall components can be easily programmed. However, the axial force effects in loadbearing components xe significantly xm complicate the procedure. The axial load changes the system’s resistance, and P-Δ effects amplify the displacement. Therefore, to incorporate these effects into a SDOF framework, either both (effect of axial load on resistance and P-Δ effects) must be incorporated into the resistance definition, or only the effect of axial load on resistance changes the resistance and P-Δ effects are incorporated through each time step. SDOF calculators such as SBEDS and Wall Analysis Code (ref. 19) developed specifically for blast analysis of wall components are available, some of which include the ability to analyze loadbearing components.
Maximum Shear and Reaction Forces
Shear failure in masonry can occur before the full flexural response mode occurs and can be in the form of diagonal shear or direct shear, as illustrated in Figure 9 (ref. 3). From an SDOF calculation perspective, the reaction force transferred to the connection and the maximum flexural shear force are the same at any point in analysis time. In reality though, the transient force demand on a connection is a function of the connection rigidity, which is not considered in the typical SDOF methodology. For blast design purposes, this demand can be estimated using two approaches:
- as an equivalent static reaction force based upon the flexural capacity of the member, and
- as the maximum of a transient dynamic shear force calculated using SDOF methodology.
The equivalent static reaction force simply comes from balancing the maximum flexural resistance provided by the component, including any strain rate effects (or DIF), with the end or edge support reactions; it therefore does not require calculations involving the equation of motion. This force can be used to check the shear capacity of components and to design the connections. Therefore, it is also referred to as equivalent support shear or equivalent static shear load. Connections are typically designed to have an ultimate capacity that will exceed the equivalent static reaction force. Connections typically have significantly less ductility than the connected components and therefore the ultimate strength of the component should not be controlled by the connections. ASCE/SEI 59-11 also requires that “the design shear forces shall not be less than the shear forces associated with the nominal flexural strength of the element.”
The dynamic reaction force is evaluated from dynamic force equilibrium through time steps. It is a function of the component resistance, inertial effects, and the applied load at each time step. Since high intensity, very short duration fluctuations will occur in the first milliseconds of dynamic reaction force histories, dynamic reaction forces are not usually used to define the maximum shear demand in a component or to design connections. The assumption that the acceleration distribution, and therefore the inertia force distribution, along the span is the same as the deflected shape assumed in the SDOF approach and does not vary with time is not accurate. The deflected shape of blast-loaded flexural components is flatter than the static deflected shape very early in response time, with almost all curvature occurring very close to the supports. At later times, when significant deflections occur, the shape changes to more closely approximate the first mode, or static flexural response shape that is typically assumed in SDOF analyses. For these reasons, among others, the dynamic reaction calculated from standard SDOF methodology is typically not considered to be accurate during very early time response, and the equivalent static reaction force is typically preferred.
Detailing
Proper detailing is critical to achieving the desired ductile failure modes that formed the bases of design and to maximizing the protection capacity of the component. Reinforced concrete masonry components must allow for the full development of reinforcing steel. Longitudinal reinforcement can be placed in several common configurations, as illustrated in Figure 10. The spacing between vertical bars is determined through the standard TMS 402 (ref. 20) design approach that meets the LOP requirements for the building being designed. All cells must be grouted for LOP III and LOP IV. Vertical bars should be placed on each side of control joints. Splices must be tension lap splices for LOP III and LOP IV. Mechanical and weld splices should be limited to regions that will remain elastic under loading and should meet TMS 402 specifications. Reinforced bond beams must be placed at the top of the wall and at all floor diaphragms. Lintels need to be reinforced as well. All horizontal discontinuous reinforcement should be hooked according to TMS 402 for special shear walls – see Figure 10.
REFERENCES
- Hetherington, J., Smith, P. Blast and Ballistic Loading of Structures, CRC Press, 1994.
- Krauthammer T. Modern Protective Structures. CRC Press, 2008.
- Dusenberry, D.O. Handbook for Blast Resistant Design of Buildings. John Wiley & Sons, Inc., 2010.
- Design of Blast-Resistant Buildings in Petrochemical Facilities, American Society of Civil Engineers Task Committee on Blast-Resistant Design, 2010.
- Blast Protection of Buildings, ASCE/SEI 59-11. American Society of Civil Engineers, 2011.
- Structural Design for Physical Security: State of the Practice, American Society of Civil Engineers Task Committee on Structural Design for Physical Security, 1999.
- Smith, S., McCann, D., Kamara, M. Blast Resistant Design Guide for Reinforced Concrete Structures. Portland Cement Association, 2008.
- Browning R.S., Davidson J.S., and Dinan R.J. Resistance of Multi-Wythe Insulated Masonry Walls Subjected to Impulse Loads—Volume 1. Air Force Research Laboratory Report AFRL-RX-TY-TR-2008-4603, 2008.
- Browning R.S., Dinan R.J., and Davidson J.S. Blast Resistance of Fully Grouted Reinforced Concrete Masonry Veneer Walls. ASCE Journal of Performance of Constructed Facilities, Vol. 28, No. 2, April 1, 2014.
- Davidson, J.S., Hoemann, J.M., Salim, H.H., Shull, J.S., Dinan, R.J., Hammons, M.I., and Bewick B.T. Full-Scale Experimental Evaluation of Partially Grouted, Minimally Reinforced CMU Walls Against Blast Demands. Air Force Research Laboratory Report AFRL-RX-TY-TR-2011-0025, 2011.
- Hoemann, J.M., Shull, J.S., Salim, H.H., Bewick, B.T., and Davidson, J.S. Performance of Partially Grouted, Minimally Reinforced CMU Cavity Walls Against Blast Demands, Part II: Performance Under Impulse Loads. ASCE Journal of Performance of Constructed Facilities, 2014.
- Structures to Resist the Effects of Accidental Explosions, UFC 3-340-02. U.S. Department of Defense, 2008.
- Single-Degree-of-Freedom Structural Response Limits for Antiterrorism Design, PDC-TR 06-08 Rev 1. U.S. Army Corps of Engineers Protective Design Center Technical Report, 2008.
- Baker Engineering and Risk Consultants, Inc. Component Explosive Damage Assessment Workbook (CEDAW). Prepared for the U.S. Army Corps of Engineers Protective Design Center, Contract No. DACA45-01-D-0007-0013, 2005.
- Biggs, J.M. Introduction to Structural Dynamics. McGraw-Hill, 1964.
- Chopra A.K. Dynamics of Structures: Theory and Application to Earthquake Engineering. Prentice-Hall, 2001.
- Tedesco J.W., W.G. McDougal and C.A. Ross. Structural Dynamics. Addison-Wesley, 1999.
- Single Degree of Freedom Blast Design Spreadsheet (SBEDS) Methodology Manual, PDC-TR 06-01. U.S. Army Corps of Engineers Protective Design Center Technical Report, 2006.
- Slawson, T.R. Wall Response to Airblast Loads: The Wall Analysis Code (WAC). Prepared for the U.S. Army ERDC, Contract DACA39-95-C-0009, ARA-TR-95-5208, November, 1995.
- Building Code Requirements and Specification for Masonry Structures, TMS 402/ACI 530/ASCE 5 and TMS 602/ACI 530.1/ ASCE 6, Masonry Standards Joint Committee, 2011 and 2013.