INTRODUCTION
Building codes include requirements for minimum reinforcement development lengths and splice lengths, as well as requirements for standard hooks, to ensure the adequate transfer of stresses between the reinforcement and the masonry. This TEK presents these requirements, based on the provisions of both the 2012 and 2009 editions of the International Building Code (IBC) (refs. 1, 2). Masonry design in these codes is primarily based on Building Code Requirements for Masonry Structures (MSJC) (refs. 3, 4). Differences between the MSJC and IBC are noted in the text when they occur.
There are two main differences between the 2008 and 2011 editions of the MSJC that impact reinforcement development and splice lengths in the corresponding 2009 and 2012 editions of the IBC:
- under 2011 MSJC allowable stress design, the allowable tensile stress, Fs, of Grade 60 steel was increased from 24,000 psi (166 MPa) to 32,000 psi (221 MPa), and
- the 2011 MSJC includes new lap splice length provisions for when confinement reinforcement is used at lap splices.
TEK 12-04D (ref. 5) includes basic material requirements, corrosion protection and placement tolerances for reinforcement used in concrete masonry construction. In addition, prestressing steel is discussed in Post-Tensioned Concrete Masonry Wall Construction, TEK 03-14 (ref. 6).
SPLICES AND DEVELOPMENT LENGTH
Minimum development lengths are necessary to adequately transfer stresses between reinforcement and the grout or mortar in which it is embedded. Splicing of reinforcement serves a similar purpose: to adequately transfer stresses from one reinforcing bar to another.
Reinforcement can be developed by embedment length, hook, or mechanical anchoring device. The development of the reinforcing bars relies on mechanical interlock of the bar deformations, hook, and/or anchor along with sufficient masonry cover to prevent splitting of the masonry. Reinforcing bars may be spliced by lapping the reinforcement, by proprietary mechanical splices or by welding.
The required length of lap or development is determined according to the design procedure used (allowable stress design or strength design). In addition, these detailing requirements have been frequently revised in recent years. As a result, the minimum lap and development lengths can vary considerably from one code to the next as well as from one design method to another.
The following sections present the requirements for both the 2009 IBC and 2012 IBC for both allowable stress and strength design.
2009 IBC SPLICE & DEVELOPMENT REQUIREMENTS
2009 IBC Allowable Stress Design
Development Length & Lap Splicing
While the 2008 MSJC includes an equation to determine development and lap splice lengths, the 2009 IBC modifies the MSJC lap splice length. In accordance with the 2009 IBC, the minimum required lap length for spliced reinforcing bars is determined using Equation 1 (see Table 1).
Further, in regions of flexure where the design tensile stresses in the reinforcement, fs, exceed 80% of the allowable steel tensile stress, Fs, the IBC requires that the required length of lap determined by Equation 1 must be increased by 50%. Alternatively, equivalent means of stress transfer to accomplish the same 50% increase is permitted. Where epoxy coated bars are used, lap length is also required to be increased by 50% but does not apply to the 12 in. (305 mm) minimum.
Development length requirements for allowable stress design are determined in accordance with Equation 3 except that there is no maximum length limit of 72db.
When noncontact lap splices are used, the bars must be spaced no farther apart than one-fifth the required length of lap nor more than 8 in. (203 mm).
When using the allowable stress design method, development of wires in tension is determined using Equation 2 (see Table 2). The development length of epoxy-coated wires is increased 50% above the value determined using Equation 2 but does not apply to the 6 in. (152 mm) minimum.
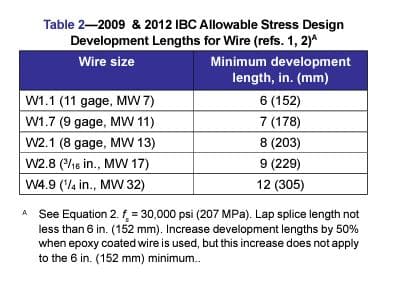
A See Equation 2. fs = 30,000 psi (207 MPa). Lap splice length not less than 6 in. (152 mm). Increase development lengths by 50% when epoxy coated wire is used, but this increase does not apply to the 6 in. (152 mm) minimum..
Alternatives to Lap Splicing
Reinforcing bars can also be spliced by welding, mechanical splicing and in some cases end-bearing splicing. Reinforcing bars larger than No. 9 (M#29) are required to be spliced using mechanical connectors.
Welded splices require the bars to be butted or shortly lapped and welded to develop in tension at least 125% of the specified yield strength of the bar. All welding is required to conform to AWS D1.4 (ref. 7), and steel for welded splices must conform to ASTM A706 (ref. 8). In practice, however, welding tends to be an expensive splicing option.
Mechanical splicing of reinforcement typically employs proprietary couplers specifically designed for this application. Mechanical splices are required to have the bars connected to develop in tension or compression, as required, at least 125% of the specified yield strength of the bar.
Reinforcing bars can also be spliced using end-bearing splices, but only in members containing closed ties, closed stirrups or spirals for bars subject to compression only. End-bearing splices rely on the transmission of compressive stress by bearing of square-cut ends held in concentric contact by a suitable device. The bar ends are required to terminate in flat surfaces within 11/2 degrees of a right angle to the axis of the bars and be fitted within 3 degrees of full bearing after assembly.
2009 IBC Strength Design
Development Length & Lap Splice Length
For development and lap splice length requirements, the 2009 IBC references the 2008 MSJC (see Equation 3 and Table 3), but adds a maximum length limit of 72db.
For Equation 3, the reinforcement size factor, g, is taken equal to 1.0 for No. 3 through No. 5 (M#10–M#16) reinforcing bars; 1.3 for No. 6 and No. 7 (M#19, M#22) bars; and 1.5 for No. 8 and No. 9 (M#25, M#29) bars. When epoxy coated bars are used, the development length determined by Equation 3 is required to be increased by 50%.
Bars spliced by noncontact lap splices must be spaced no farther apart than one-fifth the required length of lap and no more than 8 in. (203 mm).
Alternatives to Lap Splicing
Mechanical splices are required to have the bars connected to develop at least 125% of the specified yield strength of the bar in tension or compression, as required.
The IBC further stipulates that mechanical splices be classified as Type 1 or 2 according to Section 21.2.6.1 of ACI 318, Building Code Requirements for Structural Concrete and Commentary (ref. 10). Type 1 splices may not be used within the plastic hinge zone nor within a beam-column joint of intermediate or special reinforced masonry shear walls or special moment frames. Type 2 are permitted at any location.
A Type 2 splice is defined as a full mechanical splice that develops in tension or compression, as required, at least 1.25fy of the bar. This requirement is intended to avoid a splice failure when the reinforcement is subjected to expected stress levels in yielding regions. Type 1 splices are not required to satisfy the more stringent requirements for Type 2 splices, and so their use is limited as noted above.
Welded splices must have the bars butted and welded to develop at least 125% of the bar’s specified yield strength in tension or compression, as required. Welded splices must use ASTM A706 (ref. 9) steel reinforcement. Welded splices are not permitted to be used in plastic hinge zones of intermediate or special reinforced walls nor in special moment frames of masonry.
2012 IBC SPLICE & DEVELOPMENT REQUIREMENTS
Regarding development and splice lengths, two significant changes were incorporated into the 2011 MSJC, which are included by reference in the 2012 IBC:
- in the 2011 MSJC, the allowable tensile stress, Fs, of Grade 60 steel when using allowable stress design was increased from 24,000 psi (166 MPa) to 32,000 psi (221 MPa), and
- the 2011 MSJC includes new provisions for confinement reinforcement, for both allowable stress and strength design methods.
2012 IBC Allowable Stress Design
Equation 1 is still applicable for use in the 2012 IBC but with the increase in F the splice lengths of fully stressed bars will increase by 33%. Significant reductions of splice lengths in low stress areas are achieved, however. The minimums of 12 in. (305 mm) or 40db whichever is greater still apply as well.
The 2012 IBC allows the MSJC development length equation (Equation 3) to be used as an alternate to the IBC equation (Equation 1). When using Equation 3 under the 2012 IBC, however, the value of K is defined as the least of the masonry cover, 9db (vs. 5db in the 2009 IBC) and the clear spacing between adjacent reinforcement.
Tabulated values are presented in Tables 4a through 4d. Note, however, that there is no maximum length limit of 72db for allowable stress design.
Tables 4a and 4b present minimum lap splice lengths for reinforcement placed in the center of the wall, for f’m = 1,500 and 2,000 psi (10.3 and 13.7 MPa), respectively.
Tables 4c and 4d present minimum lap splice lengths for reinforcement offset in the wall, for f’m = 1,500 and 2,000 psi (10.3 and 13.7 MPa), respectively.
Other requirements for lap, mechanical, welded and end-bearing splices are identical to those under the 2009 IBC, with the exception of the new provisions for confinement reinforcement, presented below.
2012 IBC Strength Design
Requirements for development length as well as lap, mechanical and welded splices are identical to those for allowable stress design, and are presented in Tables 4a through 4d.
2012 IBC Lap Splices With Confinement Reinforcement
The 2012 IBC, by reference to the 2011 MSJC, includes new lap splice criteria where confinement reinforcement is placed. The criteria are the same for both allowable stress design and strength design.
The confinement reinforcement criteria allow a reduced lap splice length when reinforcement is provided transverse to lapped bars. Research has found that the transverse, or confinement, reinforcement increases the lap performance significantly, as long as there is at least one No. 3 (M#10) or larger transverse bar placed within the last 8 in. (203 mm) of each end of the lap (see Figure 1). Because of this effect, calculated lap splice lengths are permitted to be reduced by a confinement factor, ξ, determined using Equation 4:
where
db is the bar diameter of the vertical reinforcement
The reduced lap splice length is not permitted to be less than 36db. The clear space between the transverse bars and the lapped bars may not exceed 1.5 in. (38 mm), and the transverse bars must be fully developed in grouted masonry at the point where they cross the lapped reinforcement (see Figure 1). These provisions are included in Tables 4a through 4d
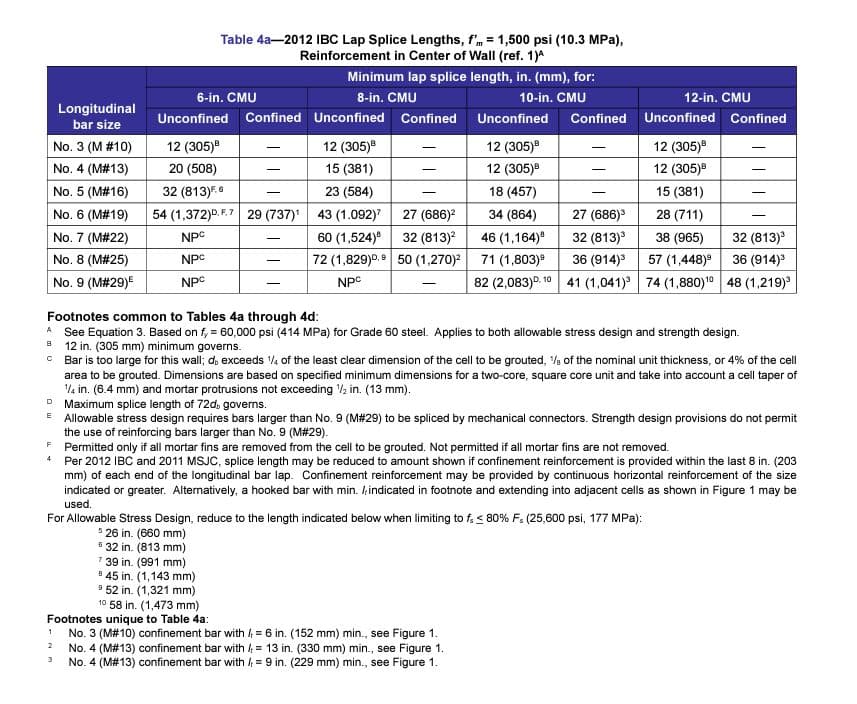
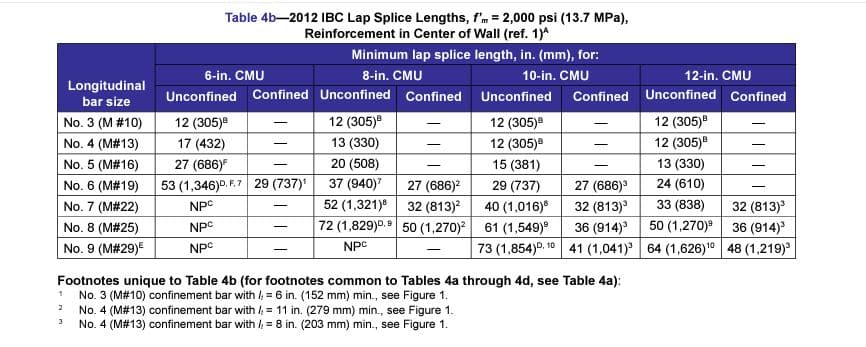
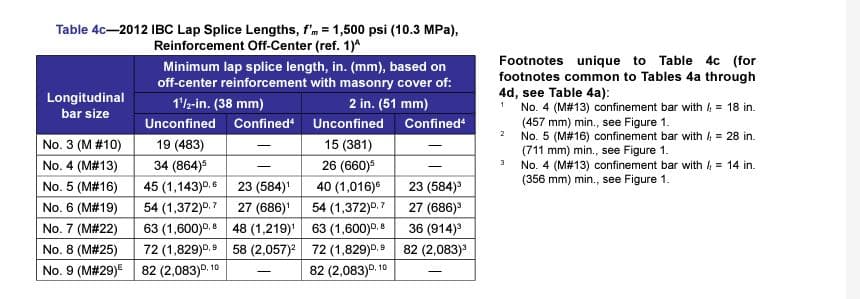
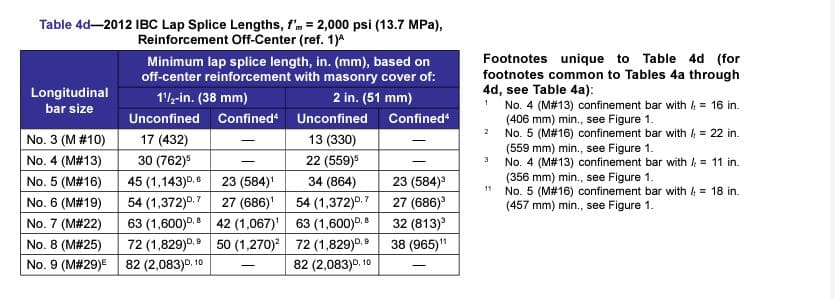
STANDARD HOOKS
Figure 2 illustrates the requirements for standard hooks, when reinforcing bars are anchored by hooks or by a combination of hooks and development length. These requirements apply to both the 2009 and 2012 IBC, for both allowable stress and strength design. Table 5 lists minimum dimensions and equivalent embedment lengths for standard hooks of various sizes. A combination of hook and development length must be used when the equivalent embedment length of the hook, le, is less than the required minimum development length, ld. In this case, development length equal to (ld – le) must be provided in addition to the hook. This additional development length is measured from the start of the hook (point of tangency with the main portion of the bar).
JOINT REINFORCEMENT SPLICES
Joint reinforcement must have a minimum splice length of 6 in. (152 mm) to transfer shrinkage stresses. Slippage of the deformed side wires is resisted by surface bond as well as by mechanical anchorage of the embedded portions of the cross wires.
NOTATIONS:
Asc = area of the transverse bars at each end of the lap splice, in.² (mm²)
Di = min. inside diameter of bend for standard hooks, in. (mm)
db = nominal diameter of reinforcement, in. (mm)
K = the least of the masonry cover, 9db for the 2012 IBC (5db for the 2009 IBC) and the clear spacing between adjacent reinforcement, in. (mm)
Fs = allowable tensile stress in reinforcement, psi (MPa)
f’m = specified compressive strength of masonry, psi (MPa)
fs = calculated tensile or compressive stress in steel, psi (MPa)
fy = specified yield strength of steel, psi (MPa)
ld = embedment length or lap splice length of straight reinforcement, in. (mm)
le = equivalent embedment length provided by standard hooks measured from the start of the hook (point of tangency), in. (mm)
lt = length of bar extension of hooked confinement reinforcement, in. (mm)
γ = reinforcement size factor
ξ = lap splice confinement reinforcement factor
REFERENCES
- International Building Code 2012. International Code Council, 2012.
- International Building Code 2009. International Code Council, 2009.
- Building Code Requirements for Masonry Structures, TMS 402-11 /ACI 530-11/ASCE 5-11. Reported by the Masonry Standards Joint Committee, 2011.
- Building Code Requirements for Masonry Structures, TMS 402-08 /ACI 530-08/ASCE 5-08. Reported by the Masonry Standards Joint Committee, 2008.
- Steel Reinforcement for Concrete Masonry, TEK 12-04D. Concrete Masonry & Hardscapes Association, 2007.
- Post-Tensioned Concrete Masonry Wall Construction, TEK 03-14. Concrete Masonry & Hardscapes Association, 2002.
- Structural Welding Code—Reinforcing Steel, AWS D 1.4-05. American Welding Society, 2005.
- Standard Specification for Low-Alloy Steel Deformed and Plain Bars for Concrete Reinforcement, ASTM A706/A706M-09b. ASTM International, Inc., 2009.
- Building Code Requirements for Structural Concrete and Commentary, ACI 318-11. American Concrete Institute, 2011.
TEK 12-06A, Revised 2013. CMHA and the companies disseminating this technical information disclaim any and all responsibility and liability for the accuracy and the application of the information contained in this publication.