INTRODUCTION
While mortar represents only a small proportion of the total wall area in concrete masonry construction (approximately 7 percent), its influence on the performance of a wall is significant. Mortar serves many important functions: it bonds units together into an integral structural assembly, seals joints against penetration by air and moisture, accommodates small movements within a wall, accommodates slight differences between unit sizes, and bonds to joint reinforcement, ties and anchors so that all elements perform as an assembly.
MORTAR MATERIALS
The American Society for Testing and Materials (ASTM) maintains national standards for mortars and materials commonly used in mortars, as follows:
Portland cement (ASTM C 150, ref. 4d) is a hydraulic cement (sets and hardens by chemical reaction with water) and is one of the main constituents of mortar. Types I (normal), II (moderate sulfate resistance), and III (high early strength) are permitted according to ASTM C 270 (ref. 4f). Air-entrained portland cements (IA, IIA, and IIIA) may be used as alternatives to each of these types.
Masonry cement (ASTM C 91, ref. 4b) is a hydraulic cement consisting of a mixture of portland cement or blended hydraulic cement and plasticizing materials (such as limestone, hydrated or hydraulic lime) together with other materials introduced to influence such properties as setting time, workability, water retention, and durability. Masonry cements are classified as Type M, Type S, or Type N according to ASTM C 270. In addition, Type N masonry cement can be combined with portland cement or blended hydraulic cement to produce Type S or M mortars.
Mortar cement (ASTM C 1329, ref. 4j) is a hydraulic cement similar to masonry cement, with the added requirement of a minimum bond strength requirement.
Blended hydraulic cements (ASTM C 595, ref. 4g) consist of standard portland cement or air-entrained portland cement (denoted by -A) combined through blending with such materials as blast furnace slag (S), or pozzolan (P & PM) which is usually fly ash. Types IS, IS-A, IP, IP-A, I(PM), or I(PM)-A blended cements may be used as alternatives to portland cement to produce ASTM C 270 compliant mortars. Types S or SA (slag cement) may also be used in mortars meeting the property specification requirements of ASTM C 270 (Table 2 of this TEK).
Quicklime (ASTM C 5, ref. 4a) is calcined (burneddecarbonated) limestone, the major constituents of which are calcium oxide (CaO) and magnesium oxide (MgO). Quicklime must be slaked (combined chemically with water) prior to use. The resultant lime putty must be stored and allowed to hydrate for at least 24 hours before use. Consequently, quicklime is rarely used in mortar.
Hydrated lime (ASTM C 207, ref. 4e) is a dry powder obtained by treating quicklime with enough water to satisfy its chemical affinity for water. ASTM C 207 designates Type N (normal), Type S (special), and air-entraining Type NA and Type SA hydrated limes. Slaking of hydrated lime is not required, thus hydrated lime is immediately usable and much more convenient than quicklime. ASTM C 207 limits the amount of unhydrated oxides in Type S or Type SA hydrated limes, assuring the soundness of mortar made using these limes. Types N or NA lime are not typically used in mortar; however, they are permitted if shown by test or performance record to not be detrimental to the soundness of the mortar. Air-entrained limes are only permitted in mortars containing nonair-entrained cement.
Aggregates (ASTM C 144, ref. 4c) for mortar consist of either natural or manufactured sand. Manufactured sand is the product obtained by crushing stone, gravel, or air cooled blast furnace slag. It is characterized by sharp, angular shaped particles. Gradation limits are established in ASTM C 144 for both natural and manufactured sands. Aggregates which fail these gradation limits may be used, as long as the resulting mortar complies with the property specification requirements of ASTM C 270, as shown in Table 2.
Water for masonry mortar (ASTM C 270, ref. 4f) must be clean and free of deleterious amounts of acids, alkalis, or organic materials. Potability of water is not in itself a consideration, but the water obtained from drinking supply sources is considered suitable for use.
Admixtures (also sometimes called modifiers or additives) for masonry mortars (ASTM C 1384, ref. 4k) are available for various purposes. Admixtures are functionally classified as bond enhancers, workability enhancers, set accelerators, set retarders, and water repellents. Since chlo-rides accelerate the corrosion of steel reinforcement and accessories ASTM C 1384 stipulates that admixtures add not more than 65 ppm (0.0065%) water-soluble chloride or 90 ppm (0.0090%) acidsoluble chloride by weight of portland cement. Similarly, the Specifications for Masonry Structures (ref. 3) limits admixtures to no more than 0.2% chloride ions. The document also limits pigments for coloring to no more than 1 to 10% by weight of cement depending upon the pigment type.
Effect of Materials on Mortar
With the diversity of materials available, masonry mortars can be formulated to produce the desired properties for most specific job requirements. Each of the individual ingredients (cement, lime, sand, water, and any modifiers present) contributes to the performance of the mortar. Portland cement provides strength and durability. Lime imparts workability, water retention, as well as some limited cementitious and autogenous healing properties. Sand acts as a filler and provides body to the mortar while helping to reduce shrinkage and control cracking. Water acts as a mixing agent, a lubricant, and is also needed for hydration of the portland cement.
The various material options alter the characteristics of the mortar in a predictable manner. Changes in cement type promote slight changes in setting characteristics, workability, color, and strength development. Use of air-entrained cement or lime generally results in decreased water demand, improved workability, increased freeze thaw resistance, and decreased bond strength. Masonry cements, used singly or in combination with portland cement, provide mortars with excellent workability and freeze-thaw durability; however, bond strengths may be reduced. Consequently, design allowable flexural tension values vary based on mortar type and cementitious materials or lime used for unreinforced masonry (ref. 1).
Changes in sand type and gradation affect mortar properties. Natural sand gives improved workability at a lower water demand because of the spherical particle shape, while manufactured sands require additional water due to their angular shape. In general, well graded aggregates reduce segregation in a plastic mortar, which in turn inhibits bleeding and improves workability. Sands deficient in fines generally produce harsh mortars, while sands with excessive fines typically result in mortars with lower compressive strengths.
TYPES OF MORTAR
Building codes generally specify mortar types as referenced in ASTM C 270, Standard Specification for Mortar for Unit Masonry (ref. 4f). Four mortar types, M, S, N and O are included in this standard. However, Types M, S, and N are typically required by building codes. Building codes also may restrict the use of some mortars for particular applications. For example, empirical design of foundation walls requires Type M or S mortar and glass unit masonry requires Type N or S mortar (ref. 1). In seismic design categories , D, E, and F portland cement/ lime or mortar cement mortar Types S or M are required (ref. 1).
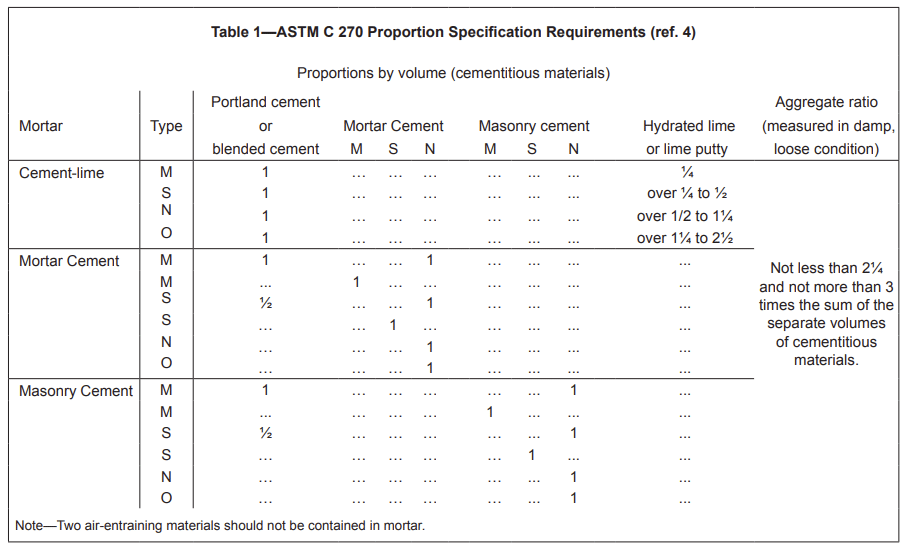
PROPORTIONING MORTAR
All mortar types are governed by either of the two specifications contained in ASTM C 270: the proportion specification or the property specification. Only one of the specifications should be called for in the project documents, not both. The proportion specification (Table 1) prescribes the parts by volume of each ingredient required to provide a specific mortar type. A combination of portland cement and lime may be used as the cementing agent in each type of mortar. Also, masonry cements (ref. 4b) or mortar cements (ref. 4j) are available that meet the requirements of M, S, and N mortars with or without further addition of cement.
As an alternative, approved materials may be mixed in controlled percentages as long as the resultant mortar meets the physical requirements designated in ASTM C 270, as shown in Table 2. The aggregate ratio noted in Table 2 must be followed. Conformance to the property specification of ASTM C 270 is established by testing laboratory prepared mortar during a pre-construction evaluation of the mortar proposed for the project. The laboratory then establishes proportions for mortar, based on successful tests. These proportions are then followed when preparing field mortar.
MASONRY MORTAR PROPERTIES
Many properties of mortar are not precisely definable in quantitative terminology because of a lack of definitive standards by which to measure them. For example, mortars can be rated on the basis of obtaining visually satisfactory mortar joints.
Depending on the particular circumstances for a given project, the criteria for mortar selection are based on design considerations, mortar properties in the plastic state or mortar properties in a hardened state. Consideration of each is necessary to achieve a desired result.
Properties of Plastic Mortar
Workability is the property of mortar characterized by the smooth plastic consistency which makes it easy to spread. This is the property of most importance to the mason. A workable mortar spreads easily under the trowel; adheres to vertical surfaces during unit handling, placement, and bedding; maintains alignment as other units are positioned; and provides a watertight, closed joint when tooled.
Once mix proportions have been established, the addition of water should be consistent with that required to improve mortar placement without sacrificing the ability to support the masonry unit. Adequate water content promotes intimate contact between the unit and mortar, which is essential for satisfactory bond. While water content has the greatest influence on the workability of a mortar, cementitious materials, aggregate gradation, and air-entrainment also contribute to a lesser degree.
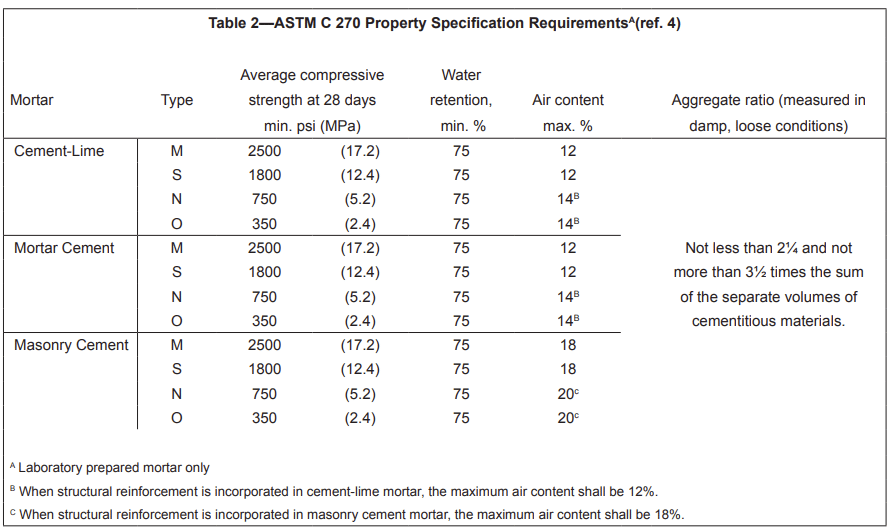
Water retention of mortar is a measure of the mortar’s ability to retain its plasticity when subjected to the atmosphere or the absorptive forces of a concrete masonry unit. Mortars with low water retention stiffen more quickly, making it difficult for the mason to bed and adjust the masonry unit during placement. Mortars with desired water retention characteristics allow the mason to lay a mortar bed two or three units ahead before placing subsequent units. Water retentivity is dependent on properties of the cementitious materials, sand gradation, and mortar proportions.
The time lapse between spreading a mortar bed and placing block should be kept to a minimum, because the workability will be reduced as water is absorbed into the block. If too much time elapses before a block is placed on a fresh mortar bed, units are less easily positioned and the bond will be reduced.
Evaporation of the mixing water from mortar may require retempering (mixing in additional water). This generally is not harmful as long as it is done prior to hydration of the mortar. To avoid the stiffening effects of hydration, mortar must be placed in final position within 21/2 hours after the original mixing (ref. 3) unless special set retarding admixtures are used.
Properties of Hardened Mortar
Properties of hardened mortar that affect the performance of the finished concrete masonry include bond, compressive strength, and durability. These properties are difficult to measure other than in laboratory or field specimens prepared under controlled conditions. However, ASTM C 1324, Standard Test Method for Examination and Analysis of Hardened Masonry Mortar, (ref. 4i) provides procedures for petrographic examination and chemical analysis for components of masonry mortar in the hardened state. A 0.35 oz. (10 g) sample is usually sufficient for both the petrographic and chemical analysis. When obtaining the sample, however, it is important to ensure that the sample is representative of the mortar in question, i.e. original mortar as opposed to pointing mortar or other mortars used on the project.
Bond is a term used to describe both the extent of contact between mortar and unit and the strength of adhesion. Bond is a function of several factors including mortar properties, unit surface characteristics, workmanship, and curing. Other factors being equal, bond strength will increase as the compressive strength of the mortar increases, although not in direct proportion. Bond may also be effectively increased through the use of properly designed mortars having water contents which provide good workability.
Compressive strength is perhaps the most commonly measured property of mortar but is perhaps the most misunderstood. Whenever compressive strength results are intended to be used to determine conformance of a mortar to the property specifications of ASTM C 270, compressive strength tests must be conducted in accordance with the laboratory procedures required by ASTM C 270. However, field mortar compressive testing is to be conducted in accordance with ASTM C 780, Standard Test Method for Preconstruction and Construction Evaluation of Mortars for Plain and Reinforced Unit Masonry, (ref. 4h) and is only to verify the consistency of materials and procedures, not to determine mortar strength (ref. 3). ASTM C 780 contains no requirement for minimum compressive strength of field mortar. The the mortar strength in the wall will be much higher than the field test because of the reduced water cement ratio due absorption of mix water into the masonry units and a greatly reduced shape factor in the mortar joint versus the mortar test cube. ASTM C 780 recognizes this and states that the strength should not be construed as being representative of the actual strength of the mortar.
Durability of mortar also is an important consideration for parapets or other walls with an extreme exposure to the weather. Oversanding or overtempering can decrease durability. High strength mortars and air entrained mortars provide increased durability. For more detailed discussion on field testing of mortar see TEK 18-05B, Masonry Mortar Testing (ref. 2).
REFERENCES
- Building Code Requirements for Masonry Structures, ACI 530-02/ASCE 5-02/TMS 402-02. Reported by the Masonry Standards Joint Committee, 2002.
- Masonry Mortar Testing, TEK 18-05B, Concrete Masonry & Hardscapes Association, 2014.
- Specifications for Masonry Structures, ACI 530.1-02/ASCE 6-02/TMS 602-02. Reported by the Masonry Standards Joint Committee, 2002.
- 2004 Annual Book of ASTM Standards, American Society for Testing and Materials:
4a. C 5-03, Standard Specification for Quicklime for Structural Purposes.
4b. C 91-03a, Standard Specification for Masonry Cement.
4c. C 144-03, Standard Specification for Aggregate for Masonry Mortar.
4d. C 150-04, Standard Specification for Portland Cement.
4e. C 207-04, Standard Specification for Hydrated Lime for Masonry Purposes.
4f. C 270-03b, Standard Specification for Mortar for Unit Masonry.
4g. C 595-03, Standard Specification for Blended Hydraulic Cements.
4h. C 780-02, Standard Test Method for Preconstruction and Construction Evaluation of Mortars for Plain and Reinforced Unit Masonry.
4i. C 1324-03, Standard Test Method for Examination and Analysis of Hardened Masonry Mortar.
4j. C 1329-04, Standard Specification for Mortar Cement.
4k. C 1384-03, Standard Specification for Admixtures for Masonry Mortars.