INTRODUCTION
To the new and prospective owner of a building, one of the most attractive features of constructing with concrete masonry is its low cost of maintenance. The characteristic wear and tear that all buildings are subjected to, however, necessitates periodic repair and restoration to preserve and maintain the original integrity and appearance of the structure. Preventive maintenance conserves the value, appearance and integrity of the building.
Since the useful life of a concrete masonry structure can be directly related to the quality of the maintenance, an established and rigorous maintenance program will greatly reduce the chances of major problems or costly repairs. This TEK focuses on typical maintenance issues facing owners of concrete masonry buildings.
DESIGN AND CONSTRUCTION CONSIDERATIONS
Design and construction methods greatly affect the required maintenance needs of a building. Accordingly, maintenance issues should be considered during the design and construction processes. Where possible, accepted industry practices should be followed to avoid cracking and spalling, preclude efflorescence, minimize staining and dirt buildup, and prevent the penetration of water into the structure. While design and construction issues are beyond the scope of this TEK, the reader is advised to refer to other industry guidelines during the design and construction of buildings to address these issues. In addition, several TEK that deal specifically with design and construction issues affecting maintenance of buildings are referred to herein for the benefit of the reader.
CRACK PREVENTION AND REPAIR
Once placed in a structure, concrete masonry units are subject to a variety of forces and stresses which, besides structural loads, include shrinkage stresses due to drying, temperature fluctuations, and carbonation (an irreversible reaction with carbon dioxide in the atmosphere). Although the net resulting shrinkage in a finished structure can vary considerably (for example, temperature movements can vary greatly with exposure and unit color, while drying shrinkage can be expected to be higher for units having a higher cement content), the combined effect of these shrinkage components could be sufficient to cause large tensile cracks in the masonry if proper precautions are not taken. Shrinkage cracking and crack control strategies are covered in more detail in CMU-TEC-009 23 (ref. 1).
The next leading cause of cracking in concrete masonry walls is differential settlement due to uneven support of the foundation. Due to the highly complicated and problematic nature of such cracks, the reader is encouraged to seek the aid of a qualified design professional for recommendation on corrective actions for differential settlement.
Any objectionable crack should be analyzed to determine the cause and any previous corrective measures taken to prevent or accommodate the movement before additional repairs are made. Otherwise cracks may simply form again. Since the necessary corrective action required in crack repair is highly dependent on the cause of the crack and whether the crack is stable (the crack has stopped getting wider), significant attention should be focused on these issues. A simple but fairly effective method of determining if a hairline crack is continuing to propagate or widen is to patch over a small length of the crack with gypsum plaster and monitor the patch regularly for several days. Additionally, a variety of gauges can also be used to routinely monitor crack widths. The benefit associated with implementing crack width and/or deflection measuring gages is that qualitative data is obtained which can be used to determine an appropriate crack repair method.
If it is determined that cracking is present due to the lack of, or inadequate spacing of control joints, it may be necessary to retrofit the structure with control joints. Installation of control joints in an existing structure is completed by first determining the location and spacing of required control joints by an approved method. Next, a vertical joint is saw-cut at the location of a head joint through the mortar and masonry units. The joint should extend completely through the wall and be approximately 3/8-inch (10 mm) wide, or one mortar joint wide. Finally, the newly cut joint should be cleaned, filled with a backer rod and caulked as recommended by the manufacturer. The sealant will prevent water, dirt, or insects from entering the structure. Before retrofitting any building with control joints, consult a qualified design professional.
If the cracking is not extensive, confined primarily to the mortar joints, and relatively stable in width, it can be readily repaired by conventional tuckpointing (also called repointing) methods as detailed in Figure 1. Unless the wall is to be parged or coated, efforts should be made to match the color and texture of the new joints to the old. If the identity of the original mortar materials is unknown, trial batches of different mix designs should be applied in test joints, tooled, and aged for a period of at least one week. Variations in the age of the mortar when the tooling is performed as well as the tooling pressure are suggested as well since both affect color and texture. The best match can then be selected. It should be noted that because of dirt deposits and stains, matching existing mortar color of old buildings may be difficult. Accordingly, cleaning of the masonry may be required prior to applying tuckpointing efforts.
Small cracks that do not pose a structural problem may be susceptible to water penetration due to wind driven rain. A variety of coatings are available that can effectively resist water penetration. Note however that cracks larger than 0.02 in. (0.5 mm) can not usually be sealed with clear water repellents.
A solution for larger, nonstructural cracks is the parging of the exposed surface. A parging material comprised of one part portland cement and 3 parts sand (by volume) passing a No. 30 sieve or a No. 50 sieve (depending on the size of the cracks) is applied to the surface in two layers. The first layer, commonly referred to as a scratch coat, is applied to the surface in approximately ¼-inch (6 mm) thickness. Once the scratch coat (so called since the surface is left rough to ensure good bond to the finish coat) is thumbprint hard, the finish coat also about ¼-inch (6 mm) thickness is applied. Once the finish coat has cured sufficiently so that nearly all the plastic shrinkage has occurred (thumbprint hard), the surface can be worked with a damp sponge to effectively seal the outer surface. More information on parging and portland cement coatings can be found in TEK 09-03A (ref 3). Large non-structural cracks that continue to move (wide shrinkage cracks, for example) can sometimes be filled with sealant which has more flexibility to undergo movement than mortar.
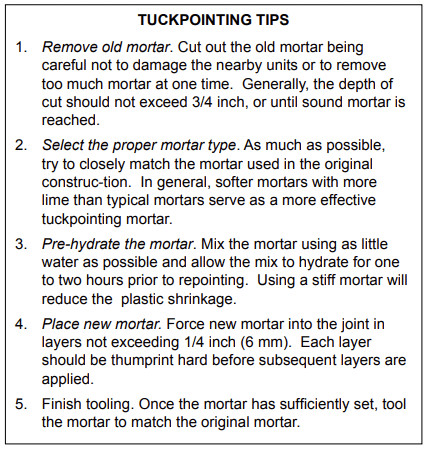
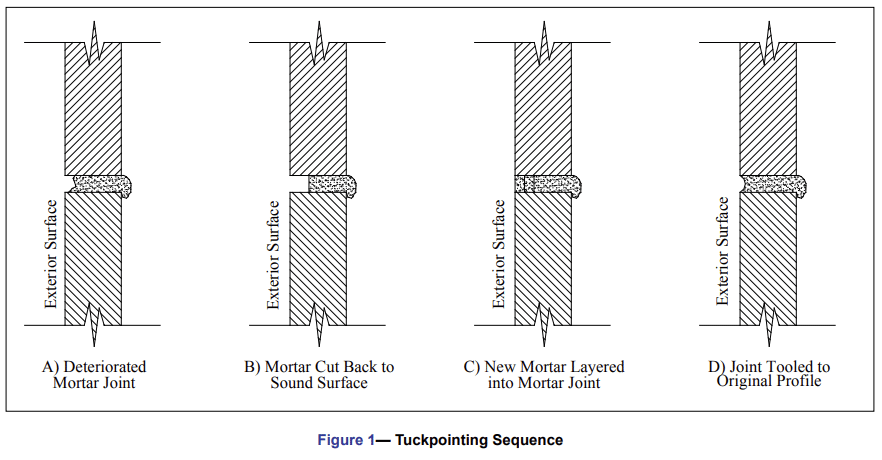
CLEANING
Periodic cleaning of buildings may be needed to remove dirt, stains, efflorescence, graffiti and mold. TEK 08-02A (ref. 4) provides information on removing a wide range of stains and TEK 08-03A (ref. 2) discusses control and removal of efflorescence. As a general recommendation for all cleaning efforts, care should be taken to use a cleaning method that is as non-aggressive as possible so as not to damage the masonry or surrounding materials. The cleaning agent manufacturer’s recommendations should be closely followed since some products can not only damage the building, but can also cause serious injuries to personnel.
Prior to starting cleaning efforts on routine stains such as rusting from nearby metals or efflorescence, the cause of the stain should be identified and remedied if possible so that further cleaning efforts are avoided. Cleaning procedures should be started in small inconspicuous areas to ensure the cleaning method is effective, non damaging, and providing the desired results. Once the effectiveness of the cleaning method is determined it can then be applied to the entire building.
WATER PENETRATION
Traditionally, concrete masonry units have required some form of coating to prevent rainwater from penetrating into the building. Today, integral water repellents can be added into the mixes used to make both concrete masonry units and mortar. The owner is advised however, to assume that the concrete masonry is somewhat porous, unless it is specifically known that the units and mortar contain integral water repellents. Accordingly, reapplication of clear surface applied water repellents, paints and other coatings is a prime maintenance item to ensure the building remains dry. See TEK 19-01 (ref. 5) for more information on water repellents.
Water penetration in a building, however, can stem from numerous other entry points, even if the wall is wet, and appears to be the leaking element. Roofs, parapet caps, flashing, doors, windows, control joints, penetrations for pipes and conduits and other building elements should be inspected routinely to ensure water penetration does not occur at these locations. Sealants around many of these elements should be monitored and replaced when needed.
To prevent water penetration through basement walls, ensure that the ground around the building slopes away from the building. Where the site does slope towards the building, a swale, or shallow trench, should be installed to direct runoff away from the basement. As discussed elsewhere in this TEK, trees, shrubs, and ground cover can shield the soil near a basement from severe rain, and reduce the amount of water absorbed by the soil. Note however, that trees and large shrubs should be kept at least 10 to 15 feet (3 to 4.6 m) away from basement walls so roots do not damage the walls.
To prevent heavy roof runoff near basements, gutters and downspouts are recommended. Downspouts should empty onto splash blocks that direct the water away from the basement. If present, sump pumps and French drains also must be maintained.
Sprinklers and water faucets should also be monitored to assure they are not spraying excessive amounts of water on walls. Crack repair, control joint maintenance and coating reapplication should also be reconsidered to ensure water tightness of the building.
COATINGS
Walls that have been covered with paint, water repellents, waterproofing or other coatings require periodic inspection of the condition of the coatings, and reapplication at some point will be necessary. Because of the wide range of products that can be used on concrete masonry walls, it is important to try to keep records of the coatings applied to the masonry. This will make the selection of appropriate reapplication materials much easier.
The proper selection and application of coatings will improve the performance and service life of the surface. For example, consider the wide range of paints commonly used. Styrenebutadiene latex or polyvinyl acetate latex paints are inexpensive, but are usually suitable for only for interior residential walls. Oilbased and alkyd paints are more expensive and slightly more difficult to apply, but generally are longer lasting. Acrylic latex paints are the most satisfactory for exteriors from the standpoint of length of life and ease of application. Portland cement paints are lower in cost but require more labor and a longer time to cure. They are however, very long-lived. These are the most common choices of paints for masonry walls, although others are useful for special applications.
When both sides of a wall are coated, the permeability of a coating or paint should always be lower on the side of the wall that is exposed to the higher vapor pressures. In warm moist regions, this means that the paint applied to the exterior of a wall should have a lower permeability to vapor than the paint applied to the inside of the same wall. Conversely, in cold dry climates, use a paint on the inside of the wall that is less permeable to water vapor than the paint on the inside of the wall. This will prevent water from passing through the coating or paint and becoming trapped within the wall. Exceptions to this rule include locker rooms, kitchens, enclosed swimming pools, or other sources of high-humidity where the interior almost always has the higher vapor pressure.
Walls should be clean before paint and other coatings are applied and should generally be dry. Some coatings however, such as some water-based water repellents and stucco, may require a damp surface. Manufacturer’s instructions should always be closely followed to ensure the preparation of the surface and application are appropriate so the coatings perform as intended.
On coarse textured exterior walls, it may be desirable to apply a fill coat prior to the first application of paint. Oil base paints and alkyds should not be applied to walls that are less than six months old unless they are first treated with a solution of three percent phosphoric acid and then one to two percent zinc chloride. Paints should not be thinned except in accordance with the manufacturer’s directions, and paints should be applied only when temperatures are within the recommended range.
Because the condition of clear water repellents is difficult to determine, scheduled reapplication is crucial to ensure the coatings shed rain water effectively. There are four general classifications of clear water repellents that are used on masonry walls: silane, siloxane, acrylic, and water based. Where possible, the same, or similar type coating should be used for the reapplication. In some areas, solvent based water repellents are no longer permitted to be used because of local regulations on volatile organic chemicals. Therefore, some products may not be available in all regions. Consult a local design professional or building official for clear coatings that are available locally. Additionally, TEK 19-01 (ref. 5) provides more information on these products.
IVY AND OTHER PLANT GROWTH
Plants in, around, and even on buildings add to the beauty of masonry walls and provide protection for the walls. They reduce temperature fluctuations by keeping the walls cooler in the summer. Trees, shrubs and ivy shield the walls from driving rain, thereby reducing the possibility of water penetration. Despite these and other benefits however, plant growth should be monitored to ensure the building is not damaged.
Roots of trees and shrubs can cause severe damage and sometimes even collapse of basement walls. Owners should accordingly avoid placing large, vigorous growing plants near basement walls. Generally trees and shrubs should be kept 10 to 15 feet (3 to 4.6 m) from basement walls, and smaller shrubs should be placed no closer than 2 to 3 feet (0.6 to .9 m) from the walls. Small plants such as flowers and ground cover can extend to the wall, and assist in preventing erosion and excessive water penetration. Large overhanging trees should also be trimmed back periodically since leaves, twigs and branches can clog drains potentially leading to serious water penetration problems.
Permitting ivy to grow on walls should also be considered carefully. While it can provide benefits, ivy shoots can enter voids in the mortar joints and damage the mortar. Over time the ivy shoots can break up and dislodge mortar and masonry units. Ivy also holds moisture that can contribute to moisture damage. Additionally, ivy is a home for insects, birds, and other animals that can enter the building.
The decision to allow ivy to grow is a balance between beauty and the durability of concrete masonry walls. Even well constructed concrete masonry walls may have their estimated service life shortened. Aesthetic and ecological value of ivy should be considered along the expectation of service life.
CONTROL JOINTS
Control joints are used to relieve horizontal tensile stresses due to shrinkage by reducing restraint and permitting movement to take place. They are placed in concrete masonry walls to prevent cracking. Vertical separations are built into the wall at locations where stress concentrations may occur.
To resist moisture penetration, control joints are filled with backer rods and sealant, or with other approved materials. These materials should be inspected periodically for any damage or foreign debris, and to ensure the sealant has not torn or debonded from the masonry wall. Damaged sealant should be removed and new sealant should be installed. Prior to filling the joint, the edges of the masonry in the joint may need to be cleaned and primed to ensure the sealant will adhere to the masonry.
UNIT DEGRADATION
Spalling and popouts in concrete masonry units are uncommon. However, under certain conditions they can occur, and units can also be damaged from large impacts. Such units should be inspected and repaired in a timely manner. Where the cause of the degradation is not apparent, consideration as to the cause of the defect should be given along with consideration of whether future degradation may occur. Obviously, if future degradation is expected, the cause should be remedied prior to making repairs. Causes of continuing damage include water penetration that may lead to freeze-thaw damage, excessive salts and chemicals from weed killers and fertilizers, and ivy and other plants.
Damaged or cracked units can be patched with mortar materials, depending on aesthetic concerns. Replacing a damaged unit can be accomplished by carefully chiseling or sawing out the broken unit and all the surrounding mortar. Once all the old mortar, dust, and debris are removed, a replacement unit can be installed by buttering the edges of the unit with mortar and placing it in the opening in the wall. The mortar should be tooled to match the original profile once the mortar becomes thumbprint hard. If the unit that requires replacement contains vertical reinforcement or is grouted, only the face shell of the unit may be able to be replaced. In this case it is advisable to spread mortar on the back of the face shell as well to provide bond between the grout as well as to the surrounding masonry units.
THE ROLE OF THE OWNER
Because masonry has earned the reputation as a longlasting and durable material, owners may not factor into their annual budget funds needed for maintenance of masonry walls. While these walls typically need much less attention than other materials, the cost invested by the owner in regular masonry maintenance throughout the life of the structure will pay great dividends in the long run.
OWNER’S MANUAL
A successful maintenance program begins with a good owner’s manual. This manual should identify and describe all of the materials and equipment installed in the building and should outline the maintenance needed for each of these items. The manual also should include updated as-built project drawings and details rather than initial design and bid specifications. The material and equipment descriptions should include the product name, the manufacturer, the expected life cycle, associated material safety issues, and where to turn for more information.
The owner’s representative, typically the architect, should assume responsibility of compiling the owner’s manual. To insure completion of the manual, it should be included as part of the scope of work when the job is put out to bid. Records of inspections and corrective measures conducted should be assembled and kept up by the building maintenance personnel as a supplement to the manual.
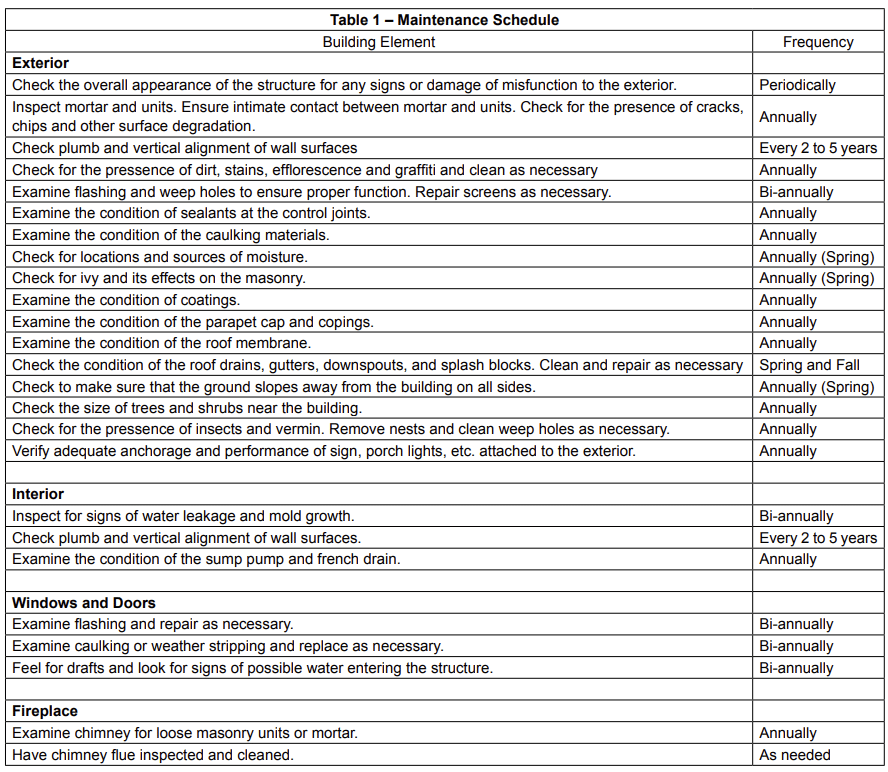
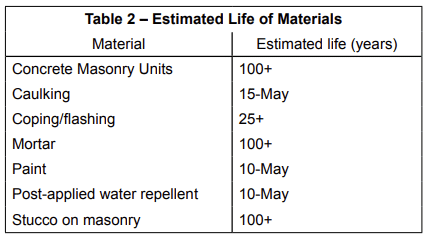
Inspection
The owner’s manual should stress the need of periodic condition assessments. Timely identification of problems or even potential problems can greatly reduce the costs associated with corrective measures. While the majority of the inspection can be done by visual assessment of the exterior surface of the masonry, the condition of the interior of the structure can also be useful to determine the performance of the masonry in areas such as water and air penetration resistance.
Building maintenance personnel or other owner’s representatives should perform these inspections at least annually. Masonry or building specialists should be consulted for a more thorough inspection every five years. Table 1 is a list of items made to schedule regular replacement of materials that are known to have a typical effective life that is less than that of the masonry. Examples of these materials and their common performance duration are listed in Table 2.
REFERENCES
- Crack Control Strategies for Concrete Masonry Construction, CMU-TEC-009-23, Concrete Masonry & Hardscapes Association, 2023.
- Control and Removal of Efflorescence, TEK 08-03A, Concrete Masonry & Hardscapes Association, 2003. Plaster and Stucco for Concrete Masonry, TEK 09-03A, Concrete Masonry & Hardscapes Association, 2002.
- Removal of Stains from Concrete Masonry, TEK 08-02A, Concrete Masonry & Hardscapes Association, 2005.
- Water Repellents for Concrete Masonry Walls, TEK 19-01, Concrete Masonry & Hardscapes Association, 2006.