INTRODUCTION
Estimating the quantity or volume of materials used in a typical masonry project can range from the relatively simple task associated with an unreinforced single wythe garden wall, to the comparatively difficult undertaking of a partially grouted multi-wythe wall coliseum constructed of varying unit sizes, shapes, and configurations.
Large projects, due to their complexity in layout and detailing, often require detailed computer estimating programs or an intimate knowledge of the project to achieve a reasonable estimate of the materials required for construction. However, for smaller projects, or as a general means of obtaining ballpark estimates, the rule of thumb methods described in this TEK provide a practical means of determining the quantity of materials required for a specific masonry construction project.
It should be stressed that the information for estimating materials quantities in this section should be used with caution and checked against rational judgment. Design issues such as non-modular layouts or numerous returns and corners can significantly increase the number of units and the volume of mortar or grout required. Often, material estimating is best left to an experienced professional who has developed a second hand disposition for estimating masonry material requirements.
ESTIMATING CONCRETE MASONRY UNITS
Probably the most straightforward material to estimate for most masonry construction projects is the units themselves. The most direct means of determining the number of concrete masonry units needed for any project is to simply determine the total square footage of each wall and divide by the surface area provided by a single unit specified for the project.
For conventional units having nominal heights of 8 in. (203 mm) and nominal lengths of 16 in. (406 mm), the exposed surface area of a single unit in the wall is 8/9 ft2 (0.083 m 2). Including a 5 percent allowance for waste and breakage, this translates to 119 units per 100 ft2 (9.29 m2) of wall area. (See Table 1 for these and other values.) Because this method of determining the necessary number of concrete masonry units for a given project is independent of the unit width, it can be applied to estimating the number of units required regardless of their width.
When using this estimating method, the area of windows, doors and other wall openings needs to be subtracted from the total wall area to yield the net masonry surface. Similarly, if varying unit configurations, such as pilaster units, corner units or bond beam units are to be incorporated into the project, the number of units used in these applications need to be calculated separately and subtracted from the total number of units required.
ESTIMATING MORTAR MATERIALS
Next to grout, mortar is probably the most commonly misestimated masonry construction material. Variables such as site batching versus pre-bagged mortar, mortar proportions, construction conditions, unit tolerances and work stoppages, combined with numerous other variables can lead to large deviations in the quantity of mortar required for comparable jobs.
As such, masons have developed general rules of thumb for estimating the quantity of mortar required to lay concrete masonry units. These general guidelines are as follows for various mortar types. Note that the following estimates assume the concrete masonry units are laid with face shell mortar bedding; hence, the estimates are independent of the concrete masonry unit width.
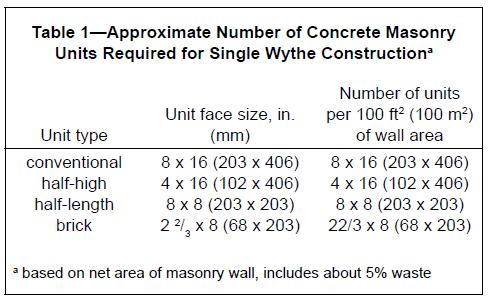
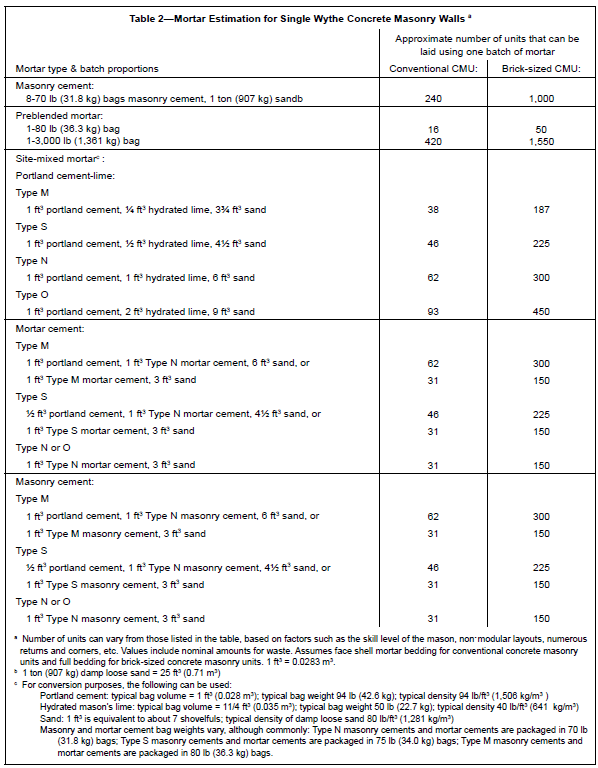
Masonry cement mortar
Masonry cement is typically available in bag weights of 70, 75 or 80 lb (31.8, 34.0 and 36.3 kg), although other weights may be available as well. One 70 lb (31.8 kg) bag of masonry cement will generally lay approximately 30 hollow units if face shell bedding is used. For common batching proportions, 1 ton (2,000 lb, 907 kg) of masonry sand is required for every 8 bags of masonry cement. If more than 3 tons (2,721 kg) of sand is used, add 1/2 ton (454 kg) to account for waste. For smaller sand amounts, simply round up to account for waste. This equates to about 240 concrete masonry units per ton of sand.
Preblended mortar
Preblended mortar mixes may contain portland cement and lime, masonry cement or mortar cement, and will always include dried masonry sand. Packaged dry, the mortars typically are available in 60 to 80 lb (27.2 to 36.3 kg) bags or in bulk volumes of 2,000 and 3,000 lb (907 and 1,361 kg).
Portland cement lime mortar
One 94 lb (42.6 kg) bag of portland cement, mixed in proportion with sand and lime to yield a lean Type S or rich Type N mortar, will lay approximately 62 hollow units if face shell bedding is used. This assumes a proportion of one 94 lb (42.6 kg) bag of portland cement to approximately one-half of a 50 lb (22.7 kg) bag hydrated lime to 4 1/4 ft3 (0.12 m3) of sand. For ease of measuring in the field, sand volumes are often correlated to an equivalent number of shovels using a cubic foot (0.03 m3) box, as shown in Figure 1.
ESTIMATING GROUT
The quantity of grout required on a specific job can vary greatly depending upon the specific circumstances of the project. The properties and configuration of the units used in construction can have a huge impact alone. For example, units of low density concrete tend to absorb more water from the mix than comparable units of higher density. Further, the method of delivering grout to a masonry wall (pumping versus bucketing) can introduce different amounts of waste. Although the absolute volume of grout waste seen on a large project may be larger than a comparable small project, smaller projects may experience a larger percentage of grout waste.
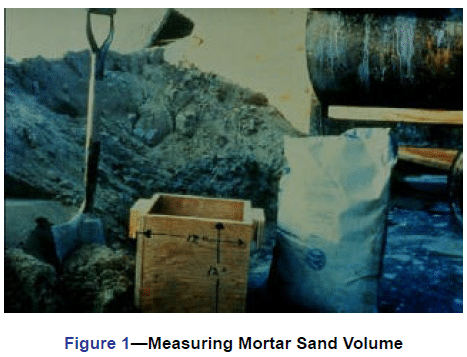
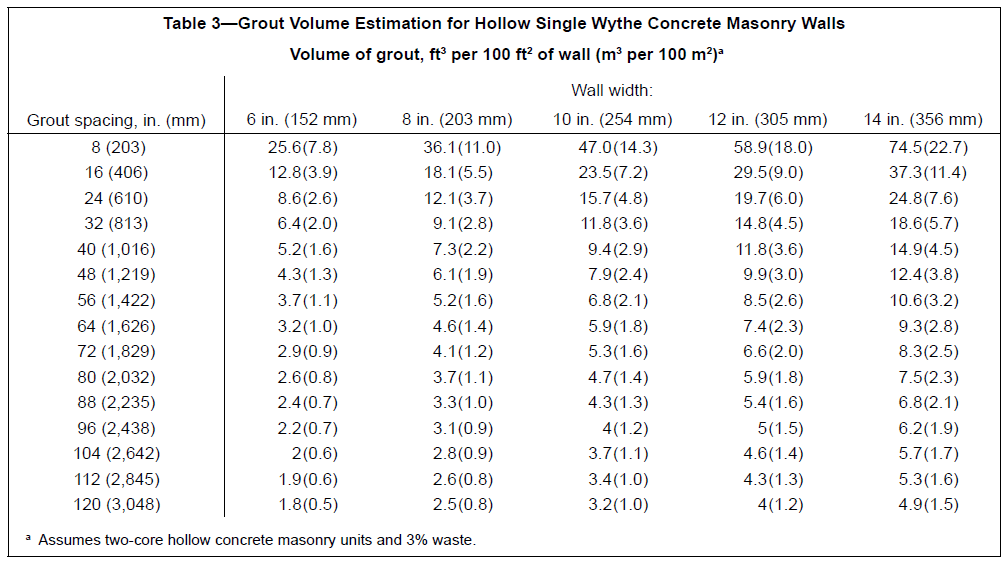
Table 3 provides guidance for the required volume of grout necessary to fill the vertical cells of walls of varying thickness. Additional grout may be necessary for horizontally grouting discrete courses of masonry. Note that walls constructed of 4-in. (102-mm) masonry units are not included in Table 3. Due to the small cell size and difficulty inadequately placing and consolidating the grout, it is not recommended to grout conventional 4-in. (102-mm) units.
Tables 4 and 5 contain estimated yields for bagged preblended grouts for vertical and horizontal grouting, respectively.
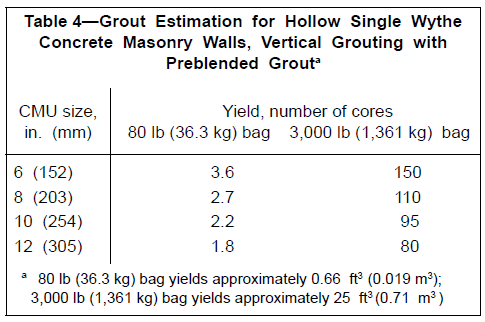
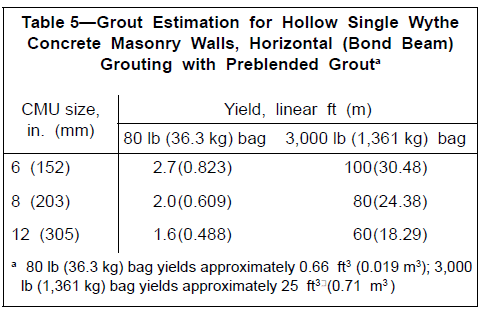
REFERENCES
- Kreh, D. Building With Masonry, Brick, Block and Concrete. The Taunton Press, 1998.
- Annotated Design and Construction Details for Concrete Masonry, CMU-MAN-001-03, Concrete Masonry & Hardscapes Association, 2003.