INTRODUCTION
For masonry construction, productivity is typically thought of as the number of concrete masonry units placed per unit of time. This production rate is influenced by many factors, some of which can be controlled by the mason and others which are beyond the mason’s control.
PRODUCTIVITY RATES
Ideally, concrete masonry productivity rates should be compiled by masonry estimators, based on records of completed jobs. Published productivity rates, such as those shown in Figure 1 and Table 1, should be used as guidelines only.
The following sections discuss some of the various factors that can impact masonry productivity. In addition to these, productivity rates can vary with unit size and concrete density, mortar workability, masonry bond pattern, number and type of wall openings, amount of reinforcement and wall size.
As illustrated in Figure 1, concrete ma-primarily in running bond, other bond patterns often require more time to lay. For example, stack bond has been estimated to decrease productivity by about 8% over comparable running bond productivity rates (ref. 4).
Bond pattern can also affect productivity. Because masonry crews are accustomed to laying concrete masonry primarily in running bond, other bond patterns often require more time to lay. For example, stack bond has been estimated to decrease productivity by about 8% over comparable running bond productivity rates (ref. 4).
IMPACT OF QUALITY ON PRODUCTIVITY
The overall quality of the project can influence the masonry productivity. Quality construction includes:
- pre-bid and pre-construction conferences,
- proper design,
- attention to planning and layout,
- quality materials,
- adequate jobsite and
- proper installation.
A project with these ingredients will also be conducive to a very productive jobsite.
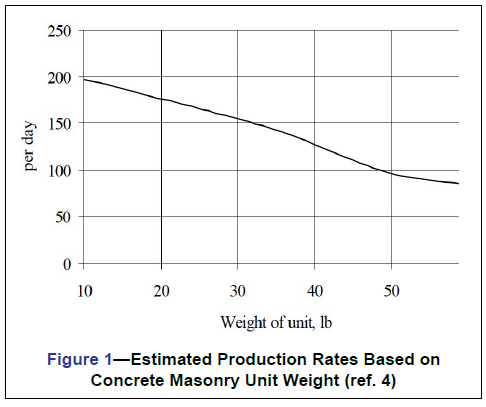
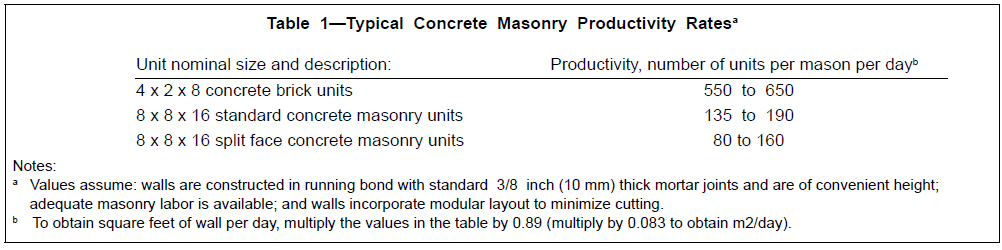
Pre-Bid and Pre-Construction Conferences
Pre-bid and pre-construction conferences should be held and attended by all parties involved in the masonry work including the owner’s representative, the architect/engineer, the contractor, the construction manager, the masonry material suppliers and the mason contractor. This facilitates good communication prior to the commencement of work and prior to the development of any misunderstandings. Clear communication minimizes delays due to factors such as lastminute changes and errors.
Proper Design
Quality design means that the designer has:
- designed and detailed a project that is constructible,
- developed plans and specifications that are sufficient for construction and are complete with the proper code and standards referenced,
- reviewed the plans, specifications and structural drawings to eliminate conflicting words and conflicting details,
- included the input of a quality mason contractor, and
- incorporated all masonry materials into CSI Division 4. (Often, some mason materials are found in division 7. If all of the mason’s work is placed into Division 4, it enhances communication with the masonry team and has a better chance of being properly incorporated into the job.) Similar to the pre-bid and pre construction conferences, a comprehensive set of plans and specifications will help enhance productivity because it will reduce or eliminate time spent correcting misunderstandings and errors.
A complete set of plans and specifications will include a copy of Building Code Requirements for Masonry Structures and Specification for Masonry Structures (refs. 1, 2), the national consensus standards for masonry design and construction. In addition, applicable ASTM standards should be included for specifying masonry materials.
Planning and Layout
Attention to planning of the building itself and of construction sequencing and scheduling can impact masonry productivity.
Concrete masonry structures can be constructed using virtually any layout dimension. However, for maximum construction efficiency and economy, concrete masonry elements should be designed and constructed with modular coordination in mind. Modular coordination is the practice of laying out and dimensioning structures to standard lengths and heights to accommodate modular sized building materials. Standard concrete masonry modules are typically 8 in. (203 mm) vertically and horizontally, but may also include 4in. (102 mm) modules for some applications. These modules provide the best overall design flexibility and coordination with other building products such as windows and doors. Typically, masonry opening widths for doors and windows should be 4 in. (102 mm) larger than the door or window width. This allows for 2 in. (51 mm) on each side of the opening for framing. Masonry opening heights for windows typically are 8 in. (203 mm) greater than the window height. This opening size allows for 2 in. (51 mm) above and below for framing and 4 in. (102 mm) for installing a sill at the bottom of the window. Masonry opening door heights are 2 in. (51 mm) greater than the door height, which leaves 2 in. (51 mm) for the door framing. Figure 2 illustrates these opening sizes.
Thus, door and window widths of 28 in., 36 in., 44 in., and 52 in. (711, 914, 1118 and 1,321 mm), and so on in 8 in. (203 mm) increments, are modular and would not require cutting of the masonry. Modular window heights are any multiple of 8 in. (203 mm), with a masonry window opening 8 in. (203 mm) greater than the height of the window if a 4 in. (102 mm) sill will be used. Similarly, a modular door height is 2 in. (51 mm) less than any multiple of eight. Thus, an 86 in. (2,184 mm) high door, which fits into an 88-in. (2,235 mm) high masonry opening, has a modular height.
Note that products are available in some locations to accommodate 6’ 8” (2,032 mm) doors in masonry walls without the need for cutting the masonry units. These include precast lintels with a 2 in. (51 mm) notch which provides the necessary 6’ 10” (2,083 mm) masonry opening to accommodate the door and frame. In other areas, door frames are available with a 4 in. (101.6 mm) header which would allow a 6’ 8” (2,032 mm) door to fit into 7’ 4” or 88 in. (2,235 mm) high masonry opening.
Nonmodular layouts may require additional considerations for items such as using nonstandard units or saw cutting masonry units and maintaining bond patterns. Additionally, other construction issues may arise, such as placement of jamb reinforcement and adequate grout consolidation within small core spaces. The end product typically is more difficult to construct, produces more waste and is more costly.
Similarly, coordinating the placement of pipes, ducts, chases and conduits to align them with hollow masonry cores can reduce the need to saw-cut masonry units.
Steel congestion in reinforced masonry can slow productivity. Placing too many reinforcing bars in too small a space makes it difficult to place the steel and to provide adequate grout coverage. Specification for Masonry Structures (ref. 3) requires 1/4 in. (6.4 mm) clear space between the reinforcing bar and the masonry for fine grout and 1/2 in. (13 mm) clear space for coarse grout.
Sample panels reduce misunderstandings and provide an objective indicator of the intended construction practices. They help ensure all parties understand the range of materials, methods and workmanship acceptable on the job. Sample panels are typically at least 4 ft by 4 ft (1.22 x 1.22 m) and should contain the full range of unit and mortar colors. Selecting units of all one shade for the sample panel will not accurately reflect the completed work. Instead, units should be randomly selected as they would in the project construction. Cleaning procedures, sealant application and all other procedures should be performed on the sample panel so that their acceptability can be judged as well. The sample panel should remain in place throughout construction as a point of reference.
For maximum productivity, timely delivery of the units, mortar, grout and other masonry materials will help expedite the job. In addition, schedule masonry work to avoid times of the year particularly subject to freezing temperatures or prolonged rains whenever possible. Although masonry construction can take place during hot, cold and wet weather conditions, special construction procedures may be warranted in some cases to ensure the masonry quality is not impacted by the weather. More detailed information on these construction procedures can be found in All-Weather Concrete Masonry Construction (ref. 4).
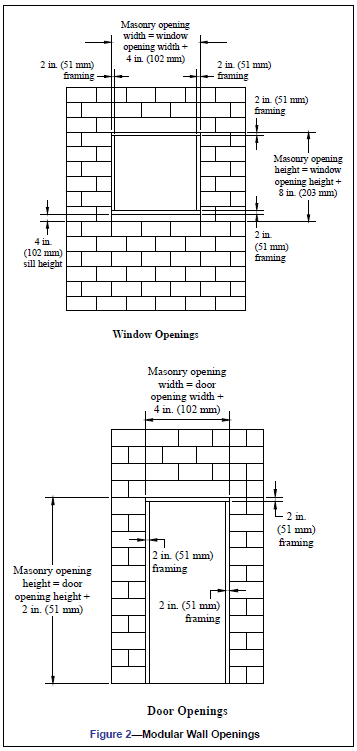
Quality Materials
Masonry materials have a successful history of meeting applicable specifications and project requirements. Ensuring that the materials used are as specified helps keep the masonry construction on track. ASTM standards for masonry units, for example, specify dimensional tolerances for the units. Units meeting the ASTM tolerances will be easier to place, and allow the mason to more easily maintain level and alignment. Similarly, units without excessive chippage (a characteristic also governed by ASTM standards) allow placement without the need for sorting the product for quality—an activity that reduces overall productivity.
Jobsite
A quality jobsite helps productivity by including ample space for the mason subcontractor to work and having easy access to the masonry supplies. This includes having:
- undisturbed space for building the sample panel(s),
- a defined and ample-sized area for materials and supplies, and
- a defined and ample-sized area for sampling and testing procedures as required for the project.
Proper Installation
In addition to the factors cited above, quality installation requires:
- an ample number of qualified craftsmen,
- qualified and sufficient supervision, and
- the right equipment for the job.
There have been some marvelous developments in products and equipment to assist masons and hence increase masonry productivity. For example, newer fork lifts often have increased capacity, a single boom which increases visibility, are more maneuverable, have higher load ratings and higher extensions. Other equipment advances that can enhance productivity include portable hand-held lasers that work in numerous directions simultaneously, electric portable winches and power (crank-up or hydraulic) scaffolding. Products that are easier for the mason to install, such as self-adhesive flashings and pre-formed flashing end dams, can also impact masonry productivity.
Choice of mortar can also impact productivity. Masonry and mortar cements provide more consistency because all of the cementitious ingredients are premixed. Premixed mortars, which include the sand mixed with the appropriate cement, are also available in silos or in mixers or blenders. Premixed mortars can improve mortar quality control and uniformity and can also increase productivity by eliminating the need for job site mixing.
In some cases, work by other trades can also impact masonry
productivity. For example, poured concrete foundations or footings which do not meet their tolerances may require the mason to saw-cut the first course of block, or take some other measure, to compensate.
REFERENCES
- Building Code Requirements for Masonry Structures, ACI 530-02/ASCE 5-02/TMS 402-02. Reported by the Masonry Standards Joint Committee, 2002.
- Specification for Masonry Structures, ACI 530.1-02/ ASCE
6-02/TMS 602-02. Reported by the Masonry Standards Joint Committee, 2002. - All-Weather Concrete Masonry Construction, TEK 03-01C,
Concrete Masonry & Hardscapes Association, 2002. - Kolkoski, R. V. Masonry Estimating. Craftsman Book Company, 1988.
- Research Investigation of Mason Productivity. Concrete Masonry & Hardscapes Association, 1989.