INTRODUCTION
Masonry structures have been used for centuries throughout the world. Concrete masonry units, however, are a relatively recent innovation. Initially, these units were made with hand operated equipment, although by the 1940’s, block production had developed to incorporate automated mixing, molding, and curing methods, resulting in consistent quality of materials. These new manufacturing processes allowed concrete masonry to be used in engineered structural systems such as multistory load-bearing structures.
In the late 1940’s, one of the first examples of engineered multistory construction was used by Professor Paul Haller in Switzerland. Today there are many examples of loadbearing masonry buildings up to 15 to 28 stories high.
The modular nature of concrete masonry units makes construction straightforward and the small unit size makes changes in plan or elevation easy. Special unit shapes are manufactured to accommodate reinforcement. Open end units, with one or both end webs removed, permit the placement of units around vertical reinforcing bars. Slots manufactured into the webs of units (termed bond beam units) are used to position horizontal reinforcement within the wall.
Concrete masonry is widely used because of the strength, durability, economy, architectural appeal, and versatility of the masonry system. A major milestone in the advancement of engineered concrete masonry was the establishment of the Specifications for Design and Construction of Load Bearing Concrete Masonry by CMHA in the late 1960’s (ref.1). This served as the building code for engineered concrete masonry structures and was adopted by the Southern Building Code Congress and other model codes. It has evolved into our present-day Building Code Requirements for Masonry Structures (ref. 2) and Specification for Masonry Structures (ref. 3).
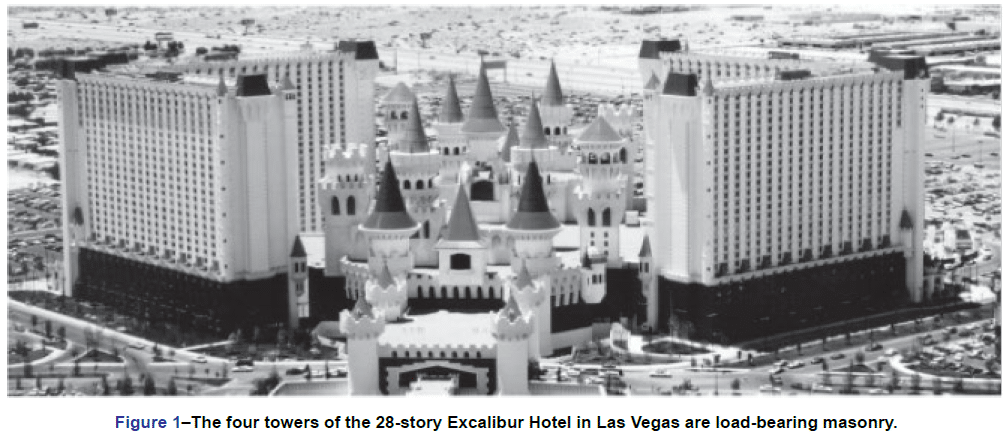
One of the earliest wall bearing concrete masonry structures using this new technology was a nine story senior citizens building in Cleveland, Tennessee which was built in 1969 utilizing partially reinforced concrete masonry walls.
In our world of economics, the bottom line is still a deciding factor in determining a building’s construction type. The real economy of concrete masonry lies in utilizing the strength of the masonry units (making them load-bearing) and minimizing the cutting of the modular building unit by utilizing multiples of 8 in. for building dimensions and openings. Regarding finish, the most economical one of course is normally plain, painted block. However, if the owner’s budget permits enhancements, a wide variety of architectural units are available (i.e. colored, splitface, scored, fluted, burnished, and slump block). Prefaced units with a glazed finish, vibrant colors and graffiti resistance are also available. Architectural units not only provide pleasing aesthetics but also greatly reduce maintenance and upkeep costs. Additionally, stucco or a variety of proprietary finishing systems also can be applied.
BUILDING TYPES
Most concrete masonry multistory buildings fall into two main types; loadbearing shear wall-type buildings and infilled walls. The Uniform Building Code (ref. 4) has also recently approved a design method for moment-resisting masonry wall frames.
Loadbearing/Shear Wall Buildings
Loadbearing concrete masonry shear wall buildings make the most effective use of concrete masonry by relying on both the economy and the structural capacity—compressive strength and shear resistance—of the concrete masonry. The most common application uses concrete masonry walls with concrete floor and roof diaphragms. The concrete diaphragms can be poured in place, although precast hollow core slabs are the most common.
Concrete masonry/precast slab buildings provide a fast, economical construction method that has allowed some builders to construct one story each week. Floors are enclosed quickly, so that mechanical, electrical, plumbing, and other contractors can begin working on one floor while masonry wall and plank construction continues on floors above them.
Concrete Masonry Infill
Infilled concrete masonry walls utilize the concrete masonry as cladding and interior partitions between concrete or steel frames, which form the structural load-resisting system. Concrete masonry walls are often used in this application because of the cost effectiveness and ease of construction. Historically, most of these walls have been constructed using standard concrete masonry units which were painted or plastered. More recently, however, architectural units are being used to eliminate the need for finishing the walls.
Construction of infilled masonry walls is usually straightforward since the main building system is in place prior to the masonry construction. The most important consideration is whether “gapped” or “ungapped” infilled walls will be provided. Gapped infilled walls are constructed with a predetermined space between the masonry and the building frame. These gaps act as isolation joints, allowing the building frame to drift and sway under lateral loads. Ungapped infilled walls, by contrast, are constructed tightly against the building frame so that the infilled walls serve as shear walls.
DESIGN CONSIDERATIONS
The typical specified compressive strength of concrete masonry, f’m, is 1500 psi (10.3 MPa). However, using high strength concrete masonry units, f’m values up to 4000 psi (27.6 MPa) are achievable. These high strength units are often specified on high-rise loadbearing projects to minimize wall thickness. For further economy, some designers specify lower f’m values in the upper stories, where the higher compressive strength is not needed, since high strength units may cost more than standard units. For example, the four, fast-track, 28-story towers of the $300 million, 4,000 room Excalibur hotel in Las Vegas, Nevada, used an f’m of 4000 psi (27.6 MPa) for the loadbearing walls on the first thirteen floors (ref. 5). The specified compressive strength decreased in successive stories, until the top floors where standard block with an f’m of 1500 psi (10.3 MPa) was used.
Contractors prefer repetitive floor plans for high-rise construction. This important design feature allows similar construction and provides structural continuity from floor to floor both of which lend to economy in construction. The same holds true for architectural details. Designs which facilitate scheduling repetitive, “assembly-line” construction procedures improve productivity and reduce construction costs. Obviously, aesthetic and functional constraints must also be considered, so that buildings are useful and attractive as well as economical.
Connections between building elements is key to the performance of the structures and should therefore be considered carefully during the design process. Connections should be simple and easy to construct and, where necessary, should accommodate building movements from expansion and/or contraction of building materials.
Differential movement deserves particular attention on high-rises where concrete masonry is clad with clay brick. Concrete materials tend to shrink, while clay tends to expand. Over the height of many stories, these opposing movements can be significant. In one case, the seventeen story Crittenden Court in Cleveland, Ohio, these movements were accommodated by designing the exterior brick as a reinforced curtain wall supported on the foundation (ref. 6). The brick was tied to the precast concrete floor planks using slotted anchors that allow vertical but not horizontal movement. This accommodates the differential movement, and also provides enough lateral stiffness to transfer wind and seismic loads from the brick to the floor diaphragms.
Because of the large size of most multistory buildings, a predefined quality control/quality assurance plan is recommended. Inspection, to ensure that key building elements have been installed properly, is essential to assure that the building was constructed as designed. Material testing may be required by the Specifications for Masonry Structures or the contract documents to verify that supplied materials meet the project specifications. As with all construction, tolerances should be carefully monitored. Steel or concrete frames constructed out of tolerance make the mason’s job difficult and slow. Proper alignment of these elements will facilitate the construction process and provide a more appealing completed structure.
CONSTRUCTION
Construction Materials
For construction to proceed smoothly and quickly, it is necessary to carefully schedule construction procedures and supply of materials. Where space allows, it is preferable to stockpile materials on site so that they are readily available when needed. For small sites, material delivery must be timed so that the materials can be moved quickly to the place they are needed.
Materials are delivered to the masons on upper stories via crane or hoist. Materials can either be stocked from the building floors, or can be placed on the work platform, if the platform is large enough and can support the weight. Coordination with crane and elevator schedules should also be considered so that they are available when materials arrive on site.
An adequate supply of concrete masonry units for the entire story should be supplied at one time. Mortar materials can be mixed using traditional techniques, although silo mix mortar systems have become increasingly popular. These systems deliver 14 to 28 yd3 (10.7 to 21.4 m3) of mortar ingredients, and produce consistent mortar from batch to batch. Additional advantages include ability to be lifted easily from floor to floor, mortar containment, and easy cleanup.
Reinforcement cut to proper length and provided in bundles for each story level also facilitates construction. Grout is typically supplied via ready-mix trucks and is pumped to the top of the wall or is lifted using cubic yard buckets. Silo mixed grout is also supplied on some jobs. Also, as with all grouted masonry, it is vitally important that the grout has a slump between 8 and 11 in. per the Specification for Masonry Structures for proper placement and final performance of the building.
Placing the Masonry
Concrete masonry can either be laid from the inside of the building with the masons working on the interior floor area or from the outside of the building with the masons working on scaffolds or work platforms. The choice depends on the size of the job, type of construction, and mason’s preferences.
Laying Units from inside the Building
For load-bearing and infilled exterior walls, concrete masonry can often be laid from the inside of the building. This normally is the most efficient and cost effective method as this allows the masons to work on the building’s floor area providing ample room for units, mortar, and other building materials. Since the mason’s work is confined to the perimeter of the floor, other trades can also work at the same time. Laying from the interior may also be an advantage in windy conditions, when work on exterior platforms may be limited.
Block for the next story are normally stacked on the concrete floor as soon as it has hardened enough to prevent damaging the surface, usually a couple of hours after the steel troweling is completed. An example of this is a hotel structure where the wall between each room is a bearing wall and the floor system is a concrete, one-way, continuous slab. To ensure structural adequacy and maximum economy, two practices must be observed: 1) no shoring can be removed until the next story of walls has been laid up, and 2) sand must be spread over the new slab to facilitate cleanup of any dropped mortar.
For masonry veneers laid from the interior, the building design and construction must accommodate the construction technique. For example, if the walls are masonry veneer with concrete masonry backup, both masonry wythes can easily be laid at the same time. If, on the other hand, the interior wythe is steel studs with sheathing, the veneer would have to be placed from the exterior. Similarly, large columns and deep beams may interfere with masonry veneer placement from the interior.
One drawback to laying units from the inside of the building is that more time is typically required to place the units to assure they align on the exterior since the masons are facing the interior, unexposed, side of the wall. However, this decrease in productivity is often offset by large reductions in scaffolding costs, which can be substantial. Although some scaffolding is needed to lay the top portion of each wall, only one level of scaffold is required.
Laying Units from Work Platforms
Scaffolds and other temporary work platforms allow the masons to work facing the exposed side of the masonry, making it easier to ensure the exposed side is laid plumb and level. Most mason contractors own a supply of scaffolding, but often must rent supplemental scaffolds for high-rise construction. Time should be allotted for placing, dismantling, and moving scaffolds on the job.
Two alternatives to traditional scaffolding for high-rise construction are powered mast-climbing platforms and suspended scaffolds. Both eliminate the labor required to construct multiple levels of conventional scaffolding.
Powered mast-climbing work platforms are erected on the ground and use electric or hydraulic power to move the platform up and down the supporting mast or masts (ref. 7). The masts are attached to the building using adjustable ties or anchors.
One advantage of these systems is that the platform can be easily moved in small increments. This means the platform can be adjusted as the wall is laid to keep it at the mason’s optimum working height. This reduces the amount of lifting of individual units and improves productivity. Powered mast-climbing platforms have maximum heights ranging from 300 to almost 700 ft (91 to 213 m), depending on the type chosen. Other variables include maximum safe wind exposure, attachment requirements, speed, and optional equipment such as overhead protection.
Suspended scaffolds (ref. 8) are work platforms that are suspended from either the roof of the building or from an intermediate floor and therefore would mainly be limited to use on infill projects where the structural frame precedes the wall. Like the mast-climbing platforms, the suspended scaffolds are adjustable in small increments to keep the platform at the optimum working height for the masons. Most suspended scaffolds are raised and lowered by hand, rather than by a powered system. The attachment requirements for suspended scaffolds are fairly complex, and are typically designed for each project and installed by the scaffold supplier.
Suspended scaffolds have the advantage of keeping the lower floors of the building accessible once the work has progressed above this point. They may also be preferable on sloping sites where erection of frame scaffolding would be difficult.
Suspended scaffolds typically become cost effective at building heights of seven to ten stories. Below this height, traditional or power mast scaffolding is probably more cost effective.
CONCLUSION
Many economical concrete masonry structures have been built around the country ranging from buildings to over twenty stories in height to fifteen foot high retaining walls. Rapid growth in areas like that of Orlando, Florida, spurred by the arrival of Disney World produced a market for quality, economical building systems. Concrete masonry construction and the early CMHA Specification for Design and Construction of Load-Bearing Concrete Masonry were ready with the technology to allow engineers and architects to design economical and aesthetically pleasing structures. High-rise buildings have seen an unprecedented growth with modern, innovative construction methods, proper engineering design and use of concrete masonry materials.
REFERENCES
- Specification for Design and Construction of Load-Bearing
Concrete Masonry, Concrete Masonry & Hardscapes
Association, 1970. - Building Code Requirements for Masonry Structures, ACI
530-95/ASCE 5-95/TMS 402-95. Reported by the Masonry
Standards Joint Committee, 1995. - Specification for Masonry Structures, ACI 530.1-95/ASCE
6-95/ TMS 602-95. Reported by the Masonry Standards
Joint Committee, 1995. - Uniform Building Code. Whittier, CA: International
Conference of Building Officials (ICBO), 1997. - Keating, Elizabeth. “A Floor a Week per Tower.” Masonry
Construction, November 1989. - Keating, Elizabeth. “Powered Mast-Climbing Work
Platforms.” Masonry Construction, May 1997. - Wallace, Mark A. “Loadbearing Masonry Rises High in
Cleveland.” Masonry Construction, May 1997. - Hooker, Kenneth A. “Suspended Scaffolds Cut High-Rise
Masonry Costs.” Masonry Construction, March 1991.