Revised 2022
Bedding sands are a critical component of all sand-set segmental concrete paving systems. Especially for vehicular applications, specifiers and contractors need to consider bedding sand selection. While gradation is an important consideration, other characteristics should be assessed in order to ensure long- term pavement performance. This technical bulletin examines these characteristics and provides guidance to specifiers and contractors.
BACKGROUND
Bedding sand provides four main functions. It beds the pavers during installation; helps initialize interlock among the pavers; provides a structural component for the system (as described in CMHA Tech Note PAV-TEC-004–Structural
Design of Interlocking Concrete Pavement for Roads and Parking Lots) and facilitates drainage of water that infiltrates through the joints. Typical specifications require bedding sands to conform to ASTM C33 Standard Specification for Concrete Aggregates and CSA A23.1 Concrete materials and methods of concrete construction FA1 gradation for concrete sands with an additional limit of 1% passing the No. 200 (0.075 mm*) sieve (See Table 1). To achieve this low percentage of fines, washing the sand is typically required. A common name for the recommended bedding material is washed concrete sand. In vehicular applications, experience and research have shown that other factors besides gradation contribute to the successful function of the bedding layer in vehicular applications. Knapton (1994) notes that since 1980 the amount of material passing the No. 200 (0.075 mm) sieve has been reduced in the British Standard BS 7533-1 Pavements constructed with clay, concrete or natural stone paving units. Code of practice for the structural design of pavements using modular paving units. He notes that fines have reduced from 10% in 1980, to 3% in 1991, to 1% for heavily trafficked pavements, further reducing to 0.1% for bus stations. North American standards currently limit the amount of allowable material passing these sieves to 1%.
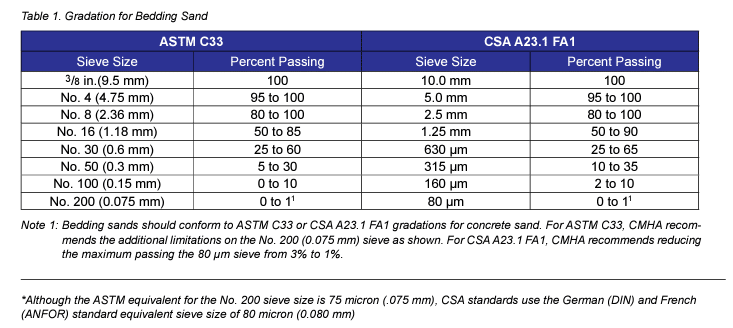
Other studies (Lilley and Dowson 1988) (Beaty 1996) have investigated failures of segmental concrete pavements subjected to channelized vehicular traffic. They have also concluded that more comprehensive specifications are required. Lilley and Dowson (1988) suggested that bedding sands in segmental concrete pavements designed to carry more than 1.5 million equivalent standard axle loads, ESALs (18 kip/80 kN), should be subjected to grading and degradation tests. For the purposes of this Tech Note, vehicular traffic is defined as roads exposed to a minimum of 1.5 million lifetime ESALs and axle loads up to 24,250 lbs (11,000 kg).
FAILURE MECHANISMS
Failure of the bedding sand layer occurs in channelized vehicular loads from two main actions; structural failure through degradation and saturation due to inadequate drainage. Since bedding sands are located high in the pavement structure, they are subjected to repeated applications of high stress from the passage of vehicles over the pavement (Beaty 1996). This repeated action, particularly from higher bus and truck axle loads, will degrade the bedding sand and cause failure. For these applications sand should be selected based on their ability to withstand long-term degradation.
Bedding sand permeability also is a significant factor in the selection process. Wherever difficulties have been experienced with laying course materials in heavily trafficked pavements, water has been a major factor (Knapton 1994). As they approach higher moisture levels in service, bedding sands may become unstable. Smaller particle sizes (fines) become suspended in water, forming slurry that lubricates the entire bedding layer. Choosing bedding sand with a gradation as shown in Table 1 will help to reduce the risk of poor drainage and instability. However, these sands will be susceptible to drainage problems if they do not have the hardness to withstand long term degradation from vehicular wheel loads.
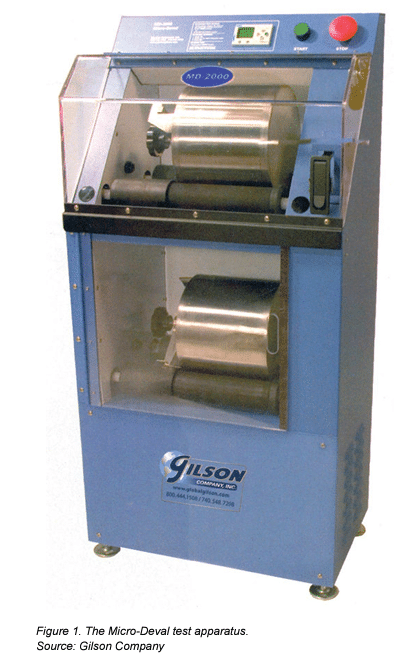
SELECTION AND PERFORMANCE DESIGN PRINCIPLES—GOING BEYOND GRADATION
Selecting Durable Bedding Sands—Durability of aggregates has long been understood to be a major factor in pavement performance. ASTM C88 Soundness of Aggregate by use of Sodium Sulfate or Magnesium Sulfate is an example of a typical test method used by road agencies to assess aggregate durability. The test involves soaking an aggregate in a solution of magnesium or sulfate salts and oven drying. This is repeated for a number of cycles, with each cycle causing salt crystals to grow and degrade the aggregate. The test method takes a minimum of 6 days to complete. The percent loss is then calculated on individual size fractions. This test method, however, is considered highly variable. Jayawickrama, Hossain and Phillips (2006) note that when ASTM initially adopted this test method they recognized the lack of precision, saying, “it may not be suitable for outright rejection of aggregates without confirmation from other tests more closely related to the specific service intended.” CMHA recommends using ASTM C88 as a measure of aggregate durability as long as other material properties described in this bulletin are also considered.
The Micro-Deval test is evolving as the test method of choice for evaluating durability of aggregates in North America. Defined by CSA A23.2-23A, The Resistance of Fine Aggregate to Degradation by Abrasion in the Micro-Deval Apparatus and ASTM D7428 Standard Test Method for Resistance of Fine Aggregate to Degradation by Abrasion in the Micro-Deval Apparatus, the test method involves subjecting aggregates to abrasive action from steel balls in a laboratory rolling jar mill. In the CSA test method a 1.1 lb (500 g) representative sample is obtained after washing to remove the No. 200 (0.080 mm) material. The sample is saturated for 24 hours and placed in the Micro-Deval stainless steel jar with 2.75 lb (1250 g) of steel balls and 750 mL of tap water (See Figure 1). The jar is rotated at 100 rotations per minute for 15 minutes. The sand is separated from the steel balls over a sieve and the sample of sand is then washed over an 80 micron (No. 200) sieve. The material retained on the 80 micron sieve is oven dried. The Micro-Deval loss is then calculated as the total loss of original sample mass expressed as a percentage. ASTM and the American Association of State Highway Transportation Officials have both adopted the coarse aggregate version of the Micro-Deval test, ASTM D6928 and AASHTO TP 58. Both are also considering a version for fine aggregates. Since the test apparatus uses the same size drum and rotates at the same speed, no modifications to the apparatus are required to perform the fine aggregate test in laboratories currently equipped to perform the coarse aggregate test procedure.
A study conducted by the Interlocking Concrete Pavement Institute (ICPI 2004) investigated nine sands from across the United States reported by contractors to have “good to excellent” serviceability in vehicular applications. The results of this study indicated that eight of these sands had Micro-Deval degradation losses less than 8% when measured according to CSA A23.2-23A. The same study subjected these sands to the ASTM C88 soundness loss and found that no sample had greater than 6% loss. The Micro-Deval test is recommended as the primary means to characterize bedding sand durability (See Table 3) and the magnesium or sulfate soundness should be considered when the Micro-Deval test is not locally available. The variability of the soundness test method should always be a consideration unless measured in relation to other material properties.
A test method similar in nature to Micro-Deval is the Lilley and Dowson test (Lilley Dowson 1998). This test method specifically developed for bedding sands is recognized internationally and is referenced in CMHA manuals Port and Industrial Pavement Design with Concrete Pavers and Airfield Pavement Design with Concrete Pavers. This test method is performed on 3 lbs (1.4 kg) randomly selected, oven-dried sand samples with two 1 in. (25 mm) diameter steel balls together weighing 0.3 lb (135 g). Three sub-samples each weighing 0.5 lbs (0.2 kg) are derived from the main sample. Each sub-sample is sieved according to ASTM C136 then re-mixed and placed in a nominal liter capacity porcelain jar with the two steel balls. The three jars are rotated at 50 rpm for six hours and sieved again. Sand durability is assessed from resulting increases in the percent passing the No. 50, 100 and 200 (0.300, 0.150, and 0.075 mm) sieves. Developed in the UK, the test is not readily available at laboratories in North America. The CSA and ASTM Micro-Deval tests may be more available.
Beaty (1996) demonstrated a correlation between the two tests with a correlation coefficient greater than 0.99. The relationship between the two tests is:
L = 1.97 + 1.21 M
Where:
M = CSA Micro-Deval Degradation Loss (%)
L = Lilley and Dowson Degradation Loss (%)
Beaty’s correlation involved a modification to the test procedure by reconstituting the test aggregates into a standard gradation shown in Table 2 and performing the Micro-Deval and Lilley Dowson tests on the re-graded aggregate. In this modified version of the Lilley Dowson test procedure the loss (L) is measured as the total increase in percentage of fines passing the No. 200 (0.075 mm) sieve at the completion of the test. Using the correlation described above, an 8% Micro Deval degradation (See Table 3) would have a corresponding Lilley and Dowson degradation of 12%.
Bedding Layer Drainage—Bedding layer drainage is important for early and long term performance of a pavement. One failure documented by Knapton (1993) describes a segmental pavement that was opened to bus traffic and within hours of construction subjected to continuous heavy rain. The bedding sand in this case had a high percentage of fines. As a result of the continuous rainfall, finer sieve fractions in the sand were transported into the drain holes of the underlying concrete slab. With the drainage compromised the bedding sand liquefied and was pumped through the joints of the pavement, resulting in immediate rutting and failure of the system. The pavement was subsequently reconstructed with bedding sand that had 0% material passing the No. 200 (0.075 mm) sieve and reported excellent performance. Although gradation is an important factor in drainage (since it affects permeability) eliminating all of the fines can sometimes be impractical. Therefore, CMHA recommends up to 1% passing the No. 200 (0.075 mm) sieve.
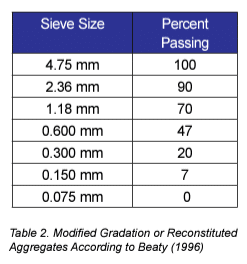
Another important material property is permeability. Even specifications that allow up to 3% of fines can result in a five fold decrease in permeability from the lowest to highest percentage passing (Bullen 1998). In research conducted by the Interlocking Concrete Pavement Institute (ICPI 2004) the permeability of “very good to excellent” bedding sands was measured. Using the test method described by ASTM D2434 Standard Test Method for Permeability of Granular Soils (Constant Head) the permeabilities ranged from 2.8 in./hr (2.1 x 10-3 cm/second) to 15.6 in./hr (1.1 x 10-2 cm/second). These values correspond to fines that range from 2.5% to 0% passing the No. 200 (0.075 mm) sieve but, more importantly they also are associated with Micro-Deval maximum degradation values of 8%. Table 3 indicates a minimum permeability of 2.8 in./hr (2.1 x 10-3 cm/second) that should also be considered at the same time as the other primary properties listed.
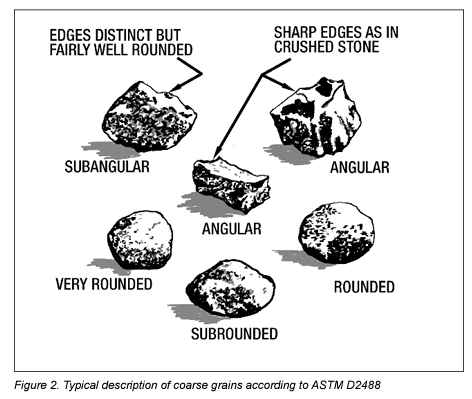
Other Material Properties—Studies have indicated that bedding sand shape plays a role in bedding sand performance. (Knapton 1993) notes that rounded or cubic grains lead to stable sands, whereas more angular grains are frequently associated with sands that fail. The sands tested by ICPI (ICPI 2004) showed that eight of the nine “good to excellent” performing sands were characterized by having a predominance of sub- angular to sub-rounded particle shapes when tested according to ASTM D2488 Description and Identification of Soils (Visual- Manual Procedure). Specifiers and contractors should consider bedding sand angularity using Figure 2 as a guide. Figure 3 shows a photograph of one of the ICPI test sands at high magnification. Table 3 suggests that a combined percentage of sub-angular to sub-rounded particles should be a minimum of 60%.
Geology—Geology of bedding sands has been noted by a number of studies to play an important role in their performance. For example, bedding sand with quartz mineralogy is preferred over crushed sandstones (Knapton 1993). In the study by the Interlocking Concrete Pavement Institute (ICPI 2004), eight of the nine “good to excellent” performing sands were noted to consist predominately of silica minerals with over 80% of the material either quartz or quartzite. Table 3 recommends a minimum 80/20 ratio of silica/ carbonate mineralogy. A tenth sample, included in the study (and noted as poor performing in the field) was characterized as having up to 50% carbonate content. Petrographic analysis was conducted according to the Ministry of Transportation of Ontario laboratory method MTO LS-616 Procedure for the Petrographic Analysis of Fine Aggregate (MTO 1996). ASTM C295 Standard Guide for Petrographic Examination of Aggregates for Concrete offers an alternative test method.
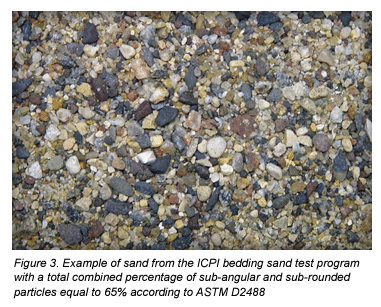
Limestone screenings and stone dust are not recommended for bedding sand. In addition to being unevenly graded and having excessive material passing the No. 200 (0.075 mm) sieve, screenings and stone dust will break down over time from wetting and abrasion due to vehicular loads. Unlike soft limestone screenings and stone dust, hard, durable concrete sand meeting the requirements in Table 3 will not break down easily. Limestone screenings also tend to break down during pavement construction under initial paver compaction. Depressions will eventually appear in the pavement surface with limestone screenings or stone dust.
Recommended Material Properties—Table 3 lists the primary and secondary material properties that should be considered when selecting bedding sands for vehicular applications. Bedding sands may exceed the gradation requirement for the maximum amount passing the No. 200 (0.075 mm) sieve as long as the sand meets degradation and permeability recommendations in Table 3. Micro-Deval degradation testing can be replaced with sodium sulfate or magnesium soundness testing as long as this test is accompanied by the other primary material property tests listed in Table 3. Other material properties listed, such as petrography and angularity testing content range of 6% to 8% has been shown to be optimal for most sands (Beaty 1992). Contractors can assess moisture content by squeezing a handful of sand in their hand. Sand at optimal moisture content will hold together when the hand is re- opened without shedding excess water. Although it can be difficult to control the exact moisture content on the job site, uniformity of moisture content can be maintained by covering stock piles with tarps. Digging into sand piles at mid- height to avoid saturated material that may be at the bottom of the pile is also recommended.
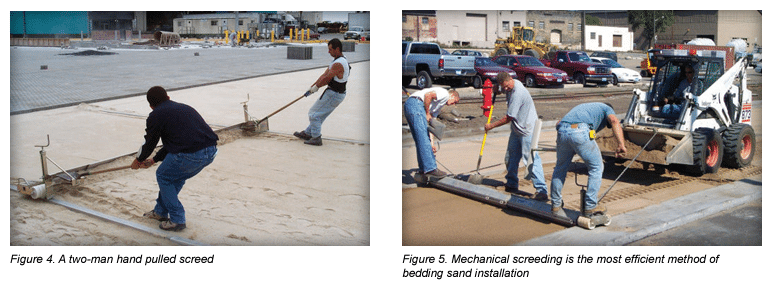
While on the job site, a contractor should check the hardness of the bedding sand particles. Particles of sufficient hardness will not break under the pressure of a Swiss Army pocket knife. This field test, although not recommended for pre-selection of bedding sands, helps assess a material at the time of delivery. Table 4 lists the recommended bedding sand properties that need to be considered by a contractor during installation.
Interlocking concrete pavements should also be designed and constructed such that the bedding sand should not be able to migrate into the base, or laterally through the edge restraints. Dense- graded base aggregates with 5% to 12% fines (the amount passing the No. 200 or 0.075 mm sieve), will ensure that the bedding sand does not migrate down into the base surface. For pavements built over asphalt or concrete bases, it is necessary to provide adequate drainage by providing 2 in. (50 mm) diameter weep holes around the perimeter on 10 ft (3 m) centers and at the low points in the concrete base to drain excess water from the bedding layer. Holes should be filled with washed angular gravel and covered with geotextile to prevent the loss of bedding sand. Figure 6 on the next page shows a detail. Specifiers can visit the CMHA website to download similar details for use in specifications from www.masonryandhardscpes.org. To control lateral loss of bedding sand, Figure 7 shows geotextile installed at the interface of a concrete curb. To ensure that the sand cannot migrate through the joints in the curb woven geotextile is placed on top of the aggregated base, extending approximately 1 ft. (300 mm) into the pavement and wrapped up the sides of the curb to fully contain the bedding sand.
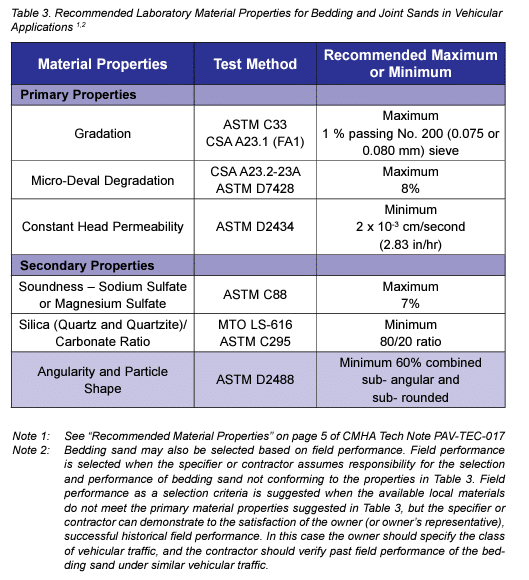
ROLE OF JOINTING SAND
Jointing sand provides two primary functions in a segmental concrete pavement; it creates interlock and helps seal the pavement. CMHA recommends that the same material properties listed in Table 3 also apply to jointing sand. Panda and Ghosh (2002) describe laboratory research on pavements using fine and coarse joint sands. Simulated loading consisted of 11-kip (51 kN) over 80 mm pavers with varying joint widths and joint sand gradations. Deflection of the pavement was then measured with coarser sand exhibiting lower deflections. The study concluded that “the coarser the sand, the better the performance.” The coarser sands used in the study correspond to the gradations for Joint Sand listed in Table 1 and the study recommended joint widths up to 3/16 in. (5mm). CMHA recommends joint widths of 1/16 to 3/16 (2 mm to 5 mm).
Contractors can benefit from using one sand source. There are advantages to using the bedding material for the jointing sand during construction. Using one material allows the contractor to monitor and control one sand product on the job site. Over time the joints become filled with detritus, providing some degree of sealing. Regardless of the sand used, segmental concrete pavements will always allow some water penetration through the joints.
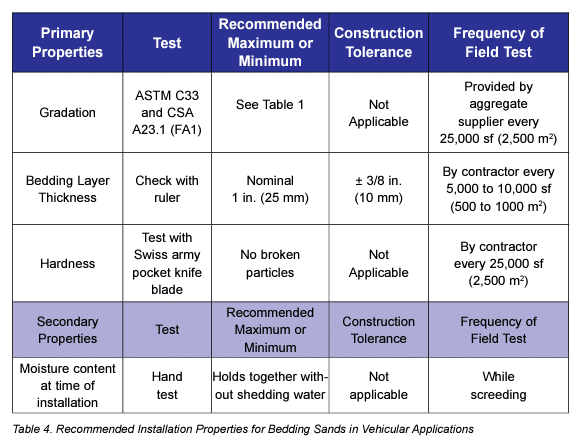
Coarse bedding sand may require additional effort to place it in the joints. In some cases, smaller joint widths may require the use of finer graded sand. In this case, the use of mortar sand is recommended. Mortar sand should conform to the gradations of either ASTM C144 or CSA A179 but should also meet the material property requirements of Table 3.
Although joint sand selection is an important factor, design and construction play a more important role. Considerations such as joint width, ensuring that the sand is swept in dry, degree of compaction, and ensuring the joints are completely filled, are just as critical to the long term success of pavement performance. Information on joint sand installation can be found in CMHA Tech Note PAV-TEC-002—Construction of Interlocking Concrete Pavements).
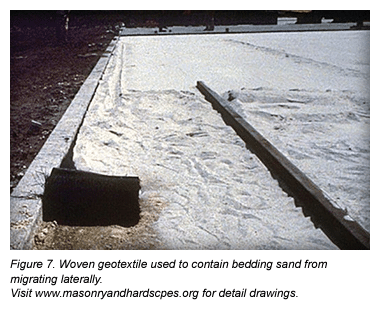
MAINTENANCE OF INTERLOCKING CONCRETE PAVEMENT
Occasionally interlocking concrete pavements will require maintenance for them to deliver peak performance. Refer to Tech Note PAV-TEC-006–Operation and Maintenance Guide for Interlocking Concrete Pavement for information on preventative maintenance, identifying and remedying aesthetic and structural distresses and best practices for the disassembly and reinstatement of interlocking concrete pavement.
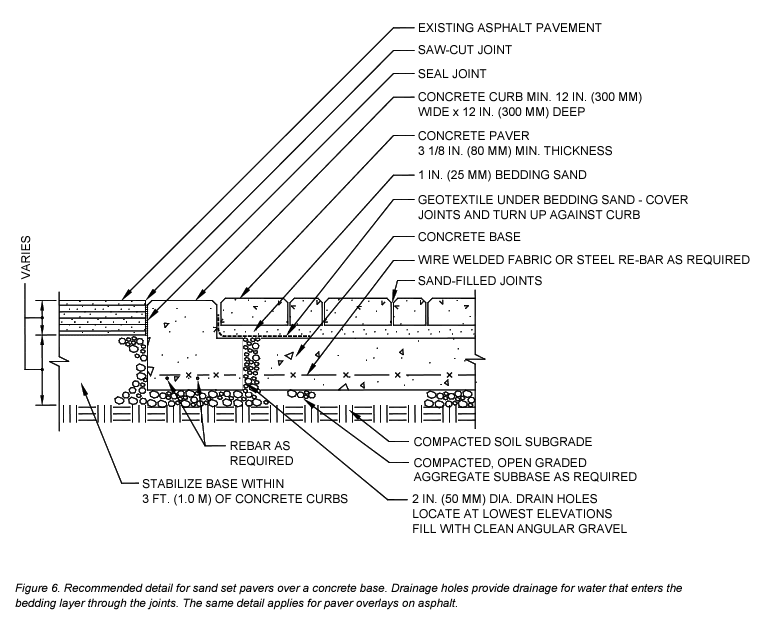
REFERENCES
Refer to the latest published ASTM and CSA standards and CMHA Tech Notes and manuals
- ASTM–American Society for Testing and Materials International, Conshocken, PA. www.astm.org
- CSA–Canadian Standards Association, Rexdale, ON. www.csagroup.org
- CMHA-Concrete Masonry and Hardscapes Association, Herndon, VA. www.MasronyandHardscapes.org
- Knapton J., “Paver Laying Course Materials – State of the Art” in Proceedings of the 2nd International Workshop on Concrete Block Paving, Oslo, Norway, pp. 246 – 264, 1994.
- BS 7533-101: Pavements constructed with clay, concrete or natural stone paving units. Code of practice for the structural design of pavements using modular paving units. British Standards Institution, London, UK, 2021
- Lilley A.A. and Dowson A.J., “Laying Course Sand for Concrete Block Paving” in Proceedings of the 3rd International Conference on Concrete Block Paving, Rome, Italy, pp. 457-462, 1988.
- Beaty A.N.S. “Laying Course Materials: Specification and Performance,” in Proceedings of the 5th International Conference on Concrete Block Paving, Tel Aviv, Israel, pp. 129-139, 1996.
- Jayawickrama, Hossain and Phillips, Evaluation of Aggregate Durability Using Micro-Deval Test, Transportation Research Board 2006 Annual Meeting, 2006.
- ICPI Bedding Sand Laboratory Testing, File no. L04-0127AT, DAVROC Testing Laboratories, ICPI Herndon, VA, USA 2004.
- Knapton J., The Nature and Classification of Bedding Sand, Proc. BIBM 1993, pp 135-141, Washington, DC, 1993.
- Bullen F. and Knapton J., “The Role of Bedding Sands in Segmental Paving Instability,” in Proceedings of the 3rd International Workshop on Concrete Block Paving,
- Cartagena, Colombia, May 10-13, 1998 pp. 36-1 to 36-4,1998.
- MTO LS – 616 Procedure for the Petrographic Analysis of Fine Aggregate, Ministry of Transportation Ontario, Downsview Ontario, Canada, 2005.
- Beaty, A., “Predicting the Performance of Bedding Sands,” in Proceedings of the 4th International Conference on Concrete Block Paving, Auckland, New Zealand, pp. 273- 284, 1992.
- Panda and Ghosh, “Structural Behavior of Concrete Block Paving—Sand in Bed and Joints,” Journal of Transportation Engineering, March 2002.