Revised March 2005
INTRODUCTION
Concrete masonry buildings offer exceptional beauty, coupled with attributes such as structural strength, durability, fire resistance, acoustic performance and low maintenance. Proper cleaning after construction and throughout the life of the building will help preserve concrete masonry’s beauty.
Although the maintenance needs of a well-designed and constructed masonry wall are minimal, contaminants can detract from an otherwise attractive structure. Cleaning of mortar smears, construction dirt and possibly efflorescence from the construction phase is usually required. Subsequent cleaning may be required over the life of the building to address dirt and soot from the atmosphere or staining from specific sources. Appropriate cleaning can remove contaminants and help produce a more uniform appearance.
This TEK discusses several general cleaning methods, applicable to whole-wall cleaning. For information on removing stains or localized contaminants, refer to Removal of Stains From Concrete Masonry, TEK 08-02A (ref. 7).
SUBSTRATES
The ease of cleaning a masonry wall can be affected by the concrete masonry units and mortar used in the wall. Cleaning products and techniques applicable to one masonry wall may not be appropriate for others. In addition, special consideration should be given to walls incorporating more than one material, such as a concrete masonry wall with clay masonry banding.
Concrete Masonry Units
Conventional, or nonarchitectural, concrete masonry units (CMUs) have a relatively smooth surface, formed from a thin layer of cement paste resulting from the typical concrete masonry manufacturing process. Aggressive cleaning methods may remove this layer, exposing aggregate and altering the final appearance. For this reason, any aggressive cleaning should be performed consistently across the entire wall surface for a uniform appearance after cleaning. In some cases, abrasive cleaning or pressure chemical cleaning are specified with smooth faced units to produce a slightly mottled “stone washed” appearance.
Ground faced units (also called honed or burnished) are polished after manufacture to achieve a smooth finish with the appearance of polished natural stone. Coatings, which are often used to deepen the color, can also help cleaning efforts by preventing dirt and other contaminants from penetrating the surface. When using ground faced units, every effort should be made to keep the units clean and free from mortar smears and droppings during construction. When required, these units can be resealed after final cleaning.
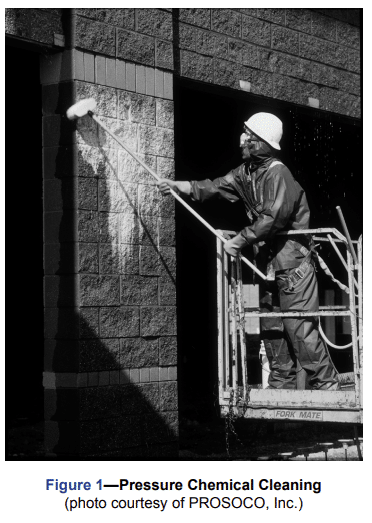
Other architectural CMU, such as split faced, split fluted and tumbled units have a natural stone-like texture produced during manufacture. The rough texture tends to hide minor soiling and makes these units more forgiving of minor efflorescence or other discolorations. This texture is also more suited to cleaning with abrasives, if that technique is required.
Glazed concrete masonry units are manufactured by bonding a permanent colored facing (typically composed of polyester resins, silica sand and various other chemicals) to a concrete masonry unit. The result is a smooth impervious surface, highly resistant to staining and easily cleaned. During construction, mortar and grout smears and droppings should be cleaned off while still easily removable, before they harden completely to the surface.
Typical Sizes and Shapes of Concrete Masonry Units, CMUTEC-001 23 (ref. 5), contains more information on the various types of concrete masonry unit finishes.
Mortar
Choosing a mortar color close to that of the concrete masonry unit makes cleaning the wall of mortar smears easier, as the mortar tends to blend in. Mortar color should be chosen to match the unit color when smooth or ground faced units are used, as they can be difficult to clean without altering the appearance. Walls with contrasting mortar and masonry unit colors may require more aggressive cleaning to remove visible mortar.
In general, the lowest-strength mortar that will meet project requirements should be specified. Higher cement content mortars with higher compressive strengths should not be assumed to have better field performance, in fact the opposite is more often true. Mortars with lower compressive strengths tend to be easier to clean off the face of the wall than are stronger mortars. Lower strength mortars also exhibit better workability, which tends to increase quality of construction. Note that building codes may restrict the use of some mortars for particular applications. More detailed information on masonry mortars is available in TEK 09-01A, Mortars for Concrete Masonry (ref. 4).
CLEANING DURING CONSTRUCTION
Many stains can be prevented or minimized through proper design, construction and maintenance procedures. Construction practices can greatly impact the amount of cleaning required for a newly constructed wall. For example, proper grouting procedures can help prevent grout blowouts and the associated clean up. Keeping the masonry as clean and dry as possible during construction can allow for less aggressive cleaning methods when construction is complete.
Cleaning exposed concrete masonry during construction encompasses such issues as the control of efflorescence and of mortar and grout droppings and smears. Detailed information on construction practices that minimize efflorescence are discussed in Control and Removal of Efflorescence, TEK 08-03A (ref. 1). The following are recommended practices for minimizing mortar and grout stains during construction (refs. 3, 6):
- Mortar squeezed out of mortar joints as units are placed should be cut off with the edge of the trowel, and care should be taken that the mortar doesn’t fall onto the wall surface or smear the surface as it falls off.
- When mortar does land on or smear the surface of the concrete masonry unit, it should be removed after initial set. Walls should be cut and brushed clean before scaffolding is raised.
- Do not cut mortar tags off until the mortar is thumbprint hard, particularly on split faced units. Similarly, joints should not be tooled until thumbprint hard.
- Mortar droppings which adhere to the exposed face of the units can be removed with a trowel or chisel after being allowed to harden. Any remaining mortar can then be removed with a stiff fiber or bristle brush.
- Excess mortar should be periodically removed from scaffolding.
- Grout spills should be immediately removed by washing and brushing.
- The base of the wall should be protected from splashing mud and mortar and grout droppings by spreading plastic sheets 3 to 4 ft (914 to 1,219 mm) on the ground adjacent to the wall and 2 to 3 ft (609 to 914 mm) up the face of the wall.
In addition to these recommendations, newly constructed masonry should be protected when adjacent construction procedures may splatter or otherwise stain the masonry. For example, plastic should be placed over masonry when concrete is poured nearby and when curing agent is sprayed.
PLANNING THE CLEANING PROCEDURE
The cleaning agent and procedure should be carefully planned, based on the type of contaminant and desired results. The cleaning method chosen should be the least aggressive that will effectively clean the wall. Before cleaning, ensure that mortar joints are cured, so the cleaning does not damage them.
Cleaning methods may alter the appearance of the finished masonry; typically, at least some cement paste is removed from the surface of the units. When this happens, more aggregate is exposed to view, which can alter the color. In general, the more aggressive the cleaning method, the more paste is removed and the greater the potential for altering the wall’s appearance. For example, sandblasting can be expected to alter the appearance to a greater degree than cleaning by hand with detergent and water. Note also that the same cleaning method may have different results based on the specific procedures used. Sandblasting at a lighter pressure will produce different results from sandblasting at a higher pressure. Again, the mildest cleaning method that will satisfy should be chosen.
The cleaning agent and procedures should first be used on a sample panel or inconspicuous location to assess: their effectiveness for the type of contaminant being removed; their effect, if any, on the finished masonry appearance; as well as the agreed upon level of cleanliness. After cleaning, the sample panel should be viewed from a distance of 20 ft (6,096 mm) under diffused lighting to evaluate the results.
Whichever cleaning method is chosen, it is important that all of the masonry be cleaned in the exact same manner (including dilution rate, brushing/scraping method, dwell time, reapplication, rinse procedure, etc.) to maintain a uniform appearance. Similarly, care should be taken to avoid overlap of areas being cleaned, as this may lead also to a nonuniform appearance.
Materials such as glass, metal, wood, architectural concrete or concrete masonry and any landscaping adjacent to the area to be cleaned should be adequately protected, since they may be damaged by contact with some stain removers or by physical cleaning methods. The level of protection and area requiring protection vary with the cleaning method, so the cleaning agent manufacturer’s recommendations should be followed.
If a surface water repellent is specified for the wall after cleaning, it should be applied as soon as conditions allow to minimize further moisture absorption or soiling.
CLEANING METHODS
The methods of cleaning concrete masonry can generally be divided into four categories: hand cleaning, water cleaning, abrasive cleaning and chemical cleaning (ref. 2). Cleaning by any method should be performed on an inconspicuous section of the building or a sample panel to ascertain its effect.
Hand Cleaning
Simple hand tools such as a trowel, chisel, stiff bristle or fiber brush, abrasive block or broken piece of masonry are first used for cleaning during construction. Steel-wire brushes should not be used because they can leave behind metal particles that may rust and stain the masonry.
Water Cleaning
Water cleaning involves scrubbing with water and detergent, water soaking, steam cleaning or pressure washing. When using water cleaning methods, the amount of water used should be limited to the least amount that will effectively clean the wall, as any water that enters the wall may promote efflorescence. See Control and Removal of Efflorescence, TEK 08-03A (ref. 1), for more detail.
Unpainted walls can usually be cleaned by scrubbing with water and a small amount of detergent. This is a nonaggressive cleaning method that generally does not alter the masonry appearance. It may not be cost-effective for large areas, however, due to the labor involved.
Clay or dirt should first be removed with a dry brush. Steel-wire brushes should not be used because any metal particles left on the masonry surface may rust and stain the masonry. Nonmetal brushes such as stiff fiber or nylon are preferred. Soaking with water causes dirt deposits to swell, loosening their grip on the underlying masonry and allowing them to be flushed away with water. Again, this method may not be appropriate if efflorescence is the primary concern.
Heated water is useful on greasy surfaces or during cold weather. However, when used with alkaline chemicals, warm water should not exceed 160° F (71° C). There is no significant advantage to using hot water with acid cleaners (ref. 2).
Pressure washing equipment can be effective for surface cleaning, and is often specified for masonry restoration work to avoid the use of harsh chemicals. Water pressure should be kept to a minimum to avoid driving water into the wall which can cause efflorescence. Note that high pressures can damage masonry or alter the final appearance. Using a consistent pressure and maintaining a set distance from the wall will produce the most uniform results. If high pressure cleaning is used, it is recommended that:
a) the pressure be limited to 400 to 600 psi (2.76 – 4.14 MPa),
b) a wide flange tip be used, never a pointed tip,
c) the tip be kept at least 12 in. (305 mm) from the masonry surface, and
d) the spray be directed at a 45o angle to the wall (never perpendicular to the wall). Pressure washing can also be used as an adjunct to scrubbing. The mild agitation created by brush application improves the overall cleaning results and enables the rinsing pressure to be kept to a minimum.
Steam cleaning has been virtually supplanted by pressure washing. However, by supplementing heat to the water, the action of loosening and softening dirt particles and grease is improved, allowing them to be more easily rinsed away. Steam is normally generated in a flash boiler and directed toward the wall using a wand at a pressure of 10 to 80 psi (69 to 552 kPa), depending on the equipment used. Although steam cleaning is less aggressive than pressure washing, it is also slower.
Chemical Cleaning
Many proprietary cleansing agents are available for concrete masonry; the concrete masonry manufacturer can be consulted for recommended compatible products. Premixed chemicals eliminate many potential problems, such as those associated with mixing reactive chemicals. They are also mixed in the proper proportions to be safely used on masonry. Strict adherence to the manufacturer’s directions is required, to protect both the user and the masonry, and to avoid any potentially harmful runoff.
When used in conjunction with water washing techniques, chemical surfectants help dissolve contaminants and allow them to be washed away during the final rinsing process. If chemical cleaning agents are used, the surfaces to be cleaned must be thoroughly prewetted with low water pressure (maximum 30 to 50 psi, 207 to 345 kPa), cleansing agents must be diluted as directed by the manufacturer and the application pressures should be kept to a minimum. After application of the cleansing agent, the wall should be thoroughly rinsed with fresh water (preferably at low pressure), or if necessary at high pressure using the precautions discussed in the Water Cleaning section.
Chemical cleaning can be a more aggressive method than pressure washing and is often more efficient and cost effective. With proper technique, the results are uniform across the wall, although the wall’s final appearance can be changed by using this method. Apply chemical cleaning solutions with low pressure spray (less than 50 psi, 345 kPa) or soft-fibered brushes.
Chemical cleaning solutions can be used to clean concrete masonry without damaging the surface; avoid using raw or undiluted acids. Even diluted acids should be used with caution, and only after thoroughly prewetting the wall, as acids dissolve the cement matrix at the masonry surface and can also damage any integral water repellent at the surface. This leaves the face more porous and exposes more aggregate, thereby changing the color and texture of the masonry. In the case of masonry with an integral water repellent, acids can also reduce the water repellency at the surface. Acids should never be applied under pressure. As a guideline, any cleaner with a pH below 4 or 5 should be considered to be acidic in nature. In addition, highly alkaline products require an acidic neutralizing afterwash as well as thorough rinsing; efflorescence can be an unwanted result if there is residual alkali.
Abrasive Cleaning
Abrasive cleaning is the most aggressive cleaning method, as the objective is not to wash away surface contaminants, but to remove the outer portion of the masonry in which the stain is deposited. For this reason, it should not be used on ground faced units, where the surface is smooth and polished. Although abrasive cleaning includes methods such as grinding wheels, sanding discs and sanding belts, it typically refers to grit blasting, also called sandblasting. Note that the use of silica sand is restricted in some areas due to its classification as an irritant, but many other blasting media are available.
Because it is a dry process, sandblasting will not promote efflorescence and can be performed in cold weather. As with pressure chemical cleaning, the cleaning method produces a consistent result across the wall with proper technique.
Care must be exercised when using abrasive cleaning techniques since overzealous applications can cause drastic changes to the appearance, durability and water tightness of the masonry. Sandblasting can alter the appearance of the masonry by roughening the surface or exposing aggregate. This is less of a concern with split faced units. In some cases, sandblasting can accelerate deterioration by increasing surface porosity. Pretesting using a sample panel is critical when sandblasting is considered.
To minimize potential damage, softer abrasives such as crushed corn husks, walnut shells or glass or plastic beads can be used. This process, sometimes called micro-peening, is slower and more costly and generally is not applicable to large scale cleaning operations.
Protective equipment and clothing must be used, including an approved respirator under a hood. Most of the dust that accompanies a dry sandblasting process can be eliminated by introducing water into the air-grit stream at the nozzle. However, the smaller particles remain a health hazard, so the same protective equipment and clothing are needed as for the dry process. The wet process requires the extra step of rinsing down the cleaned surface after blasting.
Sandblasting removes any previously applied water-resistant surface coatings, so these will need to be reapplied after abrasive cleaning.
CONCLUSION
Concrete masonry units are available in a variety of finishes, including ground faced, split faced and glazed. Contaminants from construction, such as mortar smears, and from the atmosphere after years of exposure can mar the otherwise attractive appearance of concrete masonry buildings. Cleaning methods that have been effective include hand cleaning and the use of water, chemical solutions and abrasive blasting. Some CMU manufacturers provide cleaning recommendations; in other cases, a knowledgeable professional may help determine how cleaning should best be accomplished. Field testing of cleaning materials and techniques helps ensure the desired results.
REFERENCES
- Control and Removal of Efflorescence, TEK 08-03A, Concrete Masonry & Hardscapes Association, 2003.
- Grimm, Clayford T., Cleaning Masonry – A Review of the Literature, Construction Research Center, University of Texas at Arlington, November 1988.
- Masonry Cleaning Guide. Rocky Mountain Masonry Institute, 2001.
- Mortars for Concrete Masonry, TEK 09-01A, Concrete Masonry & Hardscapes Association, 2004.
- Concrete Masonry Unit Shapes, Sizes, Properties and Specifications, CMU-TEC-001-23, Concrete Masonry & Hardscapes Association, 2023.
- Concrete Masonry Construction, TEK 03-08A, Concrete Masonry & Hardscapes Association, 2001.
- Removal of Stains From Concrete Masonry, TEK 08-02A, Concrete Masonry & Hardscapes Association, 1998.