Revised 2020
INTRODUCTION
Permeable interlocking concrete pavements (PICP) are a proven method for reducing stormwater runoff and pollutants while supporting pedestrian and vehicular traffic. Many laboratory and in-situ research projects over the past two decades by universities, government stormwater agencies, and industry have demonstrated significant runoff and pollutant reductions with cost-saving benefits. The U.S. Federal Highway Administration www.fhwa.dot.gov/pavement/concrete/pubs/hif19021.pdf has published information supporting PICP use in walkways, plazas, driveways, parking lots, alleys and streets.
Like all stormwater control measures, PICP requires maintenance as it traps sediment on its surface not unlike an air conditioning filter. Larger particles are initially trapped while allowing water to pass. Some enter the jointing stone and are trapped there. The jointing stone with larger particles eventually captures smaller particles and this decreases the infiltration rate over time. While still infiltrating water, many smaller particles are trapped within the surface and interior joints. Smaller particles are trapped and eventually decrease infiltration which results in surface ponding.
Every PICP site varies in sediment deposition onto its surface, particle size distribution, and the resulting cleaning frequency. For example, beach sand (a coarse particle size distribution) on the surface will not clog as quickly and require less effort removing than fine clay sediment. Besides the particle size distribution, the rate of surface infiltration decline also depends on the traffic, size, and slope of a contributing impervious area, adjacent vegetation and eroding soil, paver joint widths and jointing stone sizes. CMHA offers a PICP site selection tool on www.MasonryandHardscapes.org to help identify favorable sites and avoid one that may incur additional maintenance.

While routine maintenance assures long-term infiltration surface infiltration can be restored from neglected maintenance. A significant advantage of PICP is its ability to remove settled or wheel-packed sediment in the joints. This Tech Note provides guidance on routine and restorative maintenance practices that support surface infiltration. This bulletin also provides guidance on maintaining the surface as an acceptable pedestrian and vehicular surface.
PRACTICES SUPPORTING SURFACE INFILTRATION
PICP design and construction that complies with CMHA guidelines are fundamental to long-term surface infiltration. Guidelines are found in ASCE 68-18 standard on PICP, the CMHA manual, Permeable Interlocking Concrete Pavements and in CMHA Tech Note PAV-TEC-018–Construction of Permeable Interlocking Concrete Pavements available on www. MasonryandHardscapes.org. Some essential characteristics described below support continued infiltration.
PICP doesn’t use sand. Unlike interlocking concrete pavements, sand jointing or bedding materials to support paving units and dense-graded aggregate bases are not used in PICP. Sand joints and bedding allow very little water to enter and often eventually clog for traffic borne detritus and sediment.
Construction E & S control is essential. Erosion and sediment control during construction is covered in the previously mentioned documents, and is customized to each project via the Stormwater Pollution Prevention Plan or SWPPP. An inspection checklist is provided at the end of this bulletin that includes sediment control. If the PICP is built first and construction traffic must use it, then it will very likely require vacuum cleaning upon construction completion. The ideal situation is PICP constructed late in the project such that it will not receive much construction traffic and sediment. This may require using temporary construction roads.
If PICP receives run-on from upslope pervious or impervious areas, inspect these areas for erosion and sediment, yard waste, materials storage, etc. Sweep or vacuum the contributing drainage area clean and free of any dirt, leaves and mulch as they are a major source of PICP clogging. Lawn and planting beds should be sloped away from PICP areas.
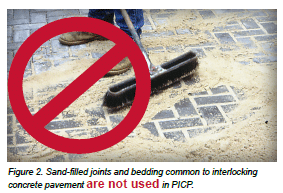
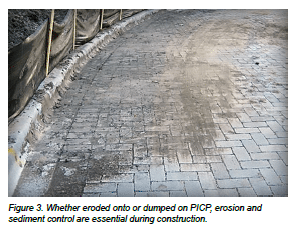
Maintain filled joints with stones. The jointing stones capture sediment at the surface so it can easily be removed. If sediment is allowed to settle and consolidate, then cleaning becomes more difficult since the sediment is inside the joint rather than on the surface. Settlement of jointing stones in the first few months is normal to PICP as open-graded aggregates for jointing and bedding choke into the larger base aggregates beneath and stabilize. This settlement often requires the joints to be refilled with aggregates three to six months after their initial installation. If possible, this should be included in the initial construction contract specifications. Aggregate-filled joints facilitate sediment removal at the surface and provide interlock for pavement structural stability.
Keeping the joints filled during the PICP service life is essential to trapping sediment and facilitating its removal at the surface and ensuring long term performance. Permeable segmental paving systems that do not use jointing aggregates may incur higher maintenance time and costs to extract accumulated sediment from deep within the joints and bedding, or eventually move through the base/subbase aggregates onto the subgrade and reduce its infiltration.
Filled paver joints means filled to the bottom of the paver chamfers with jointing stone. If the pavers have very small or no chamfers, then they should be filled within ¼ in. (6 mm) of the paver surface. Should the top of jointing stone settle below ¼ in. (6 mm), vacuum equipment can be less effective in removing sediment and cleaning becomes potentially more expensive.
Manage mulch, topsoil and winter sand. Finally, stockpiling mulch or topsoil on tarps or on other surfaces during site maintenance activities rather than directly on the PICP surface helps maintain infiltration. Figure 5 illustrates an example of correct management of landscaping material on PICP, as well as the need to exposed soil slopes.
Sand used in the winter for traction is not recommended. Figure 6 illustrates the consequence to PICP joints when subjected to winter sand for traction. If used, sand should be removed with vacuuming in the spring to prevent a substantial decrease in surface infiltration. Using jointing aggregate is recommended as a better alternative to using sand for winter traction. In addition, the aggregate can provide some refilling of the joints.
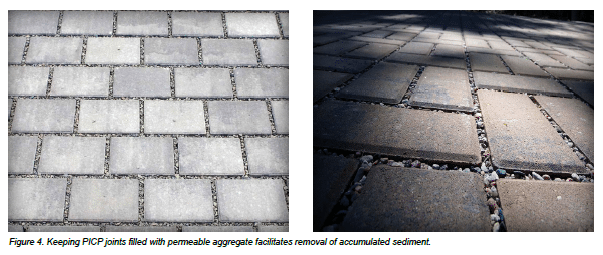
SURFACE INFILTRATION INSPECTION & TESTING
Visual Inspection—Effective ways to assess PICP surface infiltration is by conducting visual inspections or tests on the surface before, during and immediately after rainfall.
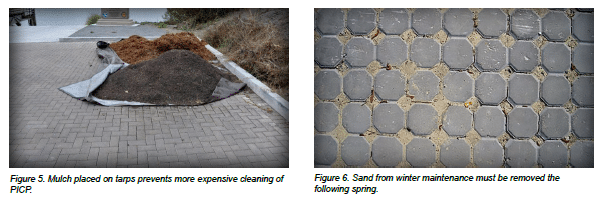
Inspect Before a Rainfall—Sediment crusted in the joints when dry is the most opportune time to remove it. During dry periods, the sediment layer in each joint can sometimes dry out and curl upward. This layer can be easily loosened by vacuum equipment.
Additionally, deciduous leaves and pine needles eventually get crushed by traffic, degrade, and work their way into the joints, thereby reducing infiltration. See Figures 7 and 8. The site should be inspected for sediments from adjacent eroding areas and those areas stabilized immediately.
Weeds growing from within joints indicate accumulated sediment in the joints and neglected maintenance. See Figure 9. Weeds will not germinate unless there is accumulated sediment. Weeds should be removed by hand. Herbicide may kill weeds, but dead vegetation and roots will remain. They typically reduce infiltration and should eventually be removed.
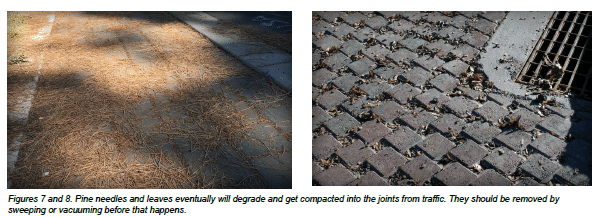
Inspect During and Just After a Rainstorm— The extent of puddles and bird baths observed during and especially after rainstorm indicate a need for surface cleaning. A minor amount of ponding is likely to occur particularly at transitions from impervious pavement surfaces to PICP. This often occurs first as sediment is transported by runoff and vehicles. See Figures 10 and 11. Should ponding areas occupy more than 20% of the entire PICP surface, then surface cleaning should be conducted. While a rainstorm’s exact conclusion is difficult to predict, standing water on PICP for more than 15 minutes during or after a rainstorm likely indicates a location approaching clogging.
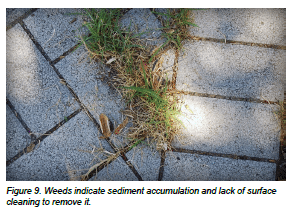
Test Surface Infiltration—A quick and subjective test for the amount of surface infiltration is pouring water on PICP. If the water spreads rather than infiltrates, the extent of spreading suggests an area that may be clogging. Should more than approximately 20% of the surface area see ponding during or immediately after a rainstorm, a more objective measure of surface infiltration of these areas can be accomplished using ASTM C1781 Standard Test Method for Surface Infiltration Rate of Permeable Unit Pavement Systems. Figure 12 illustrates the test set up using a 12 in. (300 mm) diameter ring set on plumber’s putty. (The ring can be metal or plastic.) Figure 13 illustrates the test apparatus in place with water poured into it.
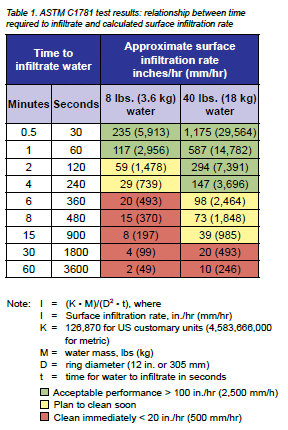
ASTM C1781 test method begins with “pre-wetting” an area inside the ring to ensure the surface and materials beneath are wet. This is done by slowing pouring 8 lbs (3.6 kg) of water while not allowing the head of water on the paver surface to exceed 3/8 in. (10 mm) depth. If the time to infiltrate 8 lbs of water is less than 30 seconds (using a stopwatch typically on a cell phone), the subsequent test is done using 40 lbs (18 kg) of water. If more than 30 seconds, then 8 lbs of water is used in the subsequent tests. Again, a 3/8 in. (10 mm) head is maintained during the pour while being timed with a stopwatch. The surface infiltration rate is calculated using formulas in the test method.
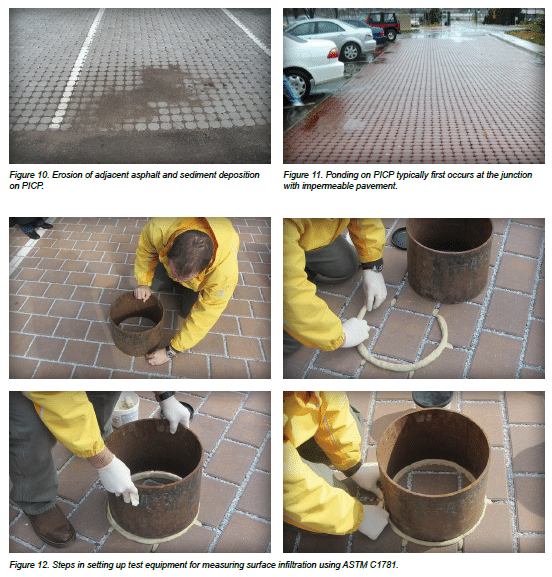
If infiltration measurements on ponded areas consistently result in rates below 20 in./hour (508 mm/hr), they require immediate surface cleaning. PICP surfaces sloped over 2% with less than 40 in./hr infiltrate rate require immediate surface cleaning. An infiltration rate of 20 in./hr equates to 30 minutes’ infiltration time and 40 in./hr results in 15 minutes. Table 1 further illustrates the relationship between time for 40 lbs (18 kg) of water to infiltrate and the calculated infiltration rate. CMHA offers a downloadable calculator for converting time of infiltration to infiltration rates when using C1781. See www.MasonryandHardscapes.org.
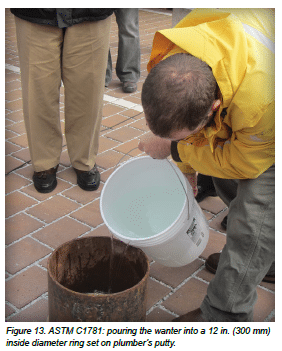
SURFACE INFILTRATION MAINTENANCE TYPES
Routine and Restorative Maintenance—There are two approaches or service types for maintaining PICP surface infiltration: routine and restorative. Routine maintenance is done regularly to maintain infiltration. It removes most loose sediment and debris from the surface before being trapped and stuck in the jointing aggregates thereby causing clogging. Routine maintenance may require reinstatement of a small amount of jointing stones or none at all.
ROUTINE MAINTENANCE EQUIPMENT OPTIONS FOR MAINTAINING VARIOUS SIZED PICP APPLICATIONS
Cleaning Small Pedestrian Areas and Driveway—These are typically under 2,000 sf or 200 m2 and include patios, plazas, sidewalks, and driveways. Equipment options follow:
Hand-held Bristle Broom— Sweep as needed to clear the surface clear of loose debris. See Figure 14.
Leaf Blower (electric or gas powered)—A minimum air speed of 120 mph (190 kph) is recommended. Jointing aggregates remain in place while removing loose debris such as leaves from the surface. See Figure 15.
Rotary Brush with Plastic Bristles—These are often used to spread jointing stone during construction. Same equipment can be used to clean surface to top of joints. Bristles can flip debris out of joints (depends on bristle reach into the joints). A small amount of aggregate may need to be replaced in the joints after using. See Figure 16.
Wet/Dry Shop Vacuum or Walk-behind Vacuum—Use equipment with a minimum 4 (peak) HP motor with minimum 130 cubic feet (3.7 m3) per minute suction. These machines can remove some jointing aggregates so they may require replenishment. See Figures 17 and 18.
Power Washer—This equipment should be capable of 1,400 to 1,800 psi (9.6 to 12.4 MPa) pressure. Apply the spray at a 30° angle approximately 18 to 24 in. (45 to 60 cm) from the surface and adjust as needed. This equipment will evacuate jointing aggregate and replenishment will be required. Power washing alone generally is not an optimal cleaning approach because there is almost no opportunity on most sites to remove the water-suspended sediment before the water is absorbed back into the pavement. See Figure 19.
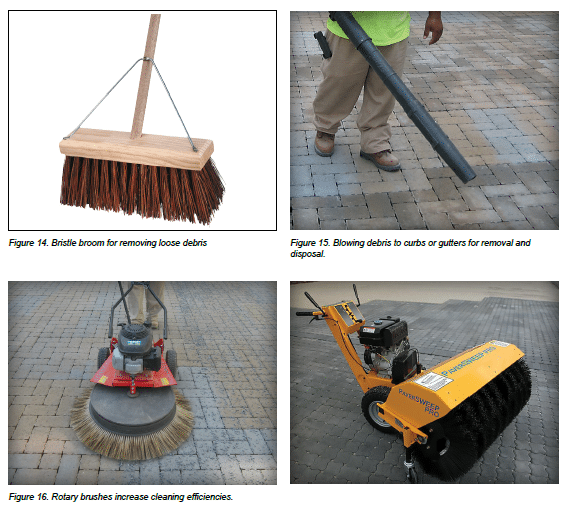
CLEANING LARGE PICP AREAS
These are typically over 2,000 sf or 200 m2 such as large plazas, long sidewalks and driveways, parking lots, alleys and streets. Equipment options follow:
Street Sweepers—These typically have rotating plastic bristle brushes positioned near the curb side and center pickup into a hopper at the rear. Do not use water as it slows removal of loose dirt into the machine. This machine does provide a small vacuum force to manage dust, but the cleaning action is provided by the mechanical sweeping, so it is moderately effective among large machines for removing sediment in the joints. Bristles from the the main broom can reach into joints parallel to the direction of the broom rotation, but have little effect on the joints not aligned with the broom rotation. See Figure 20.
Regenerative Air Sweepers—Includes a box positioned under the truck and on the pavement through which air is blown and recirculated (hence the term regenerative air). The pavement must have no convex (or reverse) crown in order to create an adequate seal for suction in the box. Air pressure flowing through it picks up loose debris and sediment. Rotating brushes can be used to direct dirt and debris toward the box. See Figure 21.
RESTORATIVE INFILTRATION MAINTENANCE FOR LARGE CLOGGED SURFACES
Restorative maintenance is conducted when sediment has lodged in the jointing stones from traffic and weather. The condition indicates that the PICP surfaces have not been regularly cleaned. Restorative maintenance requires some or complete removal of the jointing aggregates to increase infiltration. The depth of jointing stone removed depends on the penetration depth of the sediment into the joints. This can be determined on a sample of a few clogged joints (typically where ponding occurred) by prying out stones and sediment with a flat head screwdriver until little or no accumulated sediment appears.
True Vacuum Sweepers—These can withdraw jointing material and even the concrete pavers. Therefore, the vacuum engine revolutions must be adjusted by the machine operator during a few test runs to find the setting that withdraws the needed depth of sediment and jointing aggregate. After withdrawal, jointing aggregates will require replenishment. The suction orifice is typically about a yard (meter) wide and positioned on the curb side of the truck. Extremely clogged surfaces will require two or more passes. Figure 22 shows this machine. It is often used by municipalities to clean out storm drain catch basins and may require a separate vacuum attachment to clean pavements.
High-power Washing and Vacuum Equipment—Figure 23 shows the equipment for restorative cleaning where water is applied to help loosen sediment and stones in the joints. Figure 23 shows a vacuum that withdraws sediment and stones immediately after applying water. The water and debris are drawn into a vac truck.
High Pressure Air/Vacuum—High pressure air is blasted into the joints and has been shown to be very effective at dislodging sediment and debris. A second step is then required to vacuum up the debris that is dislodged. In Figure 24, the machine in the foreground blows debris completely out of the joints and the second machine takes up the debris into a vac truck similar to that used to clean catch basins. See Figure 24. As with all restorative cleaning methods, clean jointing stone is spread and the empty joints are filled. After removing excess stones from the surface, the pavers with filled joints are compacted with a minimum 5,000 lbf (22 kN) vibratory plate compactor operating at 75-90 Hz. See Figure 25. This helps settle the stones into the joints. Any joints were stones have settled should be filled with more stones within a 1/4 inch (5 mm) of the paver surfaces.
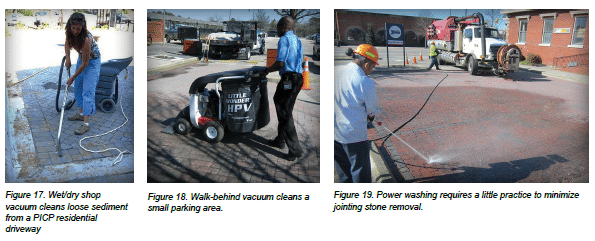
MAINTENANCE EQUIPMENT PERFORMANCE
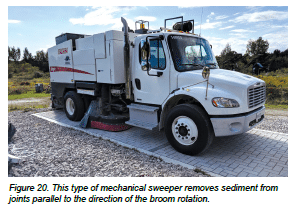
In 2020, the University of Toronto completed a two year research project, Maintenance Equipment Testing on Accelerated Clogged Permeable Interlocking Concrete Pavements. This study evaluated maintenance equipment for restoration of infiltration rates of PICP systems when joints become severely clogged. The research was conducted at the Toronto & Region Conservation Authority’s Kortright Centre in Vaughn, Ontario. The research scope of work included the construction of seven 10 ft. by 10 ft. PICP partial infiltration test pads. The cells were carefully clogged to a surface infiltration rate of ≤ 10 in/hr. The sediment infill used to clog the system was regional street cleaning sediments with a known particle size distribution. Five different technologies were investigated: full vacuum sweeper, regenerative air sweeper, dry mechanical sweeper, water pressure washing, and a hybrid high pressure air/vac system specifically designed for permeable pavement. The objective of the study was to evaluate the effectiveness of each method at restoring surface infiltration rates. The impact of cohesive soil sediment was also evaluated as part of the study. All cleaning technologies significantly improve surface infiltration rates. However, the high pressure air-vac hybrid had the best and least variable results, and was the only technique able to fully restore surface infiltration rates. Joint penetration depth was generally a good indicator of restoration effectiveness, except if sediment gradation varies. A complete copy of the report can be found at https://tinyurl.com/y67zhydz.
Also in 2020 the United States Geological Survey Madison, WI office published results of a four year investigation on cleaning PICP, Assessment of Restorative Maintenance Practices on the Infiltration Capacity of Permeable Pavement Assessment of Restorative Maintenance Practices on the Infiltration Capacity of Permeable Pavement. Since 2014, this research site has collected water quality, temperature, infiltration rates, and surface flow data with three types of permeable pavement sections (pervious asphalt, porous concrete, and permeable interlocking concrete pavement). Contributory drainage from an adjacent parking lot provided an opportunity for accelerate clogging and collect data for 9:1 and 5:1 drainage ratios. The following six pavement cleaning methods were evaluated over a 4-year period: manual cleaning with a masonry trowel; Leaf blower and broom; true vacuum; water-enhanced vacuum; high pressure air system; and pressure washer with soil vacuum. An evaluation of the efficiency of each method was based on comparing surface infiltration rates, pre and post cleaning
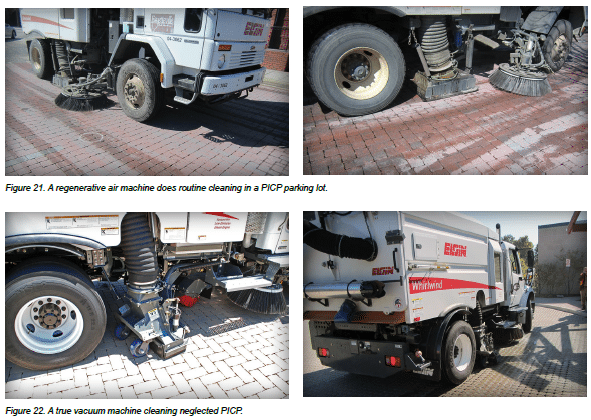
Surface variability was high due to surface flow patterns across the permeable surfaces. All cleaning methods improved surface infiltration rates. PICP showed the greatest recovery compared to pervious concrete or pervious asphalt. These systems were more difficult to maintain due to sedimentation penetrating into the solid matrix related to the twisting of interconnected pores created during placement. Different cleaning methods produce different results however, in all instances, when the same method was applied, PICP showed the greatest recovery in infiltration capacity. At this particular site the majority of clogging occurred within the top 1 inch. A complete copy of the report can be found at https://tinyurl.com/yy9nhou8.
INSPECTION INTERVALS AND PROCEDURES FOR MAINTAINING SURFACE INFILTRATION
Routine maintenance provides the best infiltration performance by implementing the following procedures:
- Weekly—Prevent contamination from routine landscape maintenance such as grass clippings from mowing, hedge trimming, mulching plant beds, etc. by:
- Broom sweep debris from the paver surface, or
- Blow debris from the paver surface with a powered leaf blower onto other surfaces that will not re-transmit it to the PICP surface.
- Mechanically sweep paver surface.
- Remove loose debris, leaves, needles, sediment, topsoil, mulch, etc. after severe rain storms using the above procedures.
- Collect and dispose of debris.
- Semi-annually—Remove loose surface debris from the pavers and jointing stones (1) when trees have defoliated in the fall and (2) at the end of winter snowfall.
- Use a wet/dry vacuum for small areas and a regenerative air machine for larger areas.
- Replenish jointing stone as needed to the bottom of the paver chamfers.
- Check any observation wells and outlet pipes from underdrains to confirm drain down and water outflows.
- As needed—Based on observation and during rainstorms and subsequent surface infiltration tests, remove and replenish the jointing stones and sediment using restorative cleaning equipment and procedures.
Note: Various factors will affect each project’s routine maintenance schedule and each must be reviewed individually.
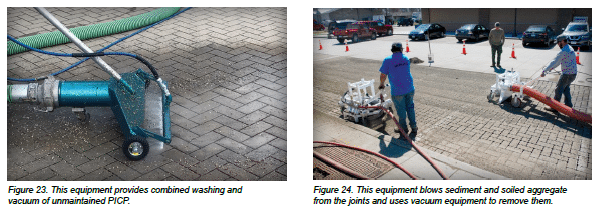
WINTER MAINTENANCE
Snow Removal—Unlike other permeable pavement surfaces, PICP demonstrates durability in the winter. PICP can be plowed with steel or hard rubber blades. Steel blades typically scratch all pavement surfaces. When using commercial snow removal companies, confirm in writing they provide protective edges on the snowplow equipment to avoid scratching the surface. Most pavers have chamfers on their surface edges which can help protect the edges from chipping by snow plows. For smaller areas, use a plastic snow shovel and fit snow blowers with plastic on the scoops and on the gliders. When possible deposit plowed snow onto grassy areas and not on the PICP when the plowed snow is dirty. Such dirt will remain and likely help clog the PICP surface after the snow melts.
Deicers—When used sparingly, deicers should not damage PICP surfaces as the brine typically forms on the surface to lower the freezing temperature of water and eventually moves into the joints with melting ice or snow. Some deicers will accelerate surface wear on some styles of pavers with blasted or hammered surfaces.
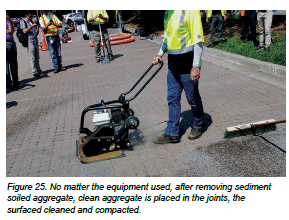
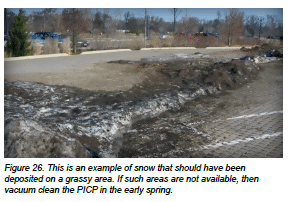
A 2020 University of Toronto study on pavement deicing operations quantified some significant winter safety benefits when using PICP. Besides confirming that the use of permeable pavers can eliminate the occurrence of snow melt refreezing and forming black ice, snow and ice can also melt and dry quicker when deicers are used on PICP. More importantly, the research confirmed that a much lower deicing salt application rate is required on PICP compared to impervious asphalt, while still maintaining a high level of slip and skid resistance. The study also demonstrated that PICP systems can attenuate and buffer the release of salt back into the environment, an important finding since there is concern about snowmelt and stormwater runoff environmentally damaging lakes and rivers.
Deicer types acceptable for use in on PICP surfaces include sodium chloride, calcium chloride and potassium chloride. Do not use magnesium chloride as it will eventually destroy all concrete materials. Anti-icing agents that contain ammonium nitrate and ammonium sulfate should not be used since they can also erode concrete. Always read and follow the manufacturer’s recommendations for use and heed all warnings and cautions.
MAINTENANCE FOR OTHER DISTRESSES
Over time and traffic, PICP can exhibit other distresses besides surface ponding from clogged joints. These are outlined in Table 2 and remedies are provided.
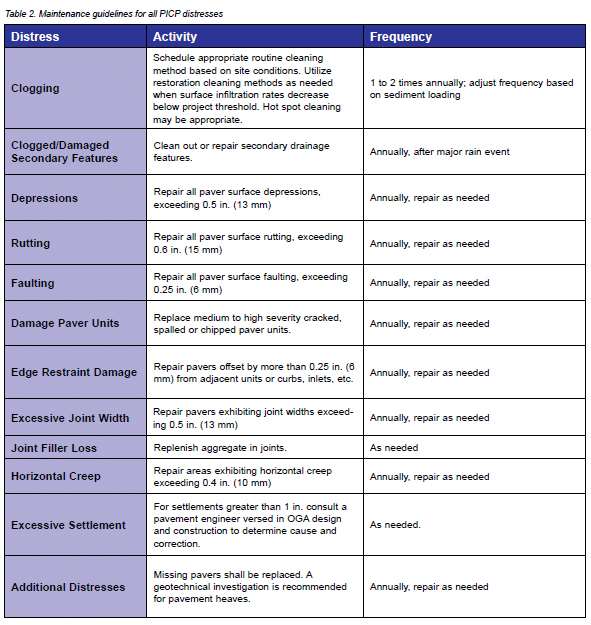
UTILITY RESTORATION GUIDELINES
- Remove and store pavers for reuse. Secure undisturbed pavers in opening with wood or metal frame.
- Remove and dispose of all jointing and bedding aggregate as they typically cannot be re-used.
- Remove the aggregate base and subbase material. Incidental mixing of base and subbase aggregates is acceptable, but make every effort to separate them. Store in on impermeable pavement or a geotextile to prevent contamination. Do not reuse contaminated aggregate.
- Re-compact subgrade material as required for stability during utility repairs.
- Repair or install utility as required.
- If below the bottom of the subbase, place and compact dense-graded road base in lifts not exceeding 6 in. (150 mm) and compact to 100 percent of standard Proctor maximum dry density. The top of the dense-graded aggregate should be at the same elevation as the bottom of the open-graded subbase aggregate. Alternately flowable fill could be used to reestablish the subgrade surface.
- Reinstate and compact the subbase aggregate in minimum 6 in. (150 mm) lifts. Use a minimum 13,500 (65 kN) plate compactor with a compaction indicator. Add new subbase aggregate if needed.
- Reinstate and compact the base aggregate as one 4 in. (100 mm) lift. Use a minimum 13,500 lbf (65 kN) plate compactor with a compaction indicator. A lightweight deflectomer (LWD) can be used to ensure that deflections of the compacted base aggregate are below an average of 0.5 mm (assuming a minimum 12 in. (300 mm)) compacted aggregate subbase. An LWD should be used according to ASTM E2835
- Place and screed new bedding aggregate in a consistent thickness layer between 1.5 and 2 in. (38 and 50 mm).
- Reinstate pavers with at surface at least 1 in. (25 mm) higher than the final elevation. Compact the pavers in two perpendicular directions with a minimum 5,000 lbf (22 kN) plate compactor. Fill joints with aggregate, sweep away excess, and compact the pavers in two perpendicular directions again. Compact pavers so they are level with surrounding pavers.
- Sweep surface clean and remove any excess aggregate and debris.
Other recommendations include keeping all removed materials clean and free of sediment and debris. Minimize excess debris from construction activities and equipment entering the permeable surface. Store all materials away from the permeable surface, otherwise separate materials from the permeable surface with geotextile. Pavement cuts located parallel and close to the wheel path should be extended to include the wheel path. Cuts located within 3 ft (1 m) of a curb or construction joint should include the removal of the adjacent base and subbase to the edge of the curb or construction joint.
REFERENCES
- Drake, et al. (2020), “De-icing Operations for Permeable Interlocking Concrete Pavements”, University of Toronto, Dept. of Civil and Mineral Engineering
- Danz, et al. (2020), “Assessment of Restorative Maintenance Practices on the Infiltration Capacity of Permeable Pavement”, U.S. Geological Survey, Middleton, WI