Revised 2024
Bitumen-sand set applications on a rigid concrete base have a proven track record of superior performance. Such applications include crosswalks, plazas, parking lots, roadways, intersections, etc. many subject to concentrated truck traffic. The performance of these pavements that experience higher loading can benefit from this method of installation and justify its higher construction cost. This type of rigid pavement construction has replaced mortar or sand-cement bedding materials in many pedestrian applications and in all vehicular ones. Mortar set pavers have not performed well under vehicular traffic and are not recommended. In addition, mortar-set pavers should not be used in pedestrian applications exposed to freeze-thaw and deicing salts. Mortar tends to deteriorate in such environments.
Bitumen-sand set applications emerged some thirty years ago from the defunct Hastings Brick Company in New York. This setting technique was used as a means to differentiate the Hastings clay brick paving system to win project specifications. Over the years, bitumen-sand set paving specifications moved into concrete paver project specifications and have seen many derivations in architectural specifications. This Tech Note provides current and proven installation techniques.
Typical Cross Section—Pavers installed on a bitumen sand set base follow the same guidelines as a sand set application. A maximum 3:1 aspect ratio (length/thickness) and a minimum 31/8 in. (80 mm) thickness for vehicular applications. Residential driveways and pedestrian applications could use a minimum 23/8 in. (60 mm) thick units with a maximum 4:1 aspect ratio) Both applications sit on a minimum 3/4 in. (20 mm) thick bitumen-sand setting bed for particles up to 1/4 in. (6 mm). If the maximum particle size is 3/8 in. (9 mm) then the bitumen-sand setting bed should be increased to 11/8 in. (28 mm) or 3 times the largest particle size.
Neoprene-modified asphalt adhesive is often applied to the surface of the thin setting bed and bonds the pavers to it. The setting bed rests on a thin layer of emulsified asphalt spread over a concrete base, which is generally referred to as an asphalt tack coat or tack coat. The tack coat provides additional adhesion of the bitumen-sand bedding to the concrete. Figure 1 shows a typical crosswalk section.
The tack coat enhances the bond of the setting bed to the underlying base. For residential and pedestrian applications with no vehicular traffic, the tack coat may be omitted. Typical highway tack coat materials can be used, including diluted asphalt emulsions. The type of tack coat will be based upon the environmental conditions and the procedure used by the installer. Emulsified asphalt should comply with ASTM D977, such as Type SS-1 or SS-1h.
In most cases, the tack coat material will be supplied in pails or drums. They should be stored in accordance with the manufacturer’s directions and be thoroughly mixed before application.
The concrete base is designed to support anticipated traffic. Unlike interlocking concrete pavers on a flexible aggregate base, those on concrete bases are typically given little or no credit for their structural contribution to the pavement cross section. The concrete base distributes wheel loads to a subbase and the soil subgrade. For bituminous-sand set applications, concrete bases are recommended in vehicular and pedestrian areas. Asphalt bases should only be used in pedestrian areas.
The bituminous setting bed is a mixture of asphalt cement and coarse sand (or fine aggregate). In most cases the maximum particle size should be less than 1/4 in. (6 mm). The mix detailed here may not be available from all hot mix asphalt plants and a suitable alternate will have to be selected. In these areas, it may be necessary to select a sand-aggregate mixture with a maximum particle size of 3/8 in. (9 mm). If a coarser topping mix is used the surface must be compacted tight to promote adhesion of the pavers.
Hot-mix plants typically use one or two different grades of asphalt cement to suit local highway construction requirements. When available, AC 20 or AR-8000 viscosity graded asphalt cements complying with ASTM D3381 can be used. These materials have a long record of success, but are gradually being replaced with performance grade, PG 58-22, binders complying with ASTM D6373 that provide similar characterisitcs.
Although this grade of asphalt cement is used throughout the United States and Canada, other grades are available to meet local design temperatures and traffic characteristics. Areas with colder climates may use grade PG 58-28 asphalt cement, and those with hotter climates may use grade PG 70-16 asphalt cement.
Fine aggregate materials available at hot mix plants are typically natural or manufactured sands. Fine aggregates should comply with ASTM D1073. When identifying an acceptable source for the bituminous-sand bedding material, refer to local department of transportation specifications for the materials they use as the surface layer on asphalt roads.
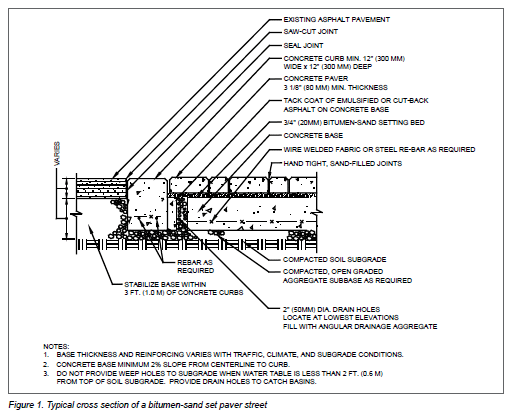
The sand should meet the gradation requirements of ASTM C33 or CSA A23.1-FA1 and consist of clean, hard, durable particles free from adherent coatings of clay, organic matter and salts. In some areas it may be difficult to find an asphalt producer that provides a product that meets the recommended sand gradation. In these areas it may be necessary to use a mix design that has particles up to 3/8 in. (9 mm) as identified in ASTM D1073. This coarser material will have a more textured surface. The aggregate should have a verifiable history of being resistant to stripping. Manufactured sands typically have a higher stability than natural sands.
The bituminous setting bed material should be mixed at a hot- mix asphalt plant. The dried aggregates and asphalt cement are heated to the appropriate temperatures and are mixed thoroughly. This will produce a uniform mixture with all of the aggregate particles evenly coated with asphalt cement. The supplier should determine the exact proportions to achieve the best mix to suit the materials, the site and the installation conditions. Typical mix proportions are approximately 6 to 8 percent asphalt cement by weight.
In vehicular applications the pavers are bonded to the bituminous setting bed using an neoprene modified asphalt adhesive. Typical proprietary materials contain 75 percent solids in a mineral spirit solvent. The solids consist of 2 percent neoprene, 10 percent asbestos free fibers and 88 percent asphalt. The adhesive is typically supplied in pails or drums. The material should be stored in accordance with the manufacturer’s recommendations and be thoroughly mixed before application. In pedestrian applications the adhesive can be omitted to help simplify future repair procedures.
The concrete pavers selected for vehicular applications should comply with the requirements of ASTM C936 or CSA A231.2 with the additional requirement that the thickness tolerances be +/- 1/16 in. (1.6 mm). Some manufacturers may need to gauge or grind the units to achieve this tolerance.
The joint sand should meet the gradation requirement of ASTM C33 or ASTM C144 or CSA A23.1-FA1 or CSA A179.
Edge restraints must be installed around the entire perimeter of the interlocking concrete paving unit area following the guidelines of CMHA Tech Note PAV-TEC-003. Concrete edge restraints should be used for vehicular applications. Metal or plastic edge restraints can be used for pedestrian and non- vehicular applications only (including when metal or plastic edge restraints are mechanically connected to concrete or asphalt base using fasteners such as ramsets, expansion bolts, steel stakes, etc.).
Pavers in bitumen-sand set applications will settle only slightly when compacted as the thin bitumen-sand bedding material is already compacted while hot. Pavers are set a few millimeters above the curb edge before compaction so that they sit just above or level with the curb after compaction. Pavers should be set higher if some settlement of the concrete base is expected, relative to the curb, due to traffic, soil settlement or both.
As with all overlays on concrete, attention should be given to draining water from the setting bed horizontally through edge restraints and catch basins, and vertically through the base. Figure 1 shows a 2 in. (50 mm) diameter drain hole pre-formed in the concrete base filled with open-graded, free-draining angular gravel. Holes are typically placed every 10 ft (3 m) along the perimeter and at the lowest elevations. While the amount of water that weeps through the bedding material is minimal, drain holes help assure its removal. Grading of the concrete base should direct water to the weep holes and prevent it from being trapped. If water remains on the bedding layer, the water can freeze and loosen the pavers from expansion. Care should be taken during construction to prevent clogging of the drain holes with bitumen-sand setting bed material.
CONSTRUCTION SEQUENCE
Figures 2 through 12 demonstrate the bitumen-sand set interlocking concrete pavement installation sequence for a crosswalk. Once the concrete base is in place and cured for at least 24 hours, a tack coat of emulsified asphalt is applied on the concrete base (Figure 2). For maximum adhesion it is important to create a thin layer of uniform thickness. To achieve this it is best to dilute the asphalt emulsion with water at a ratio of 1:1. Estimated application rates are listed in Table 1.
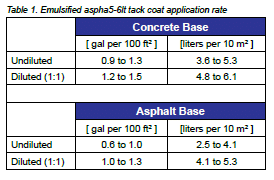
Best application results are typically achieved using a synthetic paint roller with a short nap. Once applied the tack coat should not be disturbed and should be allowed to cure before covering with the setting bed material. As the asphalt emulsion cures it should turn from a brown to black color (Figure 3). This may take a few hours depending on weather conditions. When using SS-1 and SS-1h asphalt emulsions the temperature should be between 70 and 160° F (20 to 70° C) to allow for proper curing. Asphalt tack coats are recommended for vehicular applications. They are typically not required in pedestrian applications.
The hot bitumen-sand bedding layer is placed, screeded to about 3/4 in. (20 mm) thick and compacted while remaining above 250° F (120° C) (Figures 4 and 5). This layer typically compacts about 1/8 in. (3 mm). The depth of this layer must be consistent. If the area does not have a curb to support a screed, screed bars are placed directly on the concrete base to guide the screed. The bars are removed immediately after screeding and the narrow void spaces left from the removed bars are filled with additional, hot bitumen-sand mix and troweled smooth. The compacted bitumen-sand bedding layer can compensate for only very small surface variations in the concrete
base cannot be used to make up for a rough surface finish on the concrete. The bitumen-sand mix is placed, screeded and compacted in one small area at a time (typically a 100 to 300 sq. ft. or 10 to 30 m2) in order to screed and compact the mix while hot. Areas that can not be compacted with the roller compactor should be compacted with a hand tamper (Figure 6). Before spreading the asphalt adhesive it is advisable to confirm the bedding elevation using a paver (Figure 7). If it cools prior to compaction, it is impossible to compact and will require reheating prior to compaction.
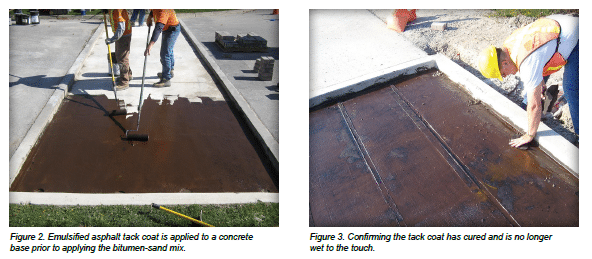
A thin layer of neoprene-asphalt adhesive is then applied with a squeegee to the top of the bedding layer, and allowed to cure (typically 1 to 2 hours). Adhesives with a high viscosity are applied with a straight edged towel as shown in Figure 8. Adhesives with a low viscosity can be applied with a squeegee. The adhesive takes a hazy appearance when ready to mark baselines and place the concrete pavers (Figure 9). Only enough adhesive should be applied that will be covered with pavers in a day’s work. Figure 10 shows the paver installation. Once the pavers are placed on the adhesive, they are very difficult to remove. If removed, they can pull up the adhesive and bitumen-sand bedding under the paver. Once all the pavers are in place including cut units, sand is swept into the joints and pavers are compacted until the joints are full (Figures 11 and 12). For more efficient work, sand sweeping and compaction can be simultaneous. Unlike sand-set pavers, there is no need to compact the pavers without sand in the joints first. When completed, the pavement can accept traffic loading immediately (Figure 13).
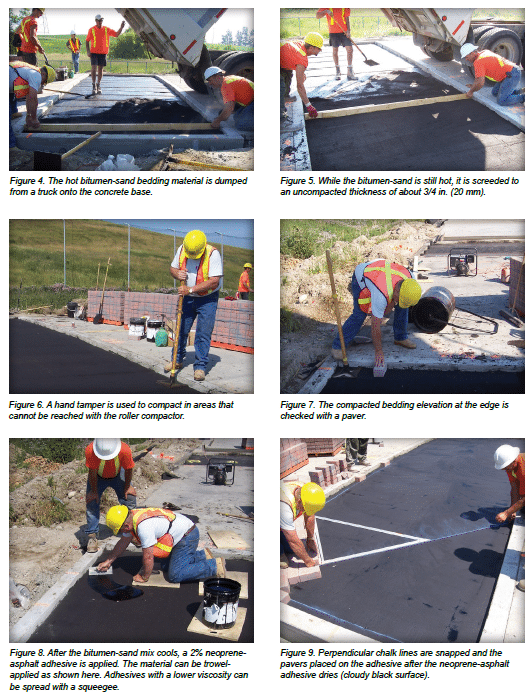
Should the surface of the pavers be stained with adhesive during installation, it is very difficult to remove and fresh replacement pavers are required. In-service reinstatement of installed bitumen-sand set pavers is practically impossible because the bitumen-sand material adheres to the bottom of the pavers when removed. It is less expensive to discard the pavers rather than remove the asphalt from the units and attempt to reinstate them.
Specialty Tools—Some specialty tools are required to successfully install bitumen-sand set pavers. For example, Figure 14 shows a roller modified with a long handle welded or bolted to the frame. The drum of the roller should be smooth with no rust, preferably with sharp edges (not rounded). Other specialty tools are shown in Figures 15, 16 and 17.
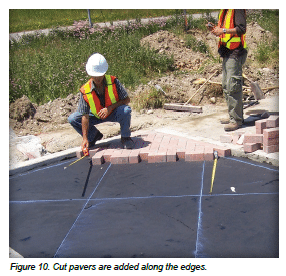
Cost and Performance—Bitumen-sand set pavers are significantly more expensive (typically 20-30% higher) than sand-set pavers over a concrete base due to additional material and labor costs. However, the additional costs incurred with bitumen-sand set concrete pavers for vehicular traffic are often balanced with the long-term performance characteristics when compared to sand-set installations under the same wheel loads. As noted in Tech Note PAV-TEC-019, interlocking concrete pavement crosswalks with bituminous-sand setting beds on concrete bases were estimated to have a life span of 7.5 million ESALs.
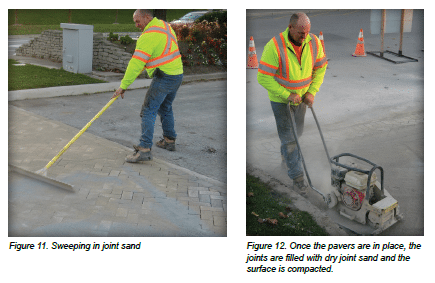
Slab Applications—Bitumen-sand set applications are sometimes used in public pedestrian areas with concrete paving slabs. Paving slabs used in sidewalks and plazas are often larger than 12 in., typically having one or both dimensions at 16, 18 or 24 in. (400, 450 or 600 mm) and are generally 1.5 to 2 in. (38 to 50 mm) thick. Information on slab size recommendations for vehicular applications is available in Tech Note PAV- TEC-024: Structural Design of Segmental Concrete Paving Slab and Plank Pavements Systems. Often the paving units are “gauged” or ground on the bottom by the manufacturer to ensure consistent thicknesses among all the units. These types of paving slabs require a very smooth and even concrete base. A tack coat is typically not used prior to placing, screeding and compacting the hot bitumen-sand mix. A neoprene adhesive is applied to the bituminous sand bedding, after it has cooled, to create a securely bonded system. Figure 18 illustrates paving slabs placed on the adhesive over the bitumen-sand bedding. After placement of the slabs directly on the bituminous-sand or on the adhesive, the joints are typically filled with concrete sand or stabilized joint sand. The slabs are compacted with a roller compactor or small plate compactor with rollers attached to help spread the compaction force and prevent cracking of the paving slabs.
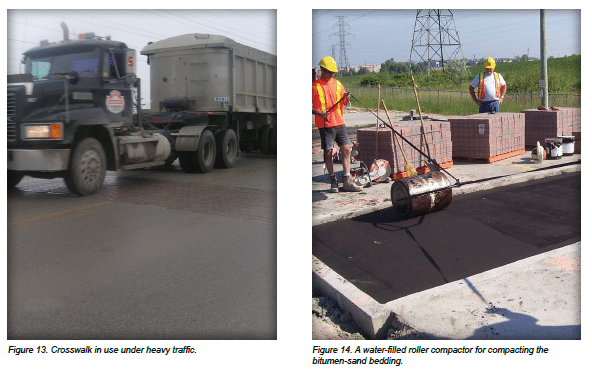
This method is superior to using a sand-cement mixture for the bedding over a concrete base as the sand-cement can be subject to deterioration from water, deicing salts and freeze-thaw cycles. Like its counterpart for vehicular applications, a bitumen-sand bedding with neoprene adhesive is more expensive, but it provides a very low-maintenance solution to rigid segmental concrete pavements, even in severe climates.
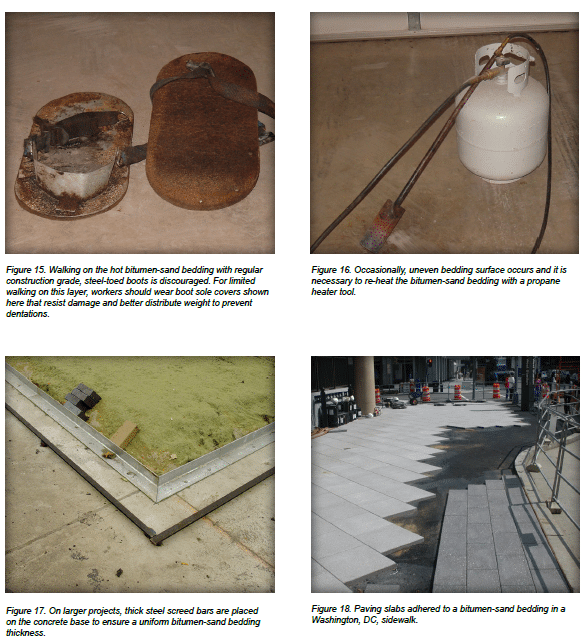
MAINTENANCE OF BITUMINOUS-SET INSTALLATIONS
The neoprene-asphalt adhesive bonds to the concrete pavers and bitumen-sand extremely well. This will make it almost impossible to remove from the concrete paver after it is applied, even if done so accidentally. Once installed and allowed to cure, it will be very unlikely that a paver can be removed without pulling up some of the bitumen-sand bedding material. Repair will typically require the removal and disposal of the pavers and bitumen-sand bedding and replacement with new material. Use of a propane torch as shown in Figure 16 along with a scraper may be required to soften and effectively remove the bitumen- sand from the concrete base. It is unlikely that the bitumen-sand hot mix will be available in a small batch so it may be necessary to use a fine gradation cold-patch material. Cold-patch can only be used in repairs and is not an acceptable substitution for hot- mix in the initial installation. Follow manufacturer’s installation instructions. Allow the cold-patch material to fully cure before applying the neoprene asphalt adhesive. A dry sand/cement mix is also acceptable for small area repairs such as individual pavers or slabs.
Construction tolerances, maintenance and repair recommendations are the same as ICP on sand-set bedding applications. Additional information on the repair and reinstatement is available in Refer to Tech Note PAV-TEC-006: Operation and Maintenance Guide for Interlocking Concrete Pavement. This reference includes information on preventative maintenance, identifying and remedying aesthetic and structural distresses and best practices for the disassembly and reinstatement of interlocking concrete pavement.
REFERENCES
Refer to the latest published ASTM and CSA standards and CMHA Tech Notes.
- ASTM–American Society for Testing and Materials International, Conshocken, PA. www.astm.org
- CSA–Canadian Standards Association, Rexdale, ON. www.csagroup.org
- CMHA-Concrete Masonry and Hardscapes Association, Herndon, VA. www.MasonryandHardscapes.org