INTRODUCTION
Concrete masonry can make a significant contribution to meeting LEED Green Building certification. Leadership in Energy and Environmental Design (LEED) is a voluntary rating system developed by the United States Green Building Council (USGBC) to evaluate a building’s environmental impact and performance. LEED provides design guidelines and third-party certification for defining what constitutes a “green” building. LEED’s overall goals are to improve: occupant well-being, the environmental impacts and the economic return of new buildings. USGBC offers several green building certification programs, each tailored to a specific market or application.
LEED version 2.2 will remain in effect until LEED 2009 is completed, around September 2009. Once LEED 2009 is active, version 2.2 registered projects can continue to certification as version 2.2 projects. This TEK provides details on LEED for New Construction & Major Renovations 2009 (LEED NC 2009) (ref. 1).
The USGBC has incorporated several changes into LEED 2009. These major changes are:
- Prerequisite and credit harmonization across rating systems (LEED Bookshelf). The intents and requirements for common prerequisites and credits among the various rating systems (i.e., New Construction, Schools, Retail, etc.) have been standardized to minimize differences or contradictions between rating systems. There are still unique prerequisites and credits in each rating system. In addition to harmonization, credit interpretation requests (CIR) that have set precedents or shown a need for clarification have been incorporated.
- A set schedule for updating the rating systems is being established, similar to building code development schedules.
- The quantity and distribution among the categories of points was changed to better reduce or improve a buildings environmental impact. These changes are most readily seen in the increase in the total number of points and in the allocation of points in each category. One of the major tools for weighting the categories was TRACI (Tool for the Reduction and Assessment of Chemical and Other Environmental Impacts), established by the EPA.
- The new Regional Priority category provides an opportunity for a project to achieve credit for addressing regional environmental concerns. The details on this category are still being finalized as the USGBC councils and chapters assemble and submit their requests to the USGBC.
LEED NC 2009 is comprised of seven categories each with its own prerequisites and credits. The prerequisites in all categories must be met to earn LEED certification. Using concrete masonry and concrete hardscape products can contribute to certification in the following LEED categories: Sustainable Sites, Energy & Atmosphere, Materials & Resources, Innovation and Design, and possibly Regional Priority*.
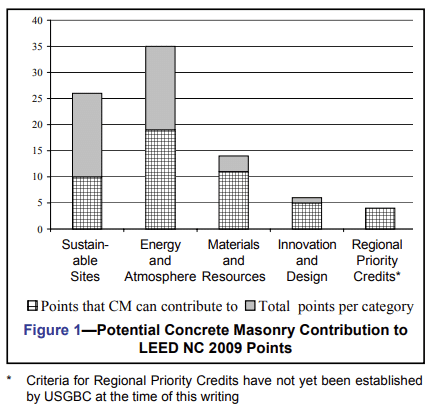
POINTS FOR CERTIFICATION
LEED NC 2009 provides a checklist of mandatory prerequisites as well as voluntary credits in seven basic categories: Sustainable Sites, Water Efficiency, Energy and Atmosphere, Materials and Resources, Indoor Environmental Quality, Innovation and Design Process, and Regional Priority Credits. Projects earn one or more credits by meeting or exceeding a checklist item’s technical requirements. Figure 1 illustrates the categories where concrete masonry products can contribute.
Points for voluntary credits add up to a final score which can earn the building one of four possible levels of certification. As shown in Figure 1, concrete masonry and hardscape products can make a significant contribution to LEED certification. A project must earn at least 40 points for LEED certification. Silver (50 pts), gold (60 pts), and platinum (80 pts) certification levels are also available. There are a total of 110 points available from the seven credit categories.
EARNING LEED POINTS
The following sections briefly describe how concrete masonry and hardscape products can contribute to earning points in each of the LEED credit categories.
Sustainable Site Prerequisite—Construction Activity Pollution Prevention
Reducing pollution due to construction activity is a prerequisite. Pollution includes soil erosion, waterway sedimentation and dust. Articulated concrete block (ACB) and open grid pavers can be used for soil erosion control and dust control. See References 3 and 4 for more information.
Sustainable Site Credit—Development Density
Developing an urban lot in lieu of an undeveloped “greenfield” area can earn a project one point towards certification. Concrete masonry and retaining walls enable designs that take advantage of small, irregularly shaped lots, where access and open area are often at a premium. Concrete masonry, because of its relatively small modular size does not require large equipment for delivery or placement, nor are large staging areas required for construction.
Sustainable Site Credit—Site Development
The overall goal of this credit is to preserve or restore natural habitats and to promote biodiversity. There are two parts to this credit, Protect or Restore Habitat and Maximize Open Space, each worth one LEED point.
On greenfield sites, segmental retaining walls and/or cantilever retaining walls can be used to limit cut and fill requirements. Reducing cut and fill operations preserves habitat and limits the disturbed area.
A second point can be earned by exceeding the local zoning requirement for open space by 25%. This 25% threshold can be met by reducing the site disturbance or by creating vegetated open space (the credit also provides requirements for projects where no local zoning requirement exists). Once again, retaining walls can limit site disturbance by reducing the amount of slope alteration.
For urban projects earning the Development Density credit, pedestrian hardscape areas, such as those provided by concrete pavers, can be counted as open space, although only 25% of the open space can be hardscape. Wetlands and ponds may count as open space if the side slope ratio does not exceed 1:4 and are vegetated. Articulated concrete block is well suited to wetland and pond construction.
Sustainable Site Credit—Stormwater Management
The intent of this credit is to limit disruption of natural hydrology by reducing stormwater runoff quantity and by improving the quality of stormwater runoff, through methods such as reducing impervious cover, increasing on-site infiltration, and managing stormwater runoff. One of the LEED-suggested strategies is to use permeable paving that promotes infiltration.
The requirement for controlling stormwater rate and quality is implemented either by limiting the post-development peak discharge rate or by implementing a plan that protects the receiving streams from excessive erosion.
An additional point may be earned by implementing Best Management Practices to capture and treat at least 90% of the average annual rainfall and removing 80% of the post development suspended solids.
Pavements are major contributors to stormwater runoff, and permeable pavements that directly pass water from the pavement surfaces to the underlying soil can help alleviate runoff. Benefits of permeable pavements include reduced stormwater runoff, direct recharge of underlying groundwater systems, partial treatment of pollutants in the runoff and increased usable space. Both permeable pavers and open-cell pavers (also known as turf stone or grid pavers) offer the option of replacing impermeable pavement with permeable pavement. These pavers can help earn one point each for reducing stormwater runoff and for treatment of stormwater. References 4, 5, and 6 provide more detailed design information for these pavements.
For the protection of receiving stream channels, ACB products can effectively reduce soil erosion and allow for a protected and
vegetated area.
Sustainable Site Credit—Heat Island Effect, Non-Roof
Urban heat islands are localized areas of high temperature, caused by the retention of solar energy on constructed dark surfaces. The effect is elevated temperatures in urban areas and a greater energy demand for cooling.
LEED offers one credit point for non-roof heat island reduction on projects if 50% or more of the site hardscape (including roads, sidewalks, courtyards and parking lots) are either shaded or use paving materials with Solar Reflectance Index of at least 29. Typical values for SRI are 35 for new gray concrete and 19 for weathered (unclean) concrete.
The SRI requirement can be met either by using light-colored concrete pavers in lieu of asphalt; or by using open-cell pavers, which can support grass or other plant materials in the pavers’ open grid areas. The open cell pavers must be considered at least 50% pervious.
Energy & Atmosphere Prerequisite—Minimum Energy Performance
This prerequisite requires a 10% improvement (for new construction) or a 5% improvement (for major renovations) over the ASHRAE 90.1 2007, Appendix G, Building Performance Rating Method (ref. 7). There are two other options for meeting this prerequisite: using the ASHRAE Advanced Energy Design Guide appropriate to the building type; and using the Advanced Buildings Core Performance Guide by the New Buildings Institute (NBI) (refs. 8, 9). These publications are prescriptive design guides that have specific building size and usage criteria.
The intent of these credits is to improve energy efficiency beyond ASHRAE 90.1-2007. Energy savings attributable to thermal mass inherent in concrete masonry construction contribute to this goal when used in conjunction with passive solar heating and/or ventilation cooling. Because concrete masonry has high thermal mass and specific heat, it provides very effective thermal storage. Masonry walls remain warm or cool long after the heat or air-conditioning has shut off. This, in turn, can effectively: reduce heating and cooling loads; improve occupant comfort by moderating indoor temperature swings; and shift peak heating and cooling loads to off-peak hours.
Using ASHRAE/IESNA Standard 90.1 Appendix G, Performance Rating Method, entails using a comprehensive, whole-building analysis software simulation program, capable of projecting the building’s energy consumption and associated costs based on an hour-by-hour simulation of a full year of weather data. Examples of such programs include DOE-2 and BLAST. These programs can accurately model concrete masonry’s thermal mass and predict the associated energy savings. These energy simulations have been used to demonstrate in many cases that, with all other variables kept the same, a high mass concrete masonry building can be heated and cooled using less energy than a similar frame building. See References 7 and 10 for more information.
Energy & Atmosphere Credit—Optimize Energy Performance
As many as 19 points can be achieved under this credit by incrementally increasing the energy efficiency of the building by 12 44% for new construction using Appendix G of ASHRAE 90.1-2007. One point is awarded for each 2% improvement. The Advanced Energy Design Guide and the Advanced Buildings Core Performance Guide can be used to achieve this credit. However, using these guides limits the potential points earned to 3.
Note that for the purposes of this credit, savings attributable to the building thermal envelope are cumulative, and so are added to savings from high efficiency HVAC, heat recovery equipment, daylighting, etc. Thus, all incremental improvements contribute toward project certification.
Materials & Resources Credit—Building Reuse
The building reuse credit is intended to extend the life of the existing building stock, thereby conserving resources, reducing waste and reducing the environmental impacts of new construction. Credits are earned when developers maintain the majority of an existing building’s structure and envelope. The building envelope is the exterior skin and framing excluding window assemblies and non structural roofing.
This credit is often obtainable when renovating buildings with exterior concrete masonry walls, because concrete masonry is an exceptionally durable material with a life cycle measurably longer than many other building envelope products. Concrete masonry construction provides the opportunity to refurbish the building should the building use or function change, rather than tearing down and starting anew.
Three points are available under this credit. These points are awarded based on the percentage of building reused. One point is awarded for 55% reuse, 2 points for 75% reuse, and 3 points for 95% reuse. An additional point is available if at least 50% of the interior, non-structural items remain. The percentages are based on the area of the completed building (existing and additions).
Materials & Resources Credit—Construction Waste Management
This item encourages contractors to divert demolition and landclearing debris from landfills and incinerators.
The construction waste management credit is awarded based on recycling or salvaging at least 50% of construction waste, based on either weight or volume. Because concrete masonry is a relatively heavy construction material and can be recycled into aggregate for road bases or other concrete products, pipe bedding or construction fill, this credit is obtainable either when buildings with concrete masonry are demolished or, in new construction when saw-cut scraps and broken pieces of concrete masonry are crushed and reused. In addition, intact and unused concrete masonry units can be redirected to other projects or donated to charitable organizations such as Habitat for Humanity.
This credit is worth 1 point if 50% of the construction, demolition and land clearing waste is recycled or salvaged and 2 points for 75%.
Materials & Resources Credit—Materials Reuse
This checklist item encourages the reuse of salvaged materials on the project, such as crushed concrete masonry, and it awards one point if the value of all reused materials is at least 5% of the total value of materials on the project. Two points are awarded at the 10% threshold. Note that the same materials cannot be claimed for both the construction waste management credit, above, and the materials reuse credit on the same project.
Materials & Resources Credit—Recycled Content
The use of building products with recycled content can earn the project one or two points. To earn the point(s), the project must meet the threshold percentage (10% for 1 point; 20% for 2 points) based on the total of all building materials used in the project.
Concrete masonry can potentially incorporate recycled materials, with due consideration to ensure that the use of these materials does not adversely affect the quality of the masonry units or construction. Recycled materials can be used as a partial replacement for cement, or as aggregate.
A full discussion, including calculation methods for recycled content, is discussed in TEK 06-06B, Determining the Recycled Content of Concrete Masonry Products (ref. 11).
Materials & Resources Credit—Regional Materials
Using materials and products that are locally extracted and manufactured supports the use of indigenous resources and reduces environmental impacts of transportation. Concrete masonry materials are most commonly extracted and manufactured close to the jobsite, thus helping to fulfill this LEED credit.
The LEED requirement is to “specify that a minimum of 10% of building materials be extracted, processed & manufactured within a radius of 500 miles.” Concrete masonry usually qualifies, since block plants are often within 50 mi (80 km) of a job site. The percentage of materials is calculated on a cost basis. If only a fraction of a product or material is extracted/harvested/recovered and manufactured within the region, then only that percentage (by weight) contributes to the regional value.
Innovation and Design Process
The intent of this item is to provide design teams with an incentive to go beyond the LEED requirements and/or to award points for innovative strategies not specifically addressed in the LEED rating system. Examples that may qualify are: substantially exceeding the building energy performance criteria (Energy & Atmosphere Credit 1), or including characteristics not directly referenced by LEED, such as acoustic performance and life cycle analysis of materials used.
Potential strategies for achieving Innovation & Design points with concrete masonry and hardscape products include:
- Show concrete masonry’s advantage in life cycle environmental impact over other building materials such as steel and aluminum due to its durability, low maintenance, and low embodied energy.
- Address indoor air quality issues, by eliminating the need for paints with exposed concrete masonry walls, thereby reducing the potential for VOC (volatile organic compounds) emissions.
- Improve indoor air quality using concrete masonry due to the reduced potential for mold growth ( concrete masonry is not a food source food for mold) and concrete masonry’s ability to be cleaned instead of being replaced in the event of a mold incident.
- Show concrete masonry’s material usage efficiency by incorporating partial grouting and prestressed masonry design techniques.
- Demonstrate concrete masonry’s intrinsic acoustical characteristics. See Reference 12 for further information.
- Make a case for concrete masonry’s superior fire resistance and fire containment qualities. See Reference 13 for further information.
Regional Priority
These credits provide a means for addressing local environmental priorities. There are six credits, but no more than four can be earned per project. These credits will pertain only to certain geographic locals, and the projects must be located within the relevant region to be eligible. Details on these credits will be available on the USGBC web site, www.usgbc.com.
REFERENCES
- LEED 2009 New Construction for Member Ballot. U.S. Green Building Council, 2008.
- LEED-NC for New Construction v2.2 Reference Guide. First Edition, U. S. Green Building Council, October 2005.
- Articulated Concrete Block for Erosion Control, ACB-TEC-001-14 Concrete Masonry & Hardscapes Association, 2014.
- Construction of Permeable Interlocking Concrete Pavement Systems, PAV-TEC-018-22, Concrete Masonry & Hardscapes Association, 2022.
- Concrete Grid Pavements, PAV-TEC-008-21, Concrete Masonry & Hardscapes Association, 2021.
- Achieving LEED Credits with Segmental Concrete Pavements, PAV-TEC-016-016, Concrete Masonry & Hardscapes Association, 2016.
- Energy Standard for Buildings Except Low-Rise Residential Buildings, ANSI/ASHRAE/IESNA Standard 90.1-2007. American Society of Heating, Refrigerating and Air-Conditioning Engineers, Inc., 2007.
- Advanced Energy Design Guides. American Society of Heating, Refrigerating and Air-Conditioning Engineers, Inc. Available for free download from: http://www.ashrae.org/technology/page/938.
- Advanced Buildings Core Performance Guide. New Buildings Institute, 2007.
- Standard 90.1-2007 User’s Manual. American Society of Heating, Refrigerating and Air-Conditioning Engineers, Inc., 2008.
- Determining the Recycled Content of Concrete Masonry Products, TEK 06-06B, Concrete Masonry & Hardscapes Association, 2009.
- Sound Transmission Class Rating for Concrete Masonry Walls, TEK 13-01D Concrete Masonry & Hardscapes Association, 2012.
- Fire Resistance Rating of Concrete Masonry Assemblies, TEK 07-01D Concrete Masonry & Hardscapes Association, 2018.