INTRODUCTION
Manufactured stone veneer has the appearance of natural stone, but is manufactured from concrete. The veneer is increasing in popularity and being used aesthetically for commercial and residential applications, giving buildings a rich, upscale look.
Typical installations are shown in Figures 1 and 2 for concrete masonry and wood frame applications, respectively. There are a number of key installation/inspection points that must be followed to provide a properly performing system. This TEK addresses a number of those key points.
KEY INSTALLATION/ INSPECTION POINTS
1. Substrate Preparation
Wood- and Metal-Framed Applications
According to The Engineered Wood Association’s (APA) Installation of Stucco Exterior Over Wood Structural Panel Wall Sheathing (ref. 1), when wood structural panel sheathing (plywood or oriented strand board – OSB) is used as the substrate material, it must have a ⅛ in. (3 mm) gap between the sheets on all sides to accommodate wood sheathing expansion when it gets wet. Without the gap, wood swelling will cause the adhered masonry veneer finish to crack, compromising the water resistance of the finish. This will allow water entry and degradation of the substrate, the veneer and the framing. Additionally, the wood framing should be relatively dry at the time of installation, as drying of the wet substrate causes shrinkage which could lead to cracking of the finish. Also note that the International Building Code (ref. 11) limits the deflection of wall systems to L/240 for brittle finishes.
Concrete and Concrete Masonry Walls
Manufactured stone veneer can be directly applied to surfaces of concrete and concrete masonry if they are free of dirt, waterproofing, paint, form oil, or any other substance that could inhibit the mortar bond. They must have a rough texture to ensure a mortar bond. ICRI guideline number 03732 (ref. 5) discusses Concrete Surface Profile (CSP), a standardized method to measure concrete surface roughness. An ICRI CSP equal to or greater than 2 is usually acceptable. Typically, cleaning may be done with power washing and/or mechanical methods (i.e. shot or bead blasting). If a bondable surface cannot be achieved, attach lath and a scratch coat before installing manufactured stone veneer. Do not bond manufactured stone masonry veneer to clay masonry surfaces.
2. Water Management
ASTM C1780, Standard Practice for Installation Methods for Adhered Manufactured Stone Masonry Veneer, (ref. 3) requires two separate layers of water-resistive barrier (WRB) to be installed over wood sheathing in exterior applications. The standard also requires that the two separate layers be installed in shingle fashion. Starting from the bottom of the wall, the inner layer of WRB should be installed, along with flashings, to create a drainage plane. The upper layer of the WRB should lap the top of the lower layer by a minimum of 2 in. (51 mm). The vertical joints of the WRB must be lapped a minimum of 6 in. (152 mm). Inside and outside corners must be overlapped a minimum of 16 in. (406 mm) past the corner in both directions. The WRB should be installed in accordance with the manufacturer’s recommendations and be integrated with all flashing accessories, adjacent WRBs, doors, windows, penetrations, and cladding transitions. The outer layer of WRB is intended to keep the scratch coat from contacting the inner layer of WRB and may be of a different material than the inner WRB.
Drainage Wall Systems: Drainage wall systems also are a very effective means of keeping water from penetrating to the interior and diverting it to the exterior. These systems have a minimum drainage gap of 3/16 in. (5 mm) and a maximum drainage gap of ¾ in. (19 mm). When a system of this type is used, some building codes permit the use of a single WRB.
Other checkpoints for effective water management include:
- flashing at all penetrations, terminations and transitions, integrated with the WRB and water directed out of the system,
- proper overhang of capping mateials, and
- soft joints at dissimilar materials to accommod and soft joints at dissimilar materials to accommodate some movement and minimize incidental water penetration.
3. Proper Selection of Metal Lath by Weight and Style for Each Span and Application
ASTM C1063, Standard Specification for Installation of Lathing and Furring to Receive Interior and Exterior Portland Cement-Based Plaster (ref. 4) must be followed for properly performing manufactured stone veneer system. All lath must be self-furred or use self-furring fasteners to allow the mortar to completely fill and encase the lath.
All lath and lath accessories must be corrosion resistant, consisting of either galvanized or stainless steel materials or nonmetallic lath with a published evaluation report from an ANSI accredited evaluation service and be rated for use behind manufactured stone veneer. More detailed recommendations can be found in the Installation Guide and Detailing Options for Compliance with ASTM 1780 for Adhered Concrete Masonry Veneer (ref. 2).
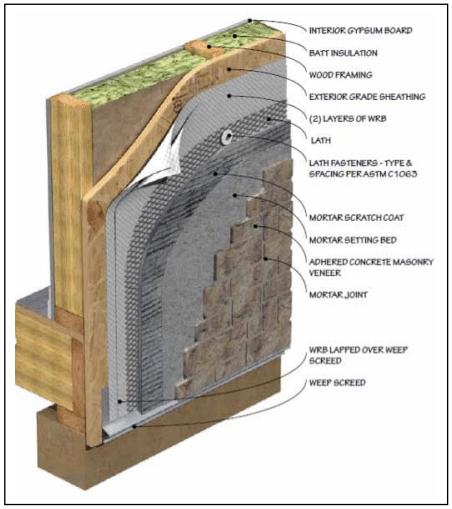
4. Proper Installation of Metal Lath
The installation of lath should be in accordance with ASTM C1063-14a (current version), Standard Specification for Installation of Lathing and Furring to Receive Interior and Exterior Portland Cement-Based Plaster (ref. 4). Metal lath should be applied horizontally (perpendicular to framing, if present) per manufacturer’s instructions, and should over- lap a minimum of 1 in. (25 mm) at the vertical seams and a minimum of ½ in. (13 mm) at the horizontal seams. The ends of adjoining lath places should be staggered. Lath should be wrapped around inside and outside corners a minimum of 12 in. (305 mm). Lath should be fastened every 7 in. (178 mm) vertically on each stud. The spacing of studs should not exceed 16 in. (406 mm). A similar spacing should be used on concrete or masonry wall surfaces. Do not end lath at inside/outside corner framing.
If not installed in accordance with ASTM C1063, alternate lath installation practices should be in accordance with manufacturer’s instructions. Acceptable installation practices for metal lath should be evaluated in accordance with AC191, Acceptance Criteria for Metal Plaster Bases (Lath) (ref. 12).
While recommendations vary, existing codes and standards do not stipulate the orientation of the lath “cups” (keys) once installed. More important than the orientation of the lath cups is ensuring the lath is embedded within, and bonded to, the mortar scratch coat for a successful AMSV installation. Lath is considered to be embedded within the mortar scratch coat when there is a ¼ in. (6 mm) nominal thickness of mortar between the back plane of the lath and the back plane of the scratch coat for at least one-half (50%) of the surface area of the installation.
When lapping paperbacked lath, be sure that lath is against lath and paper against paper. Paper backing inserted between lath at laps will prevent the mortar from going into the second lath and won’t lock the two sheets together. This can cause cracking in the manufactured stone veneer at the lath joint.
In the summer months, paperbacked lath must be protected from the sun and extreme heat to prevent the glue that attaches the paper to the lath from melting.
5. Proper Fastening of Lath
Proper fastener spacing and penetration is critical. Corrosion resistant fasteners (ref. 4) require a minimum ¾ in. (19.1 mm) nail penetration into wood framing members, a minimum ¾ in. (19.1 mm) staple penetration into wood framing members, or minimum a ⅜ in. (9.5 mm) penetration of metal framing members. Fasteners must have heads large enough to properly engage the lath.
Note that fasteners must be anchored into the framing members and are to be spaced no more than 7 in. (178 mm) on center per ASTM C1063 (ref. 4). Wood and gypsum sheathing do not have enough holding power to fully support the lath and manufactured stone veneer. A fastener attached only to the sheathing can work loose, particularly if the sheathing becomes wet. Proper fastening will help ensure that the veneer does not become detached during high wind events.
Fastener type and size is also very important. For installation directly to wood framing members, ASTM C1063 allows for the use of 1 ½ in. (38 mm) roofing nails to horizontal framing members. Vertical applications require the use of 1-in. (25-mm) roofing nails, 1-in. (25-mm) staples with minimum ¾-in. (19-mm) crowns, or 6d common nails driven to a penetration of at least ¾ in. (19 mm) and bent over to engage at least three strands of lath.
Where welded or woven wire lath is installed, rest the wire on the fastener for best performance rather than installing the fastener above the wire.
For fastening lath to steel supports, reference is made to ASTM C954 (ref. 6) by ASTM C1063 for screw information. Per that standard, lath can be wire-tied to the member with 18-gauge tie wire. Whether wire or screws are used, the maximum allowed spacing should be maintained, and once again all fastening must be corrosion resistant and penetrate into the structural member. ASTM C954 also states that the screw shall have a minimum head size of 7/16 in. (11 mm) with either a pan or wafer head large enough to engage at least three strands of lath.
6. Clearances
The following minimum clearances are critical to the proper performance of manufactured stone veneer:
Exterior Stud Walls or Where Manufactured Stone Veneer Continues Down a CMU Foundation Wall with WRB and Lath:
a. 4 in. (102 mm) from grade/earth
b. 2 in. (51 mm) above paved surfaces such as driveways, patios, etc. This minimum can be reduced to ½ in. (13 mm) if the paved surface is a walking surface supported by the same foundation that supports the wall.
Exterior Concrete or Masonry Walls with or without Lath and Weep Screeds:
a. 2 in. (51 mm) clearance from grade or ½ in. (13 mm) from a paved surface.
7. Mortar Selection, Mixing and Application
- Choose the proper mortar Type for scratch coats and pointing mortars: ASTM C270 (ref. 7) Type N or S for sitemixed or ASTM C1714 (ref. 8) Type N or S for premixed mortar. Setting mortars are the same except that ANSI A118.1 or ANSI A118.4 also may be used (refs. 9, 10)).
- Mix the mortar properly and employ hot weather provisions when the ambient temperature is above 90°F (32°C) and cold weather provisions when the temperature is below 40°F (4°C).
- Apply the scratch coat with sufficient material and pressure to completely encapsulate the lath with a nominal thickness of ½ in. (13 mm), ensuring that the lath is completely encapsulated with mortar. Horizontally score the surface after the scratch coat is somewhat firm.
- If applying to a scratch coat on open studs, non-solid sheathing, or metal building panels, allow the scratch coat to cure 48 hours, then dampen it before applying the setting bed. The setting bed mortar can be applied directly to the scratch coat, to the back of the manufactured stone veneer units (back-buttering), or a combination of both application methods.
8. Setting Manufactured Stone Veneer Units
- Dampen the unit’s bonding surface and apply enough setting bed mortar to fully cover the back of the unit with ample squeeze-out between the units.
- Take care not to bump previously installed stones. If a unit is inadvertently moved after initial set has begun, it should be removed, mortar scraped off the unit and the scratch coat, and then reinstalled following the application process.
- Pay attention to weather conditions and adjust installation procedures for hot or cold weather as needed.
- If filled mortar joints are to be provided, add pointing mortar to fill in the joints after there is sufficient cure time of the installed units, when mild contact will not break the bond to the backup system. Tool the pointing mortar when thumbprint hard. Concave or V-groove tooling provides the best water penetration resistance. Filled mortar joints are recommended at schools and other public places as children tend to try climbing walls with unfilled joints.
- Clean off remaining mortar debris on the veneer surface with a dry, soft-bristled brush. To prevent mortar smearing, DO NOT use a wet brush to treat uncured mortar joints.
9. Environmental, Chemical, Cleaning and Other Abuse
Avoid exposing manufactured stone veneer to the following as they can result in discoloring or surface damage:
- de-icing chemicals, salt, or other harsh chemicals such as acid cleaners and pool chemicals,
- sprinklers and roof downspouts should be positioned to prevent frequent moistening of the units, and
- avoid installing in areas where the units may be kicked, scraped, or scuffed such as on stair risers.
INSPECTION CHECKLIST
For Wood or Steel Stud Wall Systems:
- Minimum ⅛ in. (3 mm) gap between sheathing panels.
- Minimum of two layers of a water resistive barrier (WRB) for exterior applications.
- Proper and sufficient lap of WRBs.
- Fasteners for lath placed into framing members with sufficient penetration.
- Corrosion-resistant lath, flashing, fasteners, and accessories.
- Lath cups facing up with at least ¼ in. (6 mm) space to backing.
- Proper and sufficient lap of lath and no WRB between lath at laps.
- Scratch coat of proper materials, proper thickness and completely encapsulating lath.
- Scratch coat scored horizontally after it is somewhat firm.
For Concrete Masonry or Concrete Wall Systems:
- Use lath if surfaces are not clean and free from release agents, paints and other bond breakers for bonding directly. See checklist items for lath above.
- If using lath and a WRB is needed, see checklist items for WRB above.
- If a scratch coat is needed if not using lath, see checklist items for scratch coat above.
For Concrete Masonry, Concrete and Stud Wall Systems:
- Dampen scratch coat and units before applying setting mortar with full coverage and squeeze-out between units.
- For placed units inadvertently bumped, remove stones and mortar and reinstall.
- For filled joints, apply pointing mortar after setting mortar has sufficiently cured. Tool joints when pointing mortar is thumbprint hard.
- Properly clean pointing mortar debris from veneer surface.
REFERENCES
- Installation of Stucco Exterior Over Wood Structural Panel Wall Sheathing. The Engineered Wood Association (APA), 2006.
- Installation Guide and Detailing Options for Compliance with ASTM C1780 for Adhered Manufactured Stone Veneer, 5th Concrete Masonry and Hardscapes Association, 2023.
- Standard Practice for Installation Methods for Adhered Manufactured Stone Masonry Veneer, ASTM C1780-14. ASTM International, 2014.
- Standard Specification for Installation of Lathing and Furring to Receive Interior and Exterior Portland Cement- Based Plaster, ASTM C1063-14a, ASTM International,
- Selecting and Specifying Concrete Surface Preparation for Coatings, Sealers, and Polymer Overlays, ICRI Technical Guideline No. 03732. International Concrete Repair Institute, 2009.
- Standard Specification for Steel Drill Screws for the Application of Gypsum Panel Products or Metal Plaster Bases to Steel Studs from 033 in. (0.84 mm) to 0.112 in. (2.84 mm) in Thickness, ASTM C954-11. ASTM International, 2011.
- Standard Specification for Mortar for Unit Masonry, ASTM C270-14. ASTM International, 2014.
- Standard Specification for Preblended Dry Mortar Mix for Unit Masonry, ASTM C1714/C1714M-13a. ASTM International, 2013.
- American National Standard Specification for Standard Dry-Set Cement Mortar, 1. American National Standards Institute, 2013.
- American National Standard Specification for Modified Dry-Set Cement Mortar, A118.4. American National Standards Institute, 2013.
- International Building Code. International Code Council,
- Acceptance Criteria for Metal Plaster Bases (Lath), AC191. ICC Evaluation Service, Inc., 2012.