INTRODUCTION
Foam plastic insulation is often used in exterior concrete masonry construction to improve steady state thermal performance (R-values), and in some cases to improve air and moisture infiltration properties as well. Because of their potential flammability and smoke generation in case of fire, the International Building Code (IBC) (ref. 1) imposes additional requirements on these materials when they are used in exterior walls. These requirements are covered in IBC section 2603.
Foam plastic insulations include both rigid board (expanded polystyrene, extruded polystyrene, polyisocyanurate) as well as open cell and closed-cell spray-applied or foamed-in-place insulations. They may be used on the interior, exterior or in the cores (as either inserts or foamed-in-place) of single wythe masonry walls, and in the cavities of masonry cavity walls.
Because these plastics are flammable, the IBC mandates that they be protected by fire-resistance-rated materials or assemblies in wall and roof assemblies, to prevent the plastic insulation from contributing to the spread of fire in a building.
This TEK describes the IBC requirements for assemblies containing foam plastic insulation and presents details of concrete masonry walls that comply with those requirements. Note that this TEK focuses on the requirements for masonry wall assemblies: there may be additional requirements for the insulation, such as flame spread index and labeling.
IBC REQUIREMENTS
IBC Section 2603 regulates the use of foam plastic insulation in all types of construction, both combustible and noncombustible, with the intent of limiting the spread of fire via these materials. For exterior walls, Section 2603 requires:
- a thermal barrier between foam plastic insulation and the building interior, which can be satisfied with a 1 in. (25 mm) minimum thickness of concrete or masonry,
- ignition testing for foam plastic insulations applied to wall exteriors, although assemblies protected with at least 1 in. (25 mm) of concrete or masonry on the exterior are exempt from testing, and
- successful testing in accordance with NFPA 285, Standard Fire Test Method for Evaluation of Fire Propagation Characteristics of Exterior Non-Load-Bearing Wall Assemblies Containing Combustible Components (ref. 2).
Note that there are two important exceptions to the requirement for NFPA 285 testing:
- Wall assemblies where the foam plastic insulation is covered on each face by a minimum 1 in. (25 mm) thickness of masonry or concrete and meeting one of the following:
a) there is no air space between the insulation and the concrete or masonry (as occurs with foamed-in-place insulation); or
b) the insulation has a flame spread index of 25 or less as determined by ASTM E84, Standard Test Method for Surface Burning Characteristics of Building Materials, or UL 723, Standard for Test for Surface Burning Characteristics of Building Materials, (refs. 3, 4) and the air space between the insulation and the concrete or masonry does not exceed 1 in. (25 mm). - One-story buildings meeting the following conditions: foam plastic with a flame spread index of 25 or less and a smoke-developed index of 450 max can be placed in exterior walls without a thermal barrier where it is covered with aluminum (at least 0.032 in. (0.813 mm) thick) or corrosion-resistant steel (at least 0.0160 in. (0.406 mm) thick), provided that the insulation is not thicker than 4 in. (102 mm), and that the building is equipped with an automatic sprinkler system.
Wall assemblies meeting the requirements listed under number 1 above and buildings meeting the requirements listed under number 2 are deemed to comply with the Section 2603 requirements. Note that in cases where there is less than 1 in. (25 mm) of masonry over the insulation, there are insulations available that will meet the NFPA 285 requirements.
NFPA 285 REQUIREMENTS
NFPA 285 addresses the possibility of fire entering wall cavities through door or window openings, igniting foam plastic insulation and spreading vertically to upper stories.
The test evaluates exterior wall assemblies for buildings required to have exterior walls of noncombustible construction. The test provides a method of determining the flammability characteristics of exterior nonloadbearing wall assemblies. It is intended to evaluate combustible components included within wall assemblies required to be noncombustible, under conditions of a fire originating in the building interior.
NFPA 285 evaluates four conditions:
- flame propagation over the exterior face;
- flame propagation within combustible components from one story to the next;
- vertical flame propagation on the interior wall surface from one story to the next; and
- lateral flame propagation from one compartment to the next.
To evaluate these conditions, a two-story wall assembly with a window opening on the first floor is constructed in the test assembly. After a 30-minute fire exposure with the burner in the window opening, recorded temperatures are compared to the Standard’s conditions of acceptance to determine compliance. Note that the test evaluates wall assemblies, not specific materials.

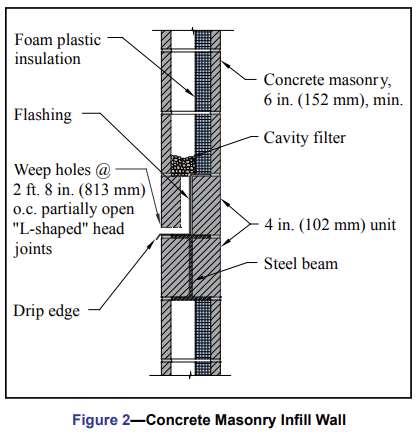
SINGLE WYTHE CONCRETE MASONRY WALLS
Single wythe walls may incorporate foam insulation in the cores of the masonry units as either rigid foam inserts or foamed in-place insulation. As discussed above, IBC Chapter 26 essentially requires a minimum of 1 in. (25 mm) of concrete or masonry on the interior and exterior of the foam insulation, as well as protection at headers to prevent ignition of the insulation above door and window openings.
When placed in concrete masonry cores, the foam plastic insulation is protected on the interior and exterior by the concrete face shells. Minimum face shell thickness for concrete masonry units is governed by ASTM C90, Standard Specification for Loadbearing Concrete Masonry Units, (ref. 5) as listed in Table 1. Table 1 shows that concrete masonry units of 6-in. (152 mm) thickness or greater provide the IBC-required 1 in. (25 mm) interior and exterior protection. Because of the small core size of 4-in. (102-mm) units, the cores of these units are rarely insulated. When insulation is placed in the cells of concrete masonry units and bond beams are provided at each story and lintels over each opening, the insulation is fully encapsulated. This meets the intent of the code to prevent the propagation of fire within wall cavities and no further isolation is necessary in this case.
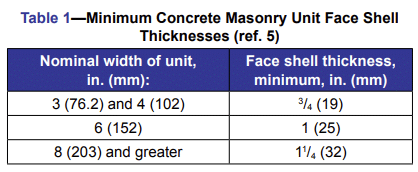
In single wythe construction, door and window headers are typically constructed using either a reinforced precast lintel or a reinforced concrete masonry lintel (shown in Figure 1). This detail provides concrete cover well over the 1 in. (25 mm) minimum required by Section 2603. The detail and level of protection would be similar with a precast concrete lintel. Refer to TEK 19-02B, Design for Dry Single Wythe Concrete Masonry Walls (ref. 6), for additional details on flashing single wythe walls.
MULTI-WYTHE WALLS
Multi-wythe concrete masonry construction is most commonly masonry cavity walls, which often incorporate foam plastic insulation in the cavity formed by the two masonry wythes. In this case, there is more than 1 in. (25 mm) of masonry on both the interior and exterior, so the focus for protecting the insulation is on the headers and jambs of window and door openings.
Per Building Code Requirements for Masonry Structures (ref. 8) concrete masonry veneer walls are to have a minimum specified 1 in. (25 mm) air space with special precautions to limit mortar overhangs inside the cavity to allow adequate drainage between the wythes. Exception b to NFPA 285 testing (see page 1) limits the air space between the insulation and the masonry to 1 in. (25 mm) maximum. Therefore, when exception b is being used, the designer should specify a 1 in. (25 mm) air space to meet both requirements.
Figure 3 shows a window top of opening detail in a concrete masonry cavity wall. In this case, 1 in. (25 mm) of mortar is slushed into the cavity below the insulation to provide the required level of protection. In addition, testing (refs. 7, 10) has shown that mineral wool fire safing covering insulation board exposed at openings in a masonry cavity wall is sufficient to pass NFPA 285 requirements. Note that mineral wool insulation cannot be exposed to the moisture in the drainage cavity. If used, it must be behind flashing or similarly protected.
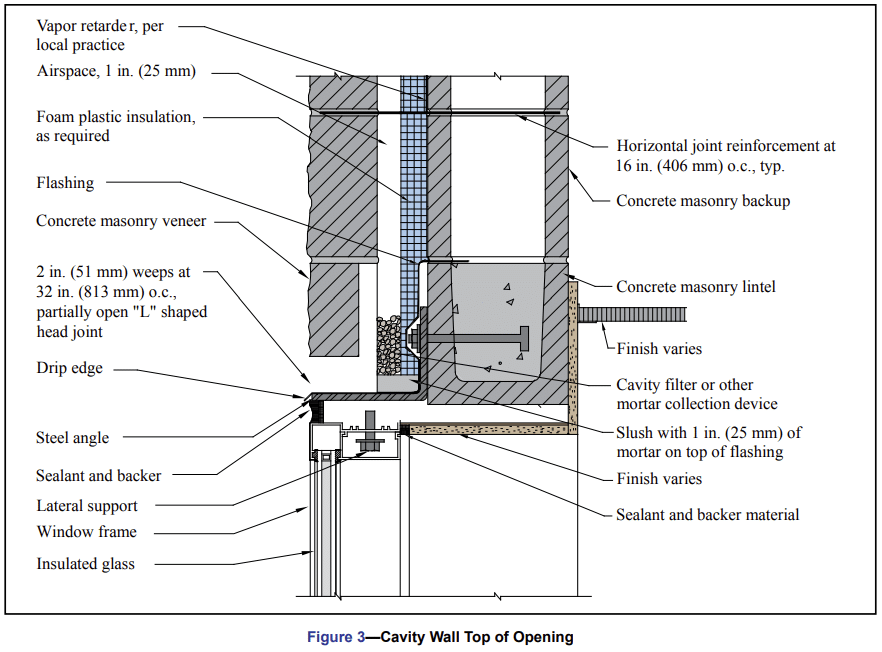
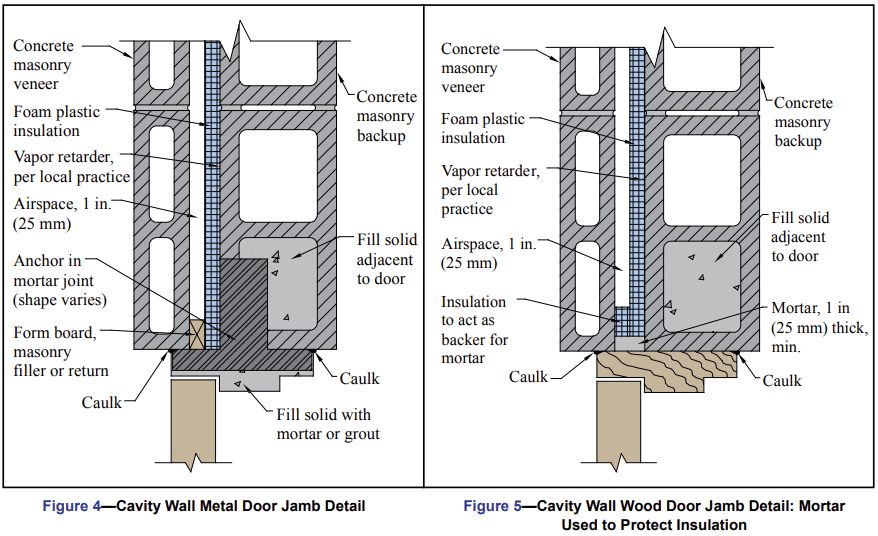
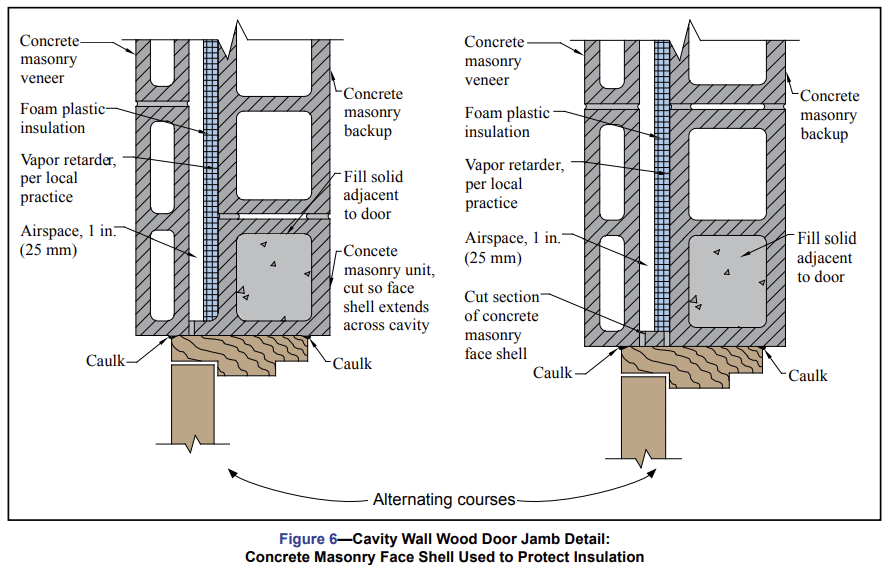
The jambs of metal doors (see Figure 4) are typically filled with mortar as the wall is constructed, again providing adequate protection for the insulation.
For wood door jambs, several options are shown in Figures 5 and 6. Figure 5 shows a detail where the insulation is held 1 in. (25 mm) back from the jamb. An additional piece of insulation bridges the cavity and acts as a backer for a 1 in (25 mm) layer of mortar. Another option is shown in Figure 6, where the unit adjacent to the jamb is turned 90o, and the unit is cut so that part of the face shell extends across the cavity, between the jamb and the insulation. On the alternate courses, a piece of the cut face shell can be mortared across the cavity to provide the protection. Wood window jamb details are very similar, as shown in Figures 7 and 8.
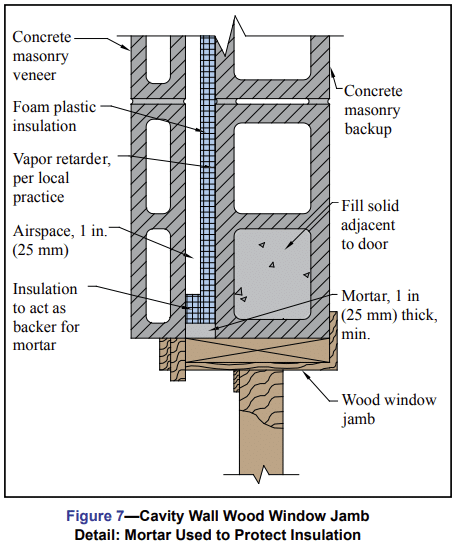
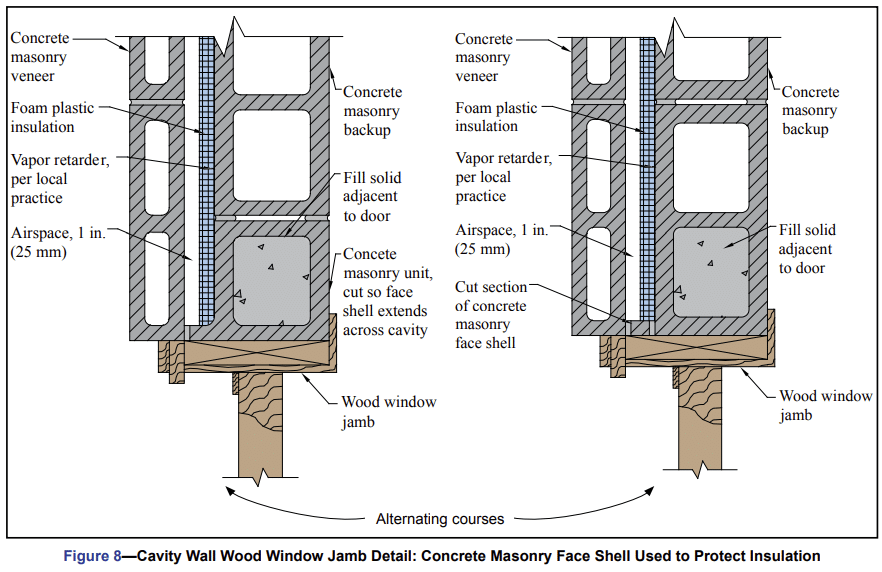
REFERENCES
- International Building Code. International Code Council, 2015.
- Standard Fire Test Method for Evaluation of Fire Propagation Characteristics of Exterior Non-Load-Bearing Wall Assemblies Containing Combustible Components, NFPA 285. National Fire Protection Association, 2012.
- Standard Test Method for Surface Burning Characteristics of Building Materials, ASTM E84-13a. ASTM International, 2013.
- Standard for Test for Surface Burning Characteristics of Building Materials, UL 723. Underwriter’s Laboratories, 2008.
- Standard Specification for Loadbearing Concrete Masonry Units, ASTM C90-13. ASTM International, 2013.
- Design for Dry Single-Wythe Concrete Masonry Walls, TEK 19 02B. Concrete Masonry & Hardscapes Association, 2012.
- NFPA 285-[06] Approved Wall Assemblies Using Foam Plastic Insulation From Dow, Tech Solutions 514.0. Dow Chemical Company, 2009.
- Building Code Requirements for Masonry Structures, TMS 402 11/ACI 530-11/ASCE 5-11. Reported by the Masonry Standards Joint Committee, 2011.
- Standard Test Method for Determining Ignitability of Exterior Wall Assemblies Using a Radiant Heat Energy Source, NFPA 268. National Fire Protection Association, 2012.
- Commercial Complete™ Wall System NFPA 285 Tested Wall Assemblies. Owens Corning Insulating Systems, LLC, 2012.